Mechanical Installation Manual (450, 525, 600)
5. Identify Installation Location
Installation Location Introduction
The performance of the Seakeeper Ride system is a direct result of the proper mounting location of the Controllers. It is vital to abide by the criteria in the Seakeeper Ride Installation Location Guide to choose the optimal mounting point for the Controllers. Optional use of the Seakeeper Ride Controller Locator Tool will assist with locating where the Seakeeper Ride system will sit on the boat Hull and how much room it will take in order to install. See the Seakeeper Ride | Controller Locator Tool Manual for further instruction on use.
For new production installations, please consult with the Seakeeper Applications Engineering Team or a naval architect for the proper location of the Seakeeper Ride Controllers according to the hull shape, hull type, engine configuration, and other relevant application details.
For refit installations, please review the following sections to determine the ideal location for the Seakeeper Ride Installation.
Note: For refit Seakeeper Ride installations, if there are trim tabs or interceptor, they MUST be removed in order to install Seakeeper Ride.
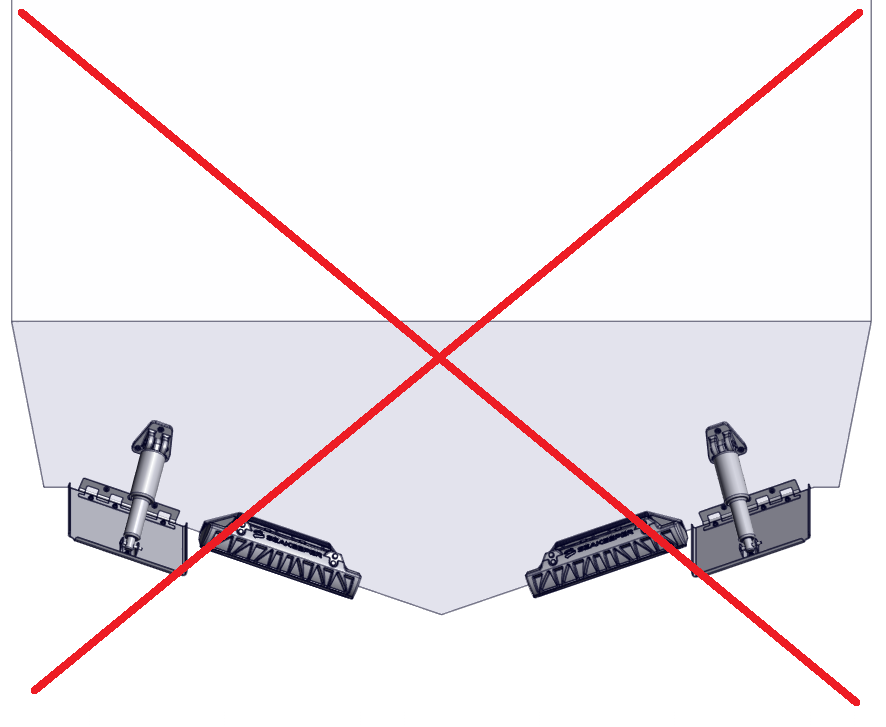
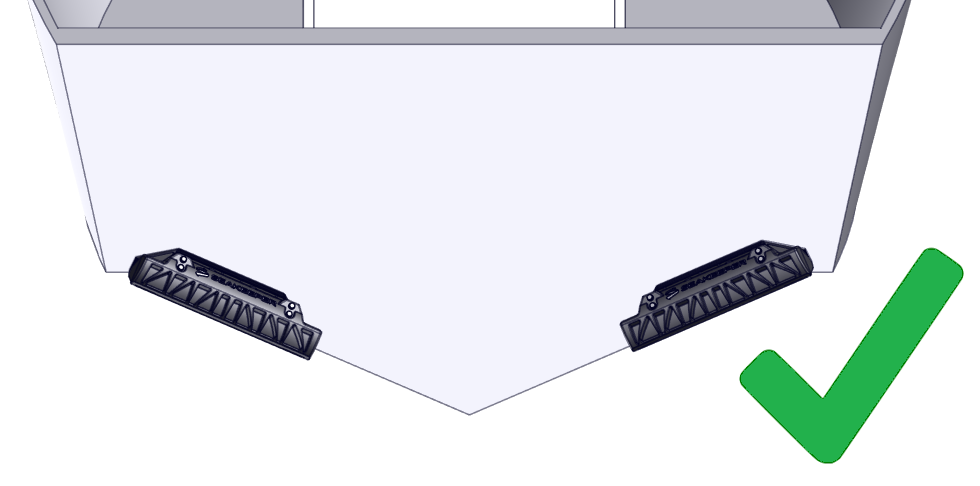
Figure 3 – Incorrect Seakeeper Ride Installation Between Trim Tabs vs. Correct Installation Near Chine
5.1. Longitudinal Location
The Seakeeper Ride Controllers will be mounted to the transom, the approximately vertical surface at the aft end of the running surface, as shown in the figures below.
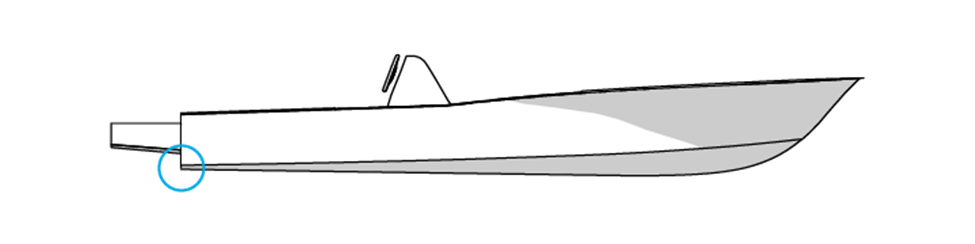
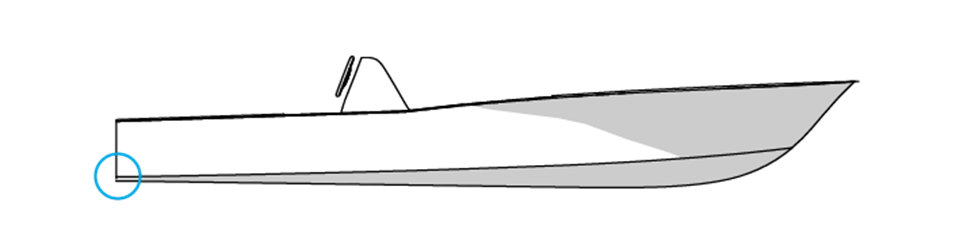
5.2. Vertical Location
Seakeeper Ride’s Controllers must be mounted so that the bottom surface of the Seal Plate (Item Number 2 below) aligns with the hull bottom. The goal is to have the Seal Plate acting like an extension of the hull bottom. The Seal Plate’s location is determined by the Transom Plate (Item Number 8 below), which is affixed to the transom and adjusted up and down during installation to allow for fine-tuning the location.
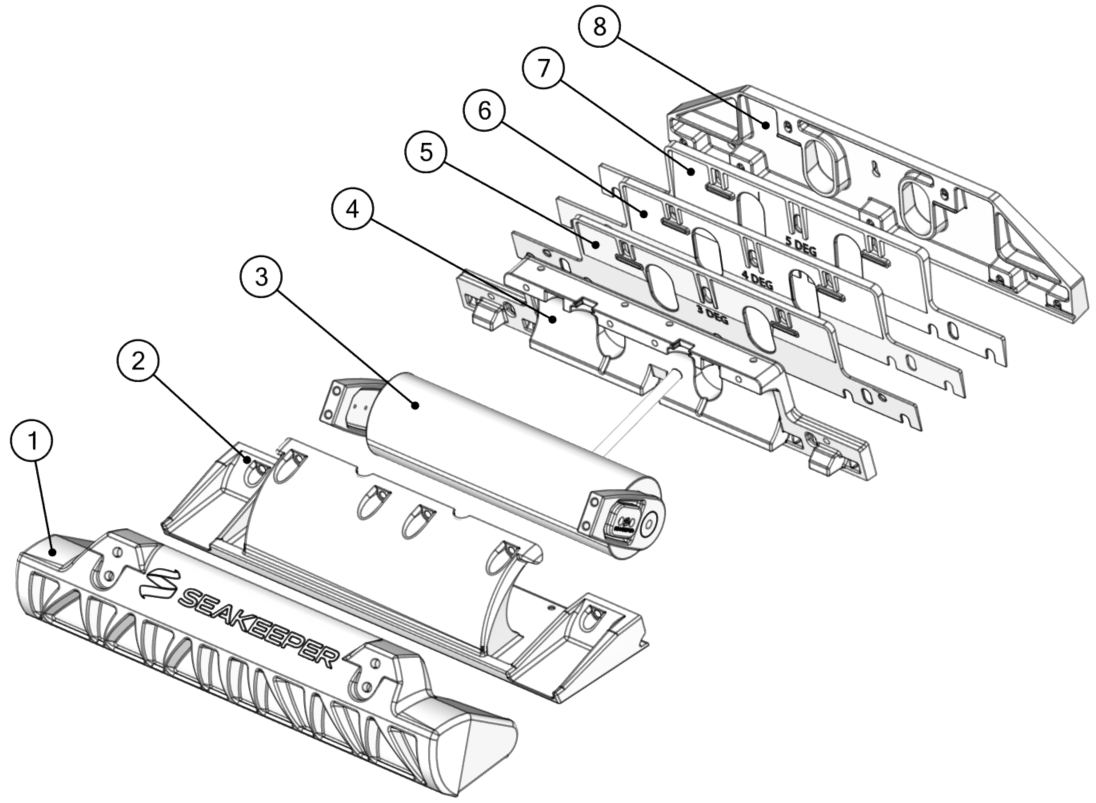
1) Blade
2) Seal Plate
3) Rotary Actuator
4) Actuator Plate
5) 5 Degree Wedge Plate
6) 4 Degree Wedge Plate
7) 3 Degree Wedge Plate
8) Transom Plate
The Ride Reference Line (RRL) is a guide for where the bottom of the Controller should be when mounted. The RRL is a representation of the bottom edge of the transom where it meets the running surface of the hull. Because of the unique shapes of different hulls, the RRL may not follow the bottom edge of the hull exactly. The following examples give guidance on where the RRL should lie on hull bottoms that are not perfectly straight.
An example transom with an exaggerated radius is shown below. The RRL is shown in blue and is the intersection of the two straight edges.
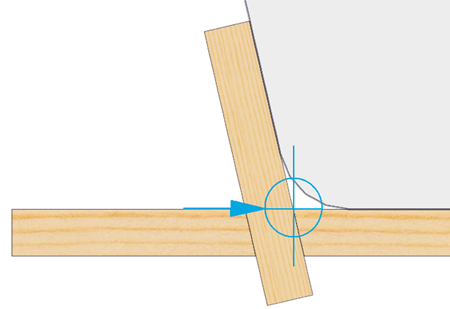
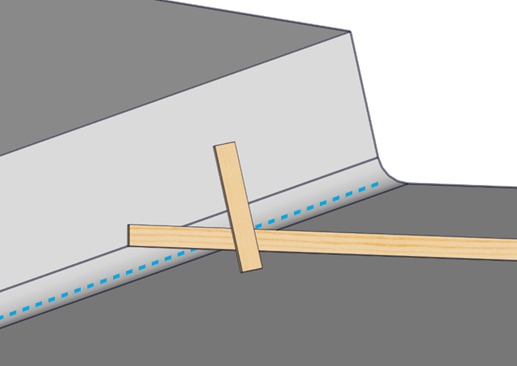
Figure 7 – Finding Reference Line with Straight Edges
Figure 9 to Figure 12 in the following section show a view from the stern of the vessel looking toward the bow. Label 1 indicates the bottom of the hull, Label 2 indicates the RRL, and Label 3 indicates the outline of the Transom Plate.
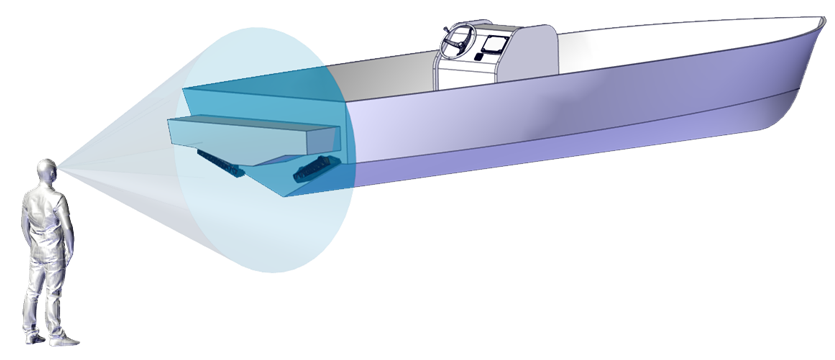
Strakes
For hulls with lifting strakes or spray strakes, they can be ignored for the placement of the equipment and determination of the RRL. Please note, large strakes which extend all the way to the transom can reduce the authority of the Seakeeper Ride equipment. Terminating the strake at least 12 inches forward of Ride maintains full system authority.
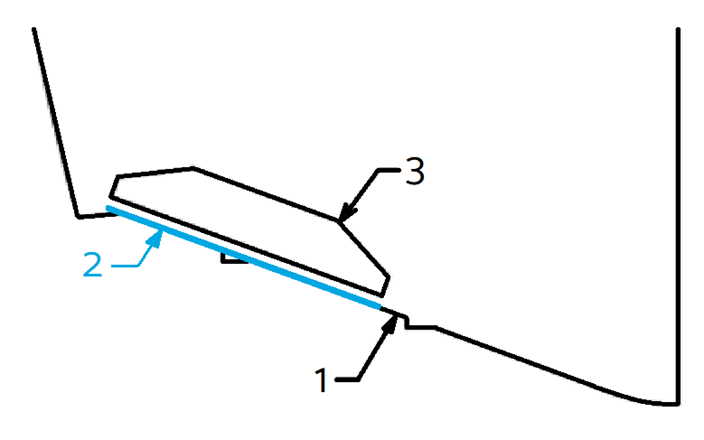
Concave and Convex Deadrise
The Seal Plates (Item Number 2 in Figure 6) have a straight design. Some hulls may have curvature along the deadrise which will cause the Seal Plate to show gaps between the deadrise at either the ends or center of the plate. The following sections describe how to find the RRL in concave and convex deadrise hulls.
Concave Deadrise
For vessels with concave curvature, the Seal Plate should be mounted such that the center of the Seal Plate is flush to the hull bottom and the ends of the Seal Plate are equidistant from the hull bottom (measurement A in the figure below). Measurement A must be 0.5 in. or less. More curvature decreases Seakeeper Ride Authority. For vessels with concave curvature, the RRL is defined as the tangent to the hull bottom, shown by the blue line.
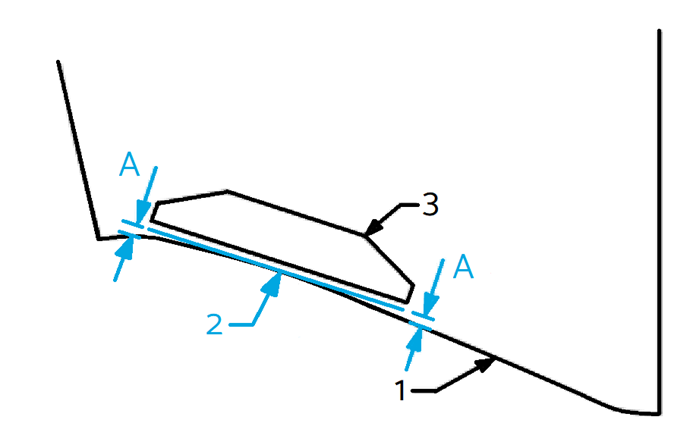
Convex Deadrise
For vessels with convex curvature, the ends of the Seal Plate should be mounted flush with the hull bottom with a gap between the center of the Seal Plate and the hull bottom (measurement B in the figure below). Measurement B must be 0.5 in. or less. More curvature decreases Seakeeper Ride Authority. For vessels with convex curvature, the RRL is defined as the straight line along the transom between inboard and outboard ends of the seal plate’s destination.
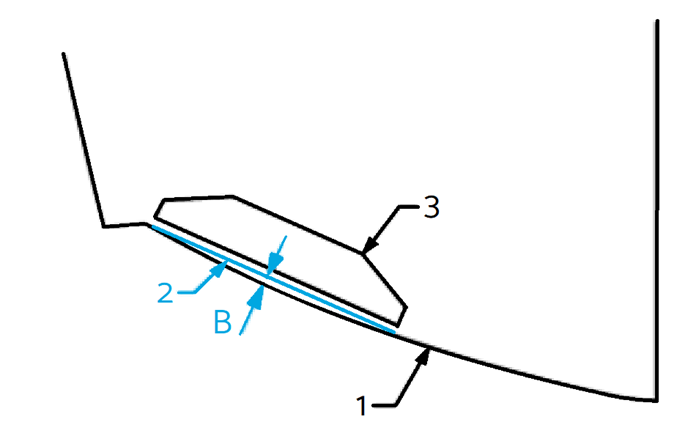
Variable Deadrise
Variable deadrise hulls are those where the running surface has breaks that run longitudinally. Generally, these hulls have decreasing deadrise angle in each successive panel moving outboard from centerline. Seakeeper Ride Controllers are capable of being mounted on variable deadrise hulls, so long as the following mounting conditions can be met:
- Distance from inboard edge of the Controller to the hull (Dimension A in the figure below) is 0.75 in. (19 mm) or less. This requirement only applies to vertical changes beneath the Controller.
- The portion of the Controller extending inboard of the deadrise break (Dimension B in the figure below) is 3 in. (76 mm) or less.
In hulls with a variable deadrise, the RRL is the highest portion of the deadrise that the Seakeeper Ride system will cover. See the figure below for this position. Because performance may degrade rapidly if these conditions are not met, please reach out to Seakeeper for guidance in this instance if a boat falls outside these parameters.

5.3. Beam-Wise Location
There are several hull features that should be considered when determining the location of the Controllers in a beam-wise orientation. As a general rule, the Controllers must be mounted as far outboard as possible, up to the chines (if the hull has chines).
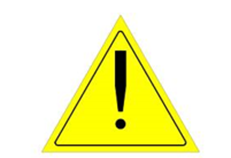
ATTENTION: Mounting the Controllers towards the centerline of the boat reduces the leverage the system has on the boat and severely reduces roll performance.
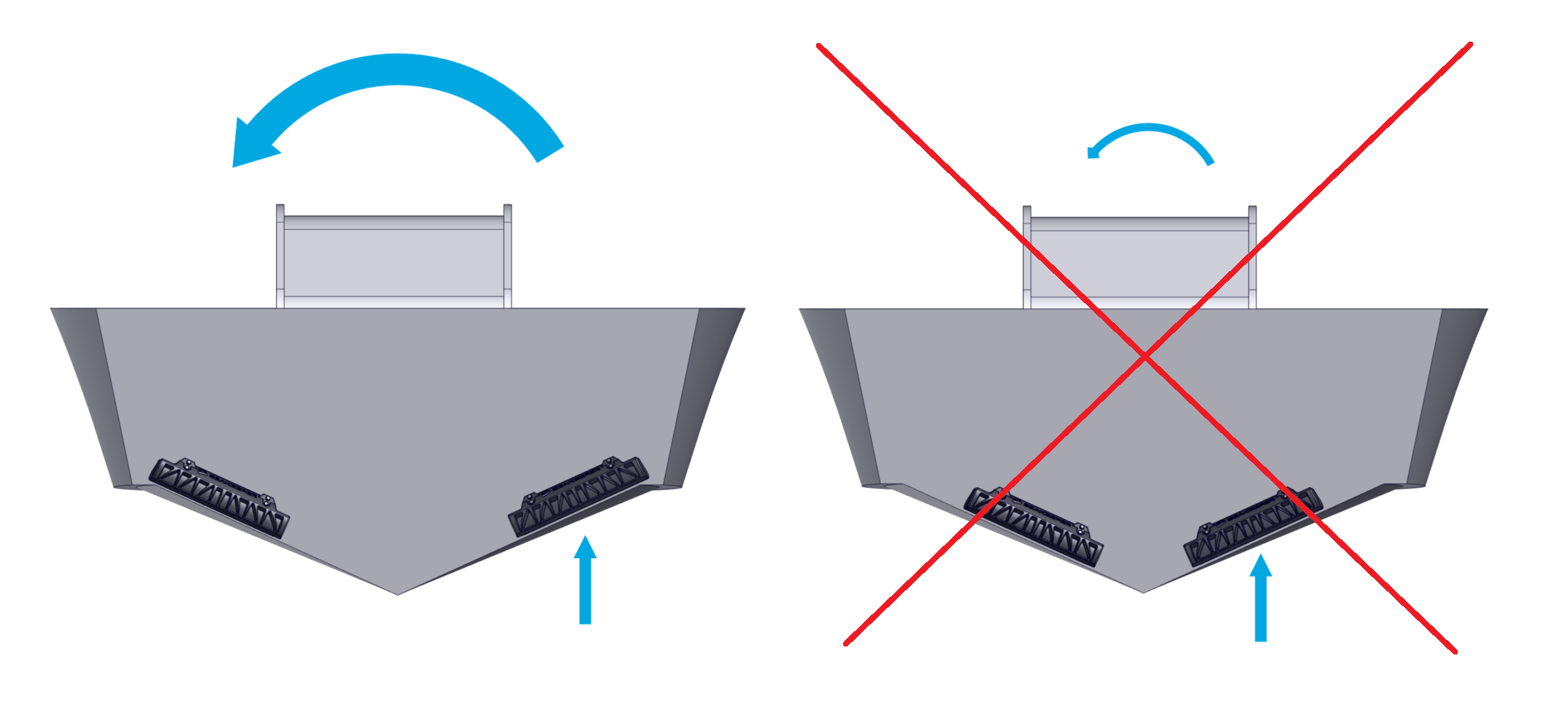
Chines
Based on the considerations of engine spacing and transom appendages, some installations will require the Controllers to extend outboard of the inboard edge of the chine. An overlap of the outboard chine of 1.5 in. (38 mm) is acceptable. For overlaps greater than 1.5 in. (38 mm), performance may degrade rapidly. The figure below illustrates placement of the outboard edge of the Controller with the following color code:
Green (Outboard of chine up to 1.5 in. (38 mm)) – Ideal
Yellow (Inboard of chine up to 1.5 in. (38 mm)) – Good
Orange (More than 1.5 in. (38 mm) from chine) – Acceptable*
Red (Overhanging Hull Side) – Unacceptable
*Controllers must NOT be mounted far enough inboard to reduce leverage, as outlined above.
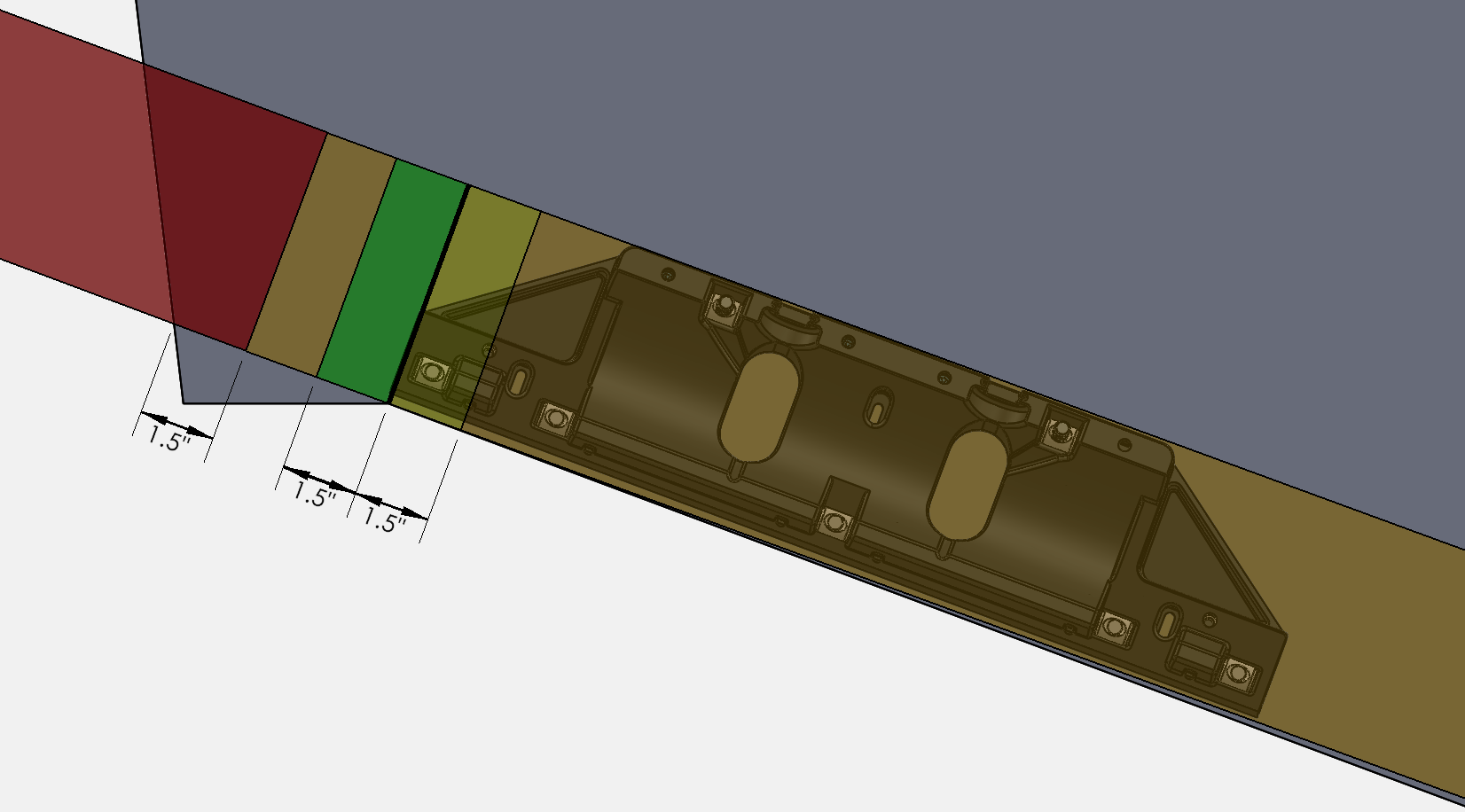
Hull Side Spacing
It is possible to have an installation where the Controller is mounted too far outboard causing water flowing around the hull side to interfere with the Controller and substantially reduce performance.
To avoid this issue, the Controller should be mounted at least 1.5 in. (38 mm) inboard of the hull side, as shown below.
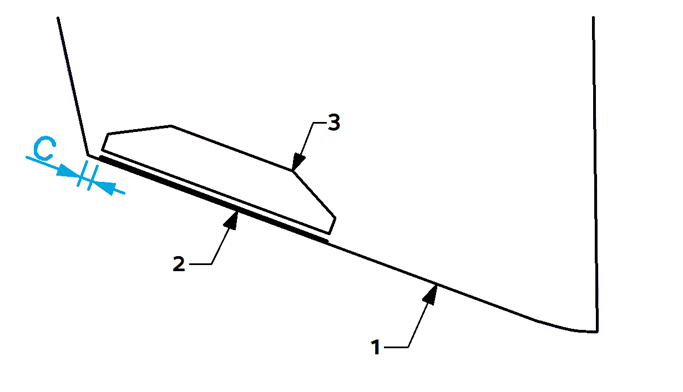
Engine Spacing
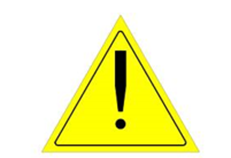
NOTE: Seakeeper has performed successful testing with Seakeeper Ride overlapping propellers significantly further than indicated below; however, because of the infinite variables (engine height, engine trim, engine longitudinal offset from Seakeeper Ride Controllers, propeller selection, propeller rotation, sea conditions, loading conditions, vessel characteristics, and more) which impact the interaction between Seakeeper Ride and propulsors, Seakeeper cannot provide more specialized guidance or blanket recommendation to install with more propeller overlap than indicated below. If the Builder, Owners, or Operators choose to install the Seakeeper Ride Controllers with more propeller overlap than indicated in the figure below, it may result in rpm/coolant fluctuation and/or engine faults. Please see the Operation Manual for additional detail on Seakeeper Ride’s potential impacts to propulsors.
Because the Controllers have the potential to change water flow into the boat’s propellers, the Controllers should be mounted as far from the propellers as possible. It is recommended that the inner edge of the Controller be mounted outboard of the diameter of the propeller tip (see the figure below). The line defining this instruction is the tangent line to the diameter of the propeller tip on the outboard side, perpendicular to the deadrise. Label 4 indicates the diameter of the propeller tip.
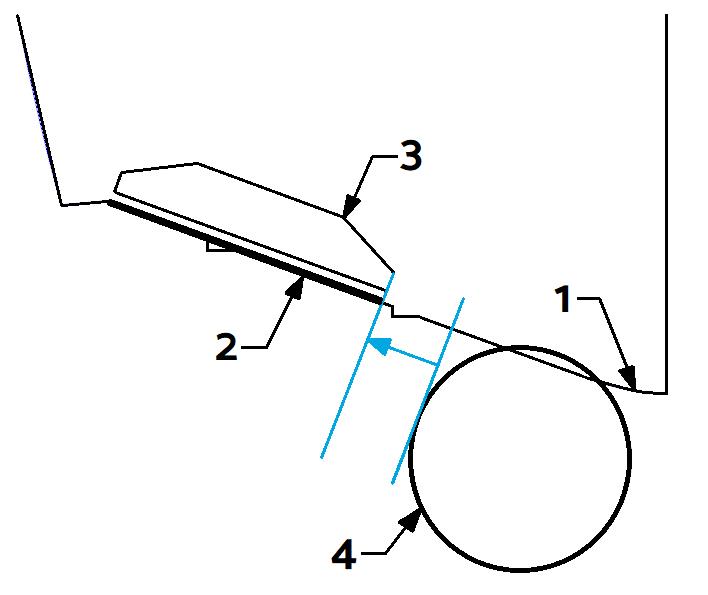
Note: Any obstructions preventing the installation of the Controllers or beyond the dimensions specified must be removed before continuing with the installation of Seakeeper Ride.
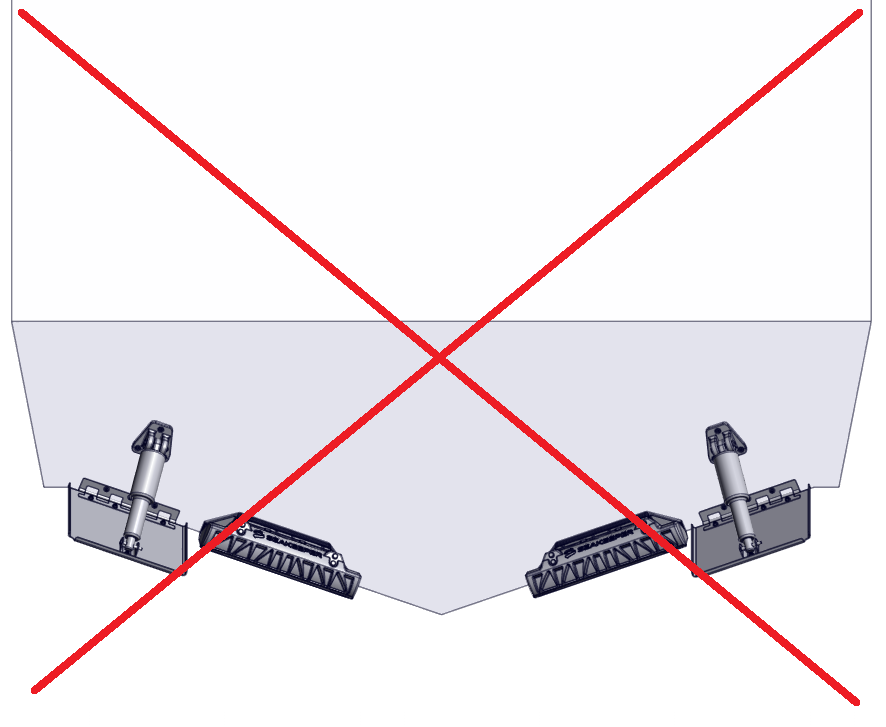
5.4. Overhead Clearance
Because the Controllers are mounted externally on the hull, there may be some installations where space must be cleared to create room for the Controllers. There must be at least 5 in. (127 mm) of clearance between the aft most running surface and any surface above where the Controller will be placed (this includes any bracket or similar hardware that hangs over the Controller). The Controller will extend aft of the hull by 8 in. (203 mm).
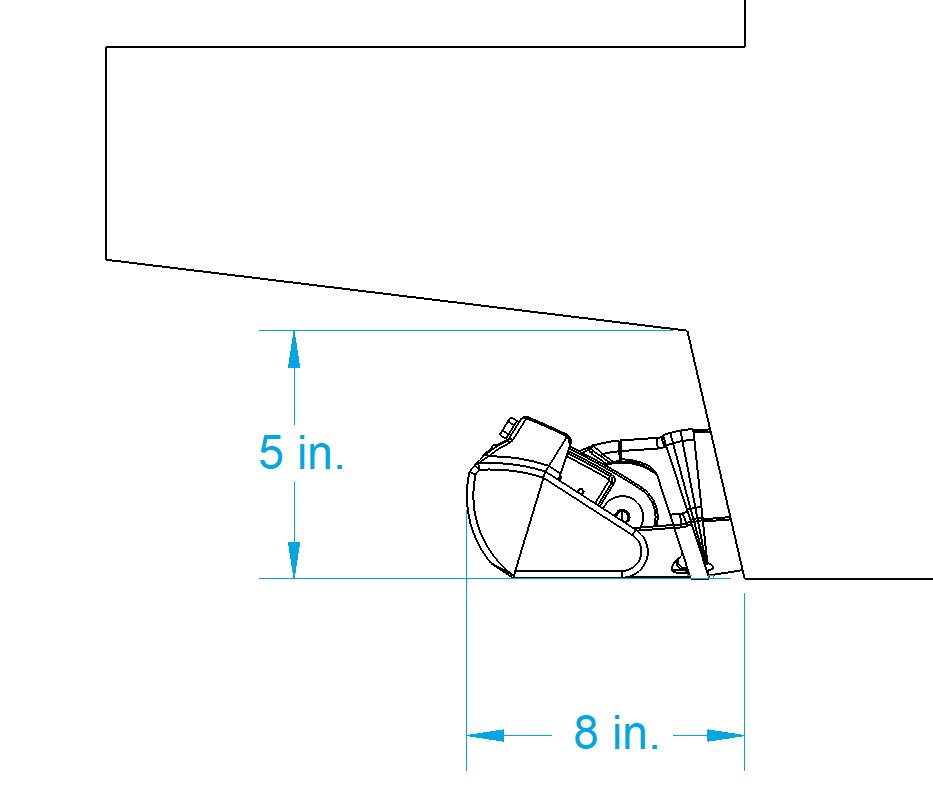
5.5. Loading and Storage Details
The Controllers should not be installed where they will carry any load of the boat while on bunks (i.e. a trailer, storage rack, or fork truck). If there is concern with bunks loading the Controllers:
Mount Upward – Seakeeper Ride can be mounted up to 1/8 in. (3.2 mm) up from the bottom of the hull with negligible effect on system performance.
Angle Upward – Seakeeper Ride can be mounted up to two (2) degrees angled upward from the bottom of the hull with negligible effect on system performance.
One or both of these mounting tolerances may be used to keep Seakeeper Ride from contacting the bunks and increase the longevity of the system.
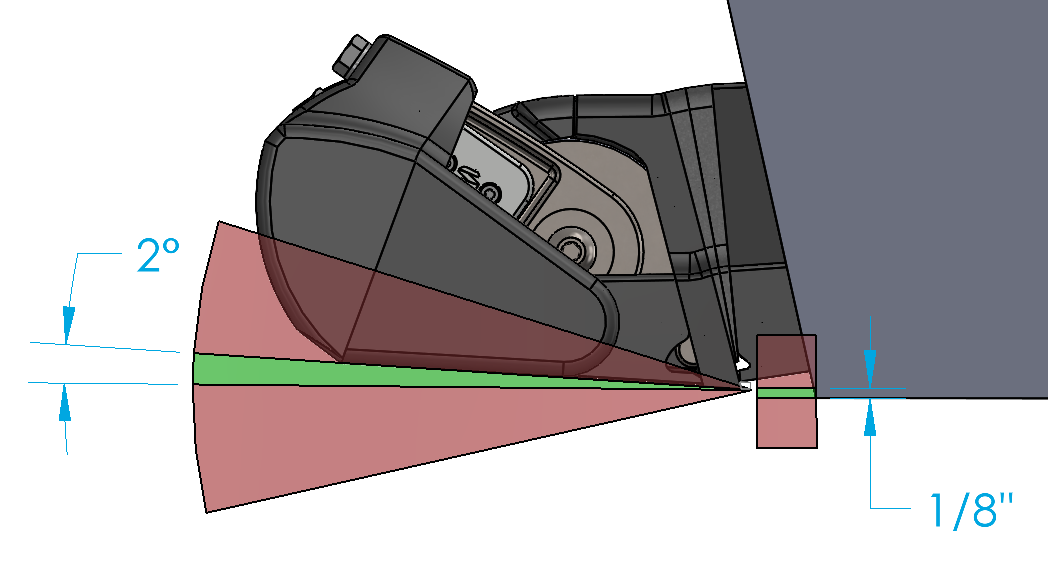
Seakeeper Ride will automatically retract the Blades when coming to a stop, meaning that they will be flush with the rest of the Controller and should not cause problems when placing the boat on bunks during normal operation in both Auto and Manual modes.
Setting Up the Trailer for Seakeeper Ride
Cut bunks short – If the bunks are too long, cut them to correspond with the end of the transom rather than extending aft.
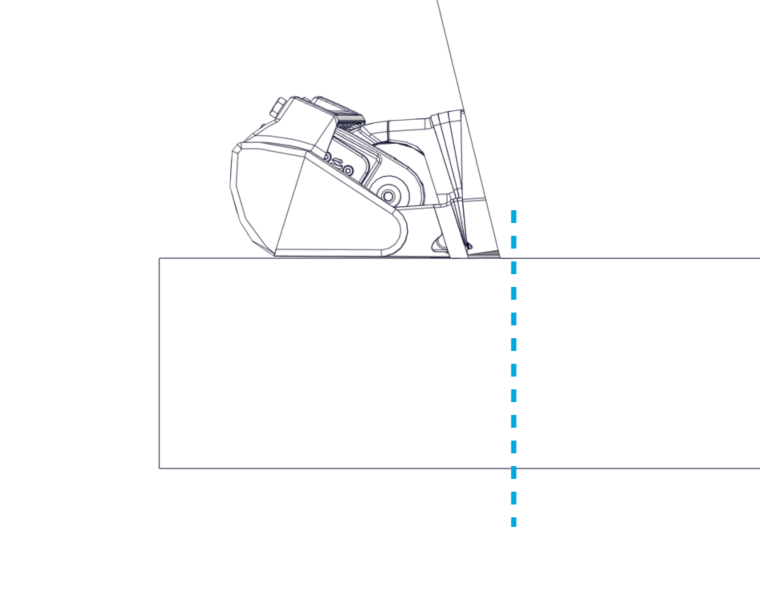
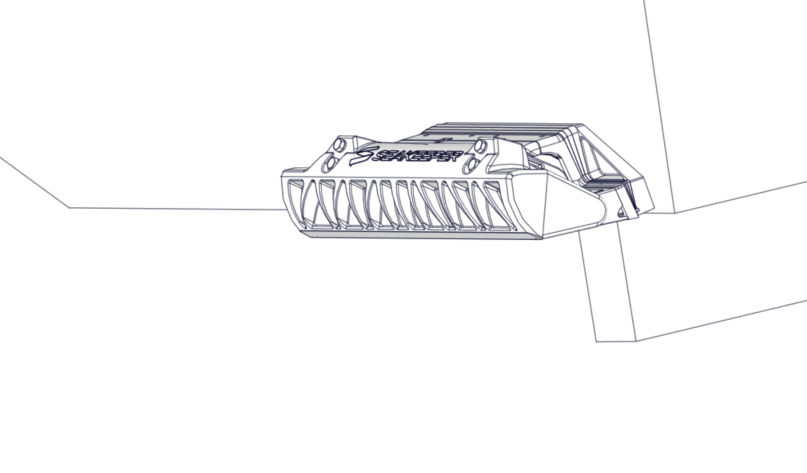
Figure 19 – Cutting Bunks Short
Cut bunks low – If the bunks cannot be cut shorter, bunks can be cut with a small recess below Seakeeper Ride to prevent excessive force on the Controller when going down the road.
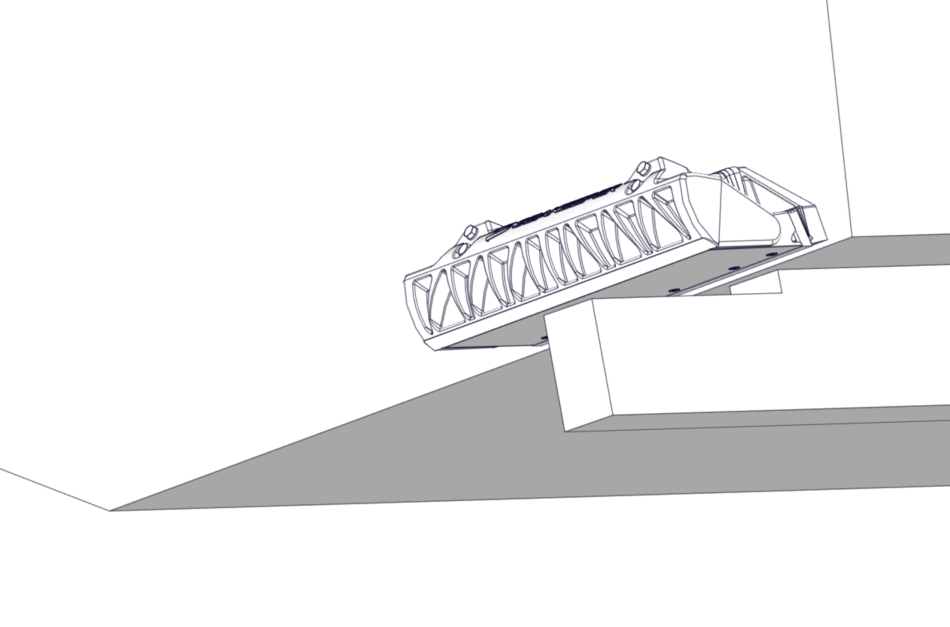
Do Not Place Tie-Down Straps Across Seakeeper Ride – Consider moving straps to cleats or to a different tie down point.
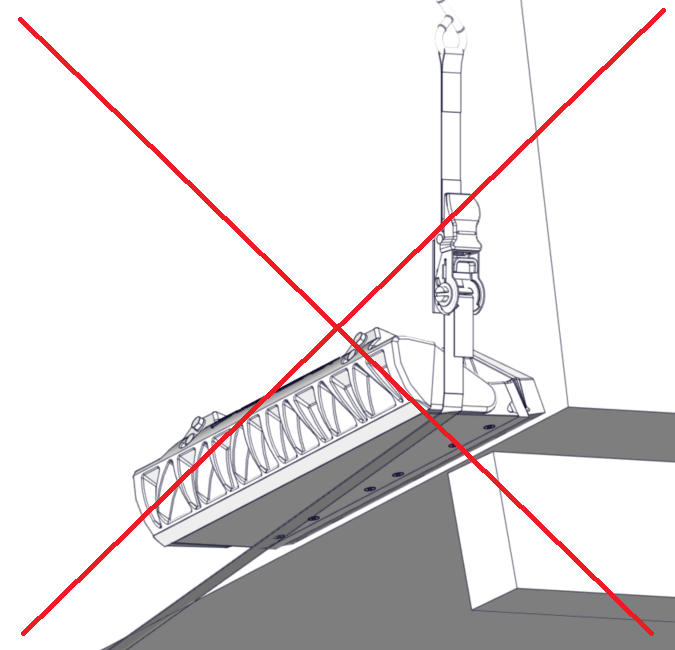
5.6. Asymmetrical Details
Many boats are not perfectly symmetrical about the centerline, resulting in subtly different mounting locations and angles for each Controller. This is acceptable and may require different Wedge angles used for port and starboard Controllers. Following this guideline for the correct installation location will result in a proper installation even if there are asymmetries in the hull.
5.7. Cable Entry
In the final details of the installation, the cable that powers and drives the Controllers must pass through the transom of the hull. The location for cable penetration will be based on available access to the transom on the interior.
Concealed Cable Entry
For concealed cable entry, route through either of the oval holes of the Transom Plate (highlighted in blue in the figure below). To utilize either location, you must be able to reach the hole from the inside to tighten the supplied cable gland and prevent water entering the hull.
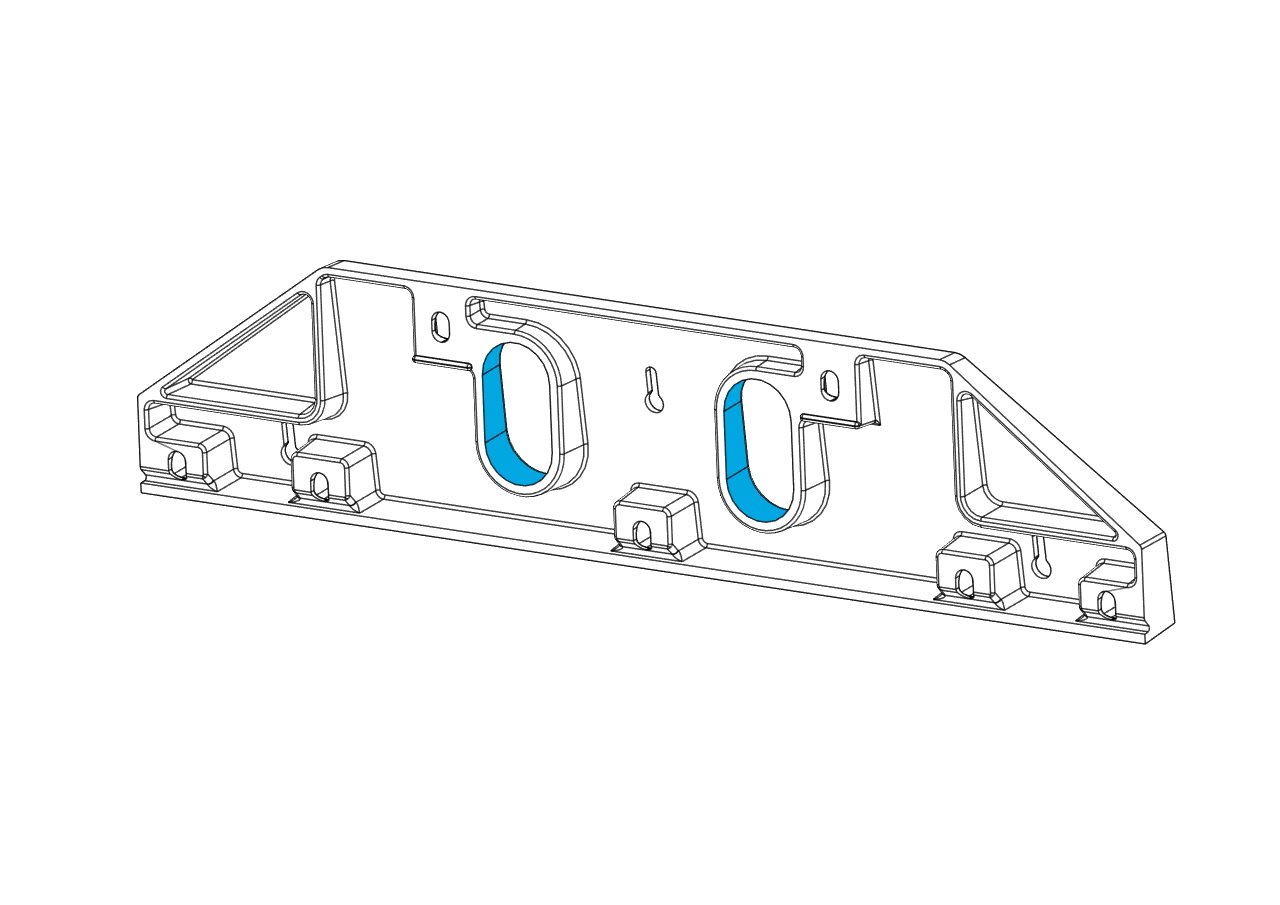
As an example for internal routing, the figure below depicts a stringer shown with dotted lines that is preventing use of the inboard cable penetration. In this example, the outboard cable pass-through is available as indicated by the blue arrow. This can only be used if there is access on the interior side of the penetration.
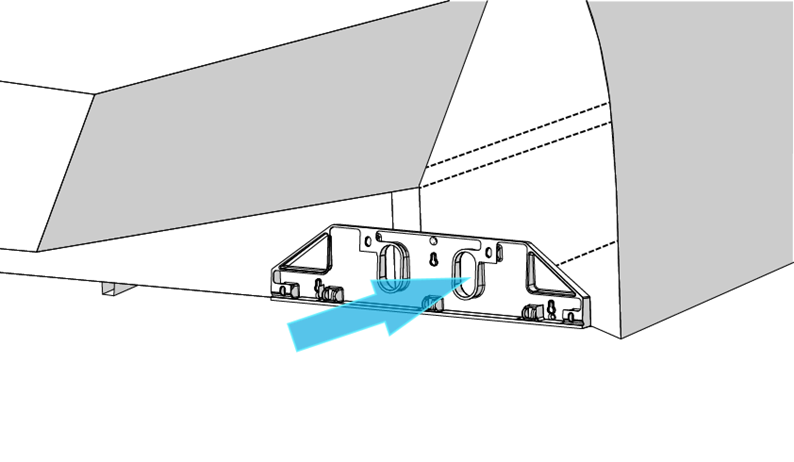
Exposed Cable Entry
Locations outside the Transom Plate can be used as well. If the cable penetration location is below the waterline, the supplied cable gland must be used to ensure a watertight hull after the penetration.
This cable penetration method can be used in locations above the waterline as well.
Cable Lengths
In all cases, the supplied cable for the Controllers is limited to 10 ft (3 m). Carefully consider the cable routing and location of the Distribution Module to ensure both cables can connect to the Distribution Module.