Seakeeper 35 / 30HD Installation Manual (90268-7)
Cooling Installation
Cooling Installation Introduction
The Seakeeper 35 is shipped with the cooling circuit filled and ready for use. Only a quick confirmation of glycol level is required.
Reference Documents & Drawings:
Link to Seakeeper 35/30HD Reference Documents
- 90233 – Seakeeper 35 Hardware Scope of Supply
- 90417 – Seakeeper 30HD Hardware Scope of Supply
- 90288 – Seakeeper 35/30HD Cable Block Diagram
- 90290 – Seakeeper 35/30HD Cooling Water Schematic
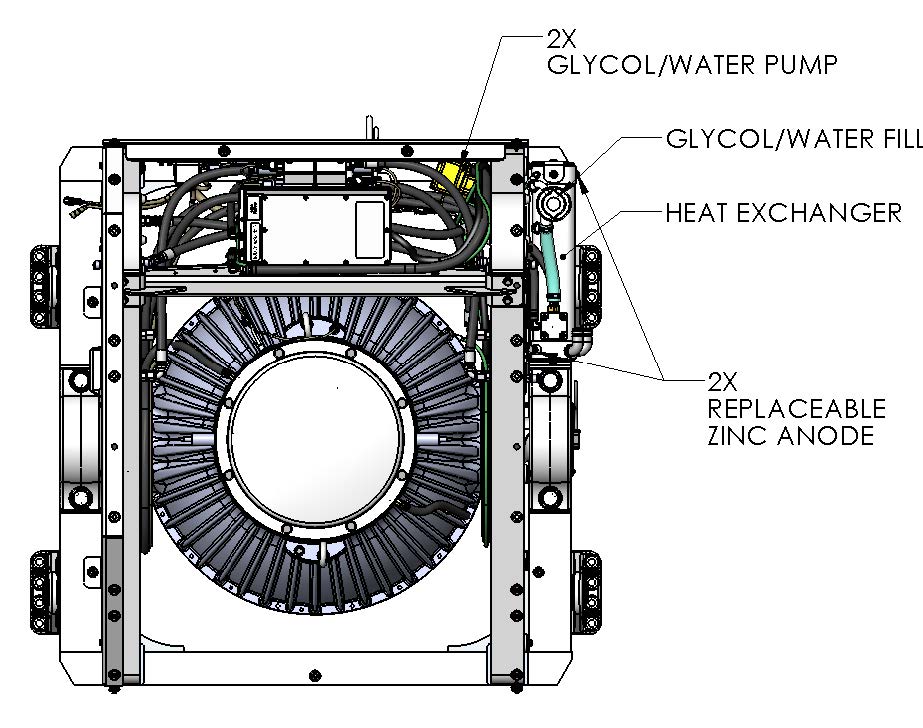
Precautions
- Installer is responsible for supplying a dedicated seawater pump and associated plumbing. Seawater connections on the heat exchanger mate with 1 in. (25.4 mm) hose.
- There is no need to disconnect hose from glycol pump except to replace the pump. In this case, provision will need to be made to catch draining glycol as plumbing is disconnected. Use caution to avoid breaking plastic hose connections on pump casing.
- An output is available from motor drive box to power and automatically control seawater pump. This pump must operate on 230 VAC single phase and consume less than 5 A. Pumps requiring other voltages or higher current can still be controlled by using this supply from motor drive to trigger an installer-supplied contactor, but a separate source of power must be provided.
- Maximum seawater pressure in heat exchanger is 20 psi (1.4 bar).
- Seawater flow requirement through heat exchanger is 10 GPM (38 LPM) minimum and 14 GPM (53 LPM) maximum under all operating conditions of the boat. When sizing seawater pump, installer should factor in losses for raw water plumbing. In addition to initial operation at dock, new Seakeeper installations should be checked to be within the flow requirements while vessel is at speed. Flows higher than 14 GPM (53 LPM) could affect heat exchanger life.
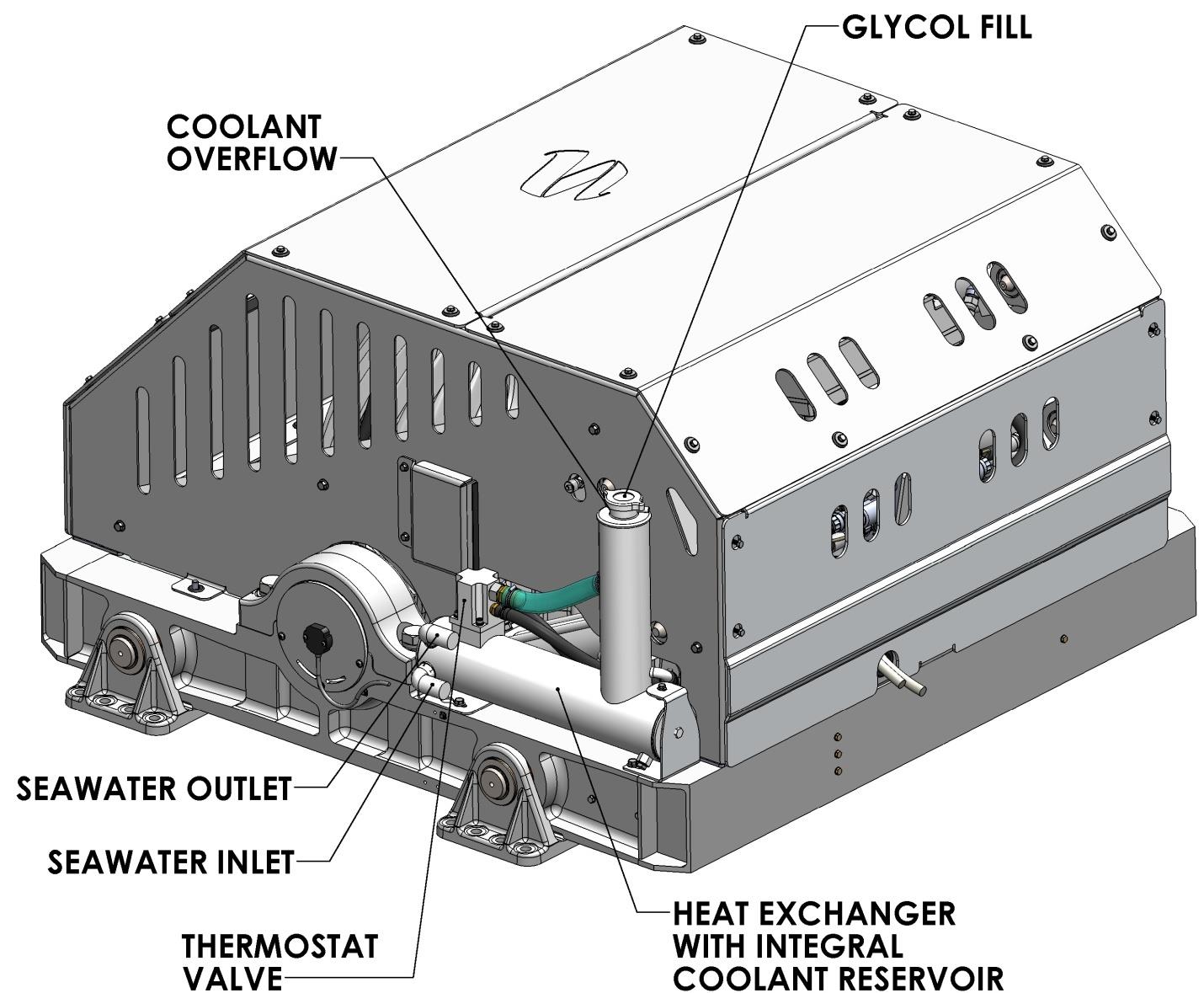
Adding Coolant
- Cooling system is filled to proper level when shipped, with a mixture of 50% ethylene glycol and 50% distilled water. The clear tube between the thermostat housing and reservoir should be filled with green coolant mixture. If level has dropped, check for evidence of leaks at all connections before adding fluid as described below. If coolant is at the correct level, skip to Section: Connecting Seawater to Heat Exchanger.
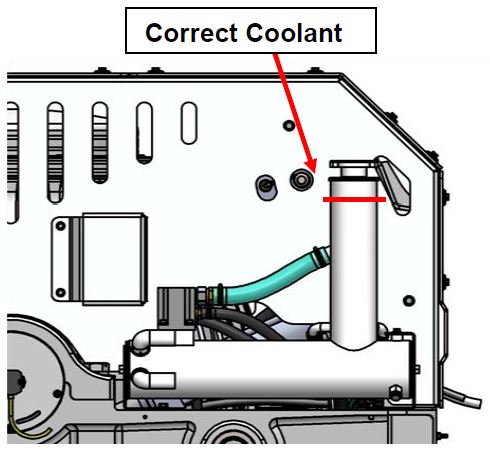
- Mix 50% ethylene glycol with 50% distilled water in a clean container. Refer to Table 1 or glycol manufacturer’s literature for freezing points.
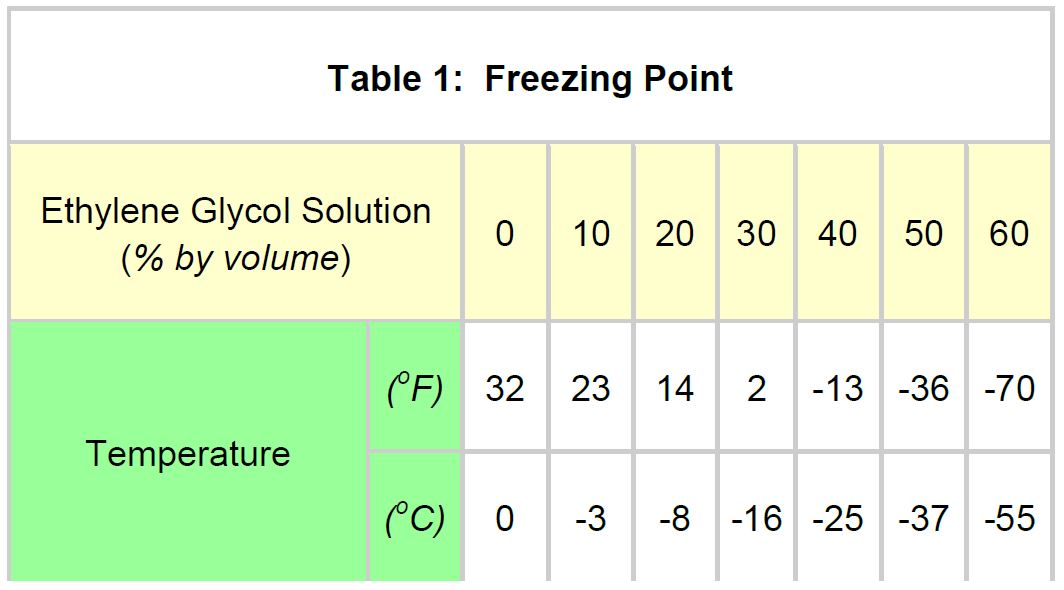
- Remove pressure cap on top of reservoir. Pour mixture in until level is 1 – 2 inches from top of reservoir as shown in Figure 3. Filling reservoir above this level will not cause any damage but coolant may be expelled from pressure relief port below cap due to normal thermal expansion of coolant.
- Connect 24 V to controller.
- At the Display check for any ALARMS
- Press the POWER ON/OFF button.
- The flywheel will start to spin and the glycol pump will start.
- Recheck glycol level with fluid circulating in coolant circuit. Sight down inside reservoir and check that coolant level is above upper port on reservoir as shown in Figure 3. Replace cap.
- After several minutes of running, press POWER ON/OFF button
to turn power off to the flywheel and glycol pump.
- At the Display check for any ALARMS
- The cooling system is self-purging. If small amounts of air are in the system, they will most likely be dislodged during the first sea trial. Re-check level after sea trial and add fluid if required.
Connecting Seawater to Heat Exchanger
- Connect seawater from installer-supplied pump to lower 1 in. (25.4 mm) hose barb on heat exchanger. Use the same practices as other below waterline seawater plumbing. Required flow rate is 10 GPM (38 LPM) minimum and 14 GPM (53 LPM) maximum.
- Connect seawater discharge (upper hose barb) to overboard drain. Use the same practices as typical below waterline seawater plumbing.
- In addition to initial operation at dock, new installations should be checked with a flow meter for minimum 10 GPM (38 LPM) flow under all normal operating conditions. If no other method of confirming flow is available, discharge line may be temporarily diverted to a bucket. Flow is calculated from time to fill a known volume. A self-priming seawater pump (customer/installer supplied) may be required due to installation location to maintain water flow in all underway conditions where cavitation near the intake may occur and potentially cause an air-lock condition restricting seawater flow to the heat exchanger.
- Inspect raw water plumbing after sea trial for any signs of leakage.
- Heat exchanger contains removable end-caps to provide access for cleaning the tube bundle.
