Seakeeper 26 Installation Manual (90265-8); S/N 26-233-0690 to Current
2.5 Saddle Installation
2.5.1 Saddle Installation Introduction
Seakeeper recommended adhesives are listed in TB-90382 – Structural Adhesives Recommendations. Seakeeper recommends using a structural adhesive with a lap shear strength of 2000 psi (13.8 MPa) or greater. Careful consideration should be exercised by the installer when selecting the appropriate adhesive, such as working time, material compatibility, and surface preparation are three important factors to consider. Proper surface preparation in accordance with the adhesive manufacturer’s recommendations prior to installation is critically important. Information regarding pot-life, structural properties and material compatibility can be found on the adhesive product’s technical data sheet (TDS). An etching/cleaning primer compatible with the adhesive should be used on all aluminum surfaces if recommended by the manufacturer. Typically, two-part methacrylate based adhesives are the best options for bond-in installations such as Plexus MA590 and Sci-GripSG300, which provide compatibility with aluminum and FRP substrates, adequate working time, and exceed the strength requirements. See Seakeeper Drawing No. 90272 – Seakeeper 26 Bond-In Installation Details, for further information.
2.5.2 Preparation of Vessel Structure
Refer to Seakeeper Drawing No. 90272 – Seakeeper 26 Bond-In Installation Details. Important dimensional and load information is given in this drawing that will impact the design details of the structure that will receive the Seakeeper as well as selection of the adhesive to bond the Seakeeper into the hull.
The foundation “saddles” of the Seakeeper are designed to be bonded directly to the composite hull structure of the vessel to effectively distribute Seakeeper loads. A complete bond is required between the inside surface of the saddles and the hull structure. Seakeeper recommends having a minimum of 2.4 L / 0.6 gal of adhesive on hand for installation. Some adhesives require etching primer for aluminum surfaces (Plexus MA590 requires PC120 primer). Both manual and pneumatic application guns are available from adhesive manufacturers. Two workers should apply the adhesive at the same time to finish the installation before the adhesive starts to cure. To aid in determining the quantity of adhesive required, the interior surface area (bonding surfaces) of each saddle is 287 in.2 (1,852 cm2) for a total bonded surface area for all four saddles of 1,148 in.2 (7,406 cm2).
The hull structure supporting the Seakeeper should be arranged so the Seakeeper is parallel to the water plane in the port-starboard and forward-aft directions. In addition, the four areas on top of the beams that the saddles will bond to need to be co-planar within 1/8 in. (3 mm) to minimize potential distortion of Seakeeper support frame when installed. The four areas on top of the saddles on which the feet of the Seakeeper foundation rest must be coplanar within 0.6 in. (1.5 mm) to minimize potential distortion of Seakeeper support frame when installed.
Note that any paint or gel-coat present in bond area should be removed so that adhesive will bond directly to laminate fibers and resin. Fiberglass and aluminum surfaces should be sanded in cross-hatch pattern with 80-grit sandpaper and thoroughly cleaned prior to adhesive application.
Seakeeper provides an installation fixture template (P/N 90088), that locates the saddles at the proper spacing both in the port-starboard and the forward-aft direction direction. See Figures 6, 7 & 8 below. Once assembled with the provided saddle fittings, the fixture can be used to check clearances and alignment of the hull structure. The fixture will allow the builder / installer to lay-up and adjust the foundation dimensions to create a low-clearance fit between the Seakeeper foundation saddles and the hull structure. Shear strength of the adhesive will be maximized if the cured thickness between the vessel structure and the Seakeeper saddles is at the thinner end of the adhesive manufacturer’s recommended range. Therefore, the fixture should be used to confirm that the overall dimensions of the foundations are square and level and that the adhesive gap is within Seakeeper’s recommended range of .04 in. to .13 in. (1 to 3 mm).
Note: Do NOT use the installation fixture to establish Seakeeper envelope dimensions. Refer to Drawing No. 90272 – Seakeeper 26 Bond-In Installation Details, for envelope dimensions. A 3-D model of the Seakeeper is available on the Seakeeper website (www.seakeeper.com) to aid in designing the Seakeeper foundation and the space around the Seakeeper.

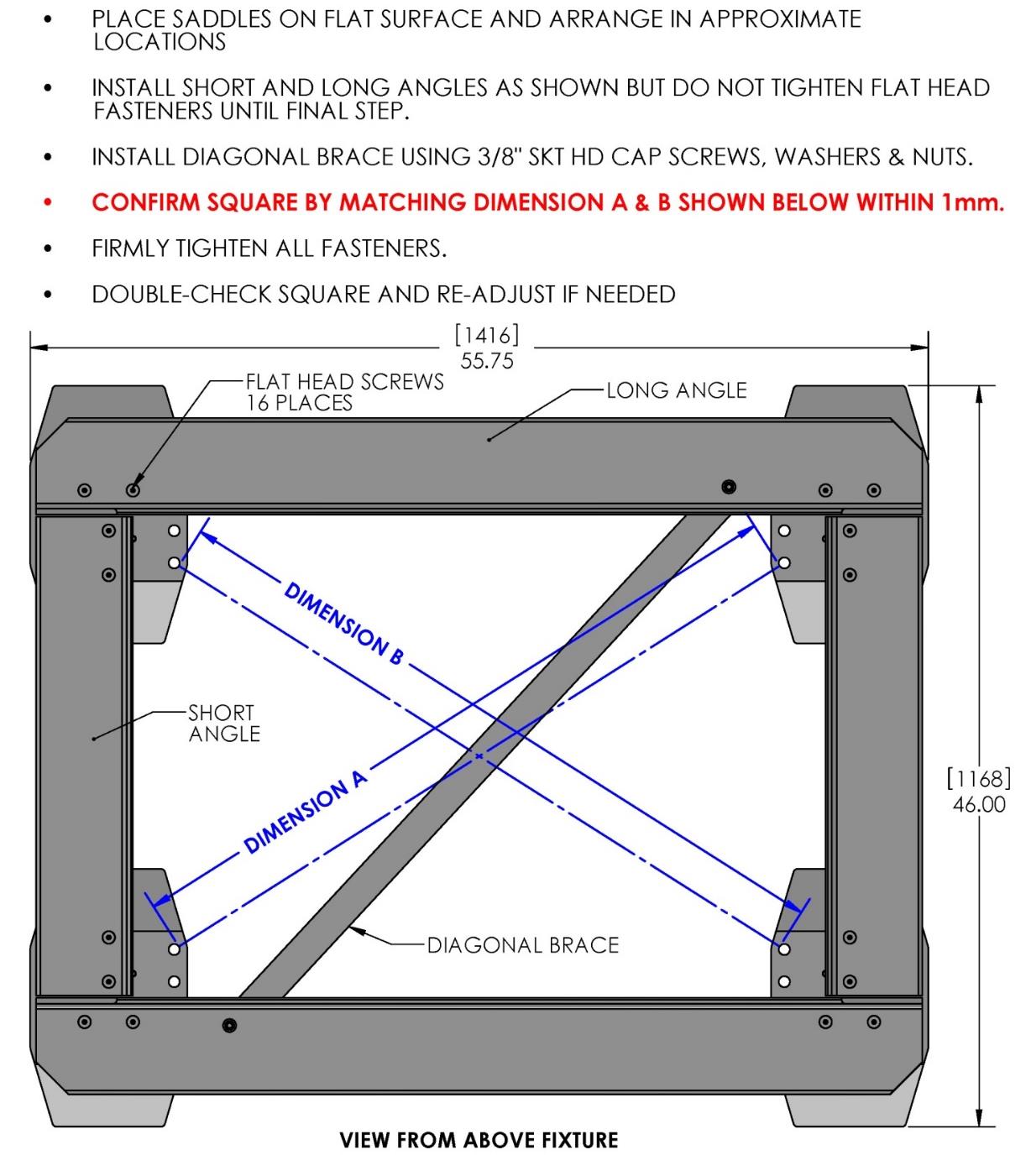
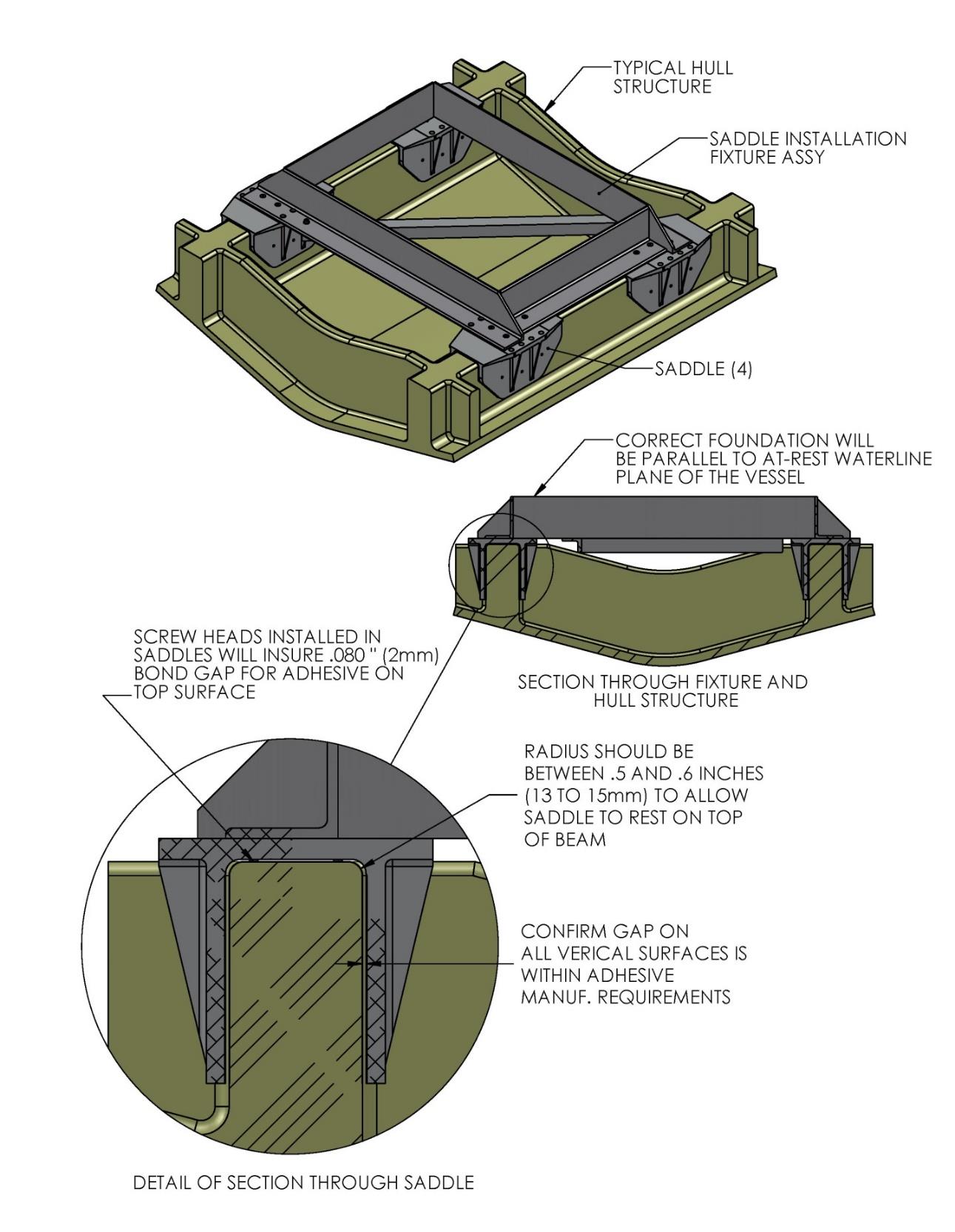
2.5.3 Fiberglass Hull Preparation
- Position installation fixture (Figure 9) on hull girders noting recommended clearances for maintenance from Figure 2 (in Section: Selection of Installation Location). Check that the screws fastening the saddles to the installation fixture are tight (Figure 7).
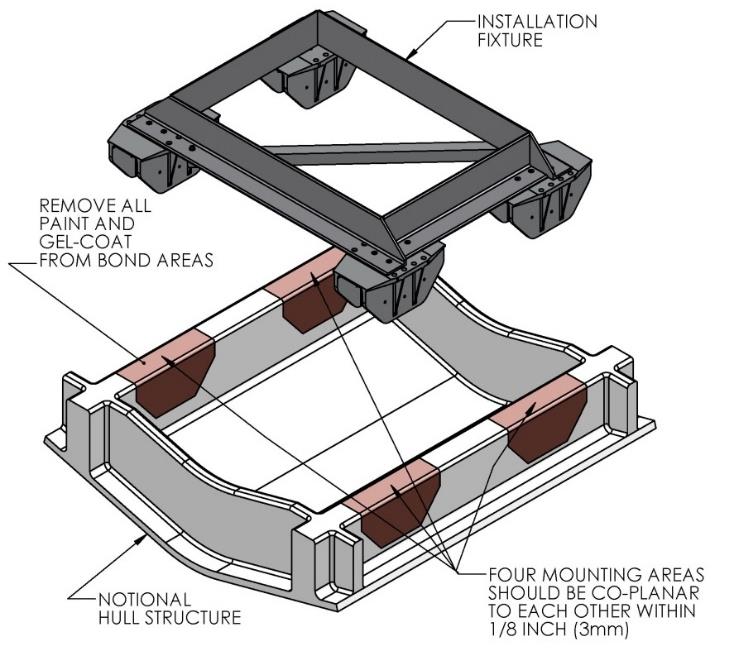
- Mask hull area (as shown in blue, Figure 10) around foundation saddles for easy clean-up and to create an outline of surface area to receive adhesive as shown in brown (Figure 9). Ensure that the bond gap is within adhesive manufacturer’s recommended thickness, or 3 mm if using Plexus MA590 or Sci-Grip SG300.
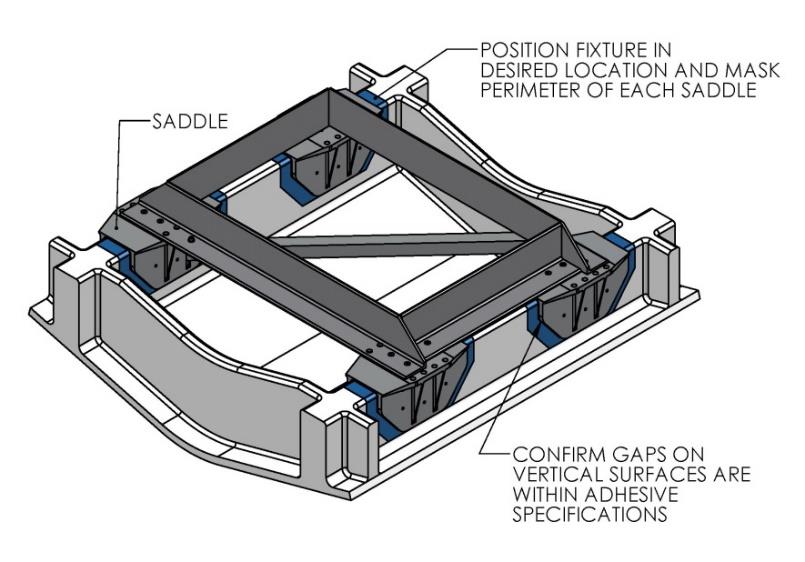
- Raise fixture clear of foundation. Check all four mounting areas are co-planar to within 1/8 in. (3 mm) to each other, as well as parallel to the water line plane, as shown in Figure 11.
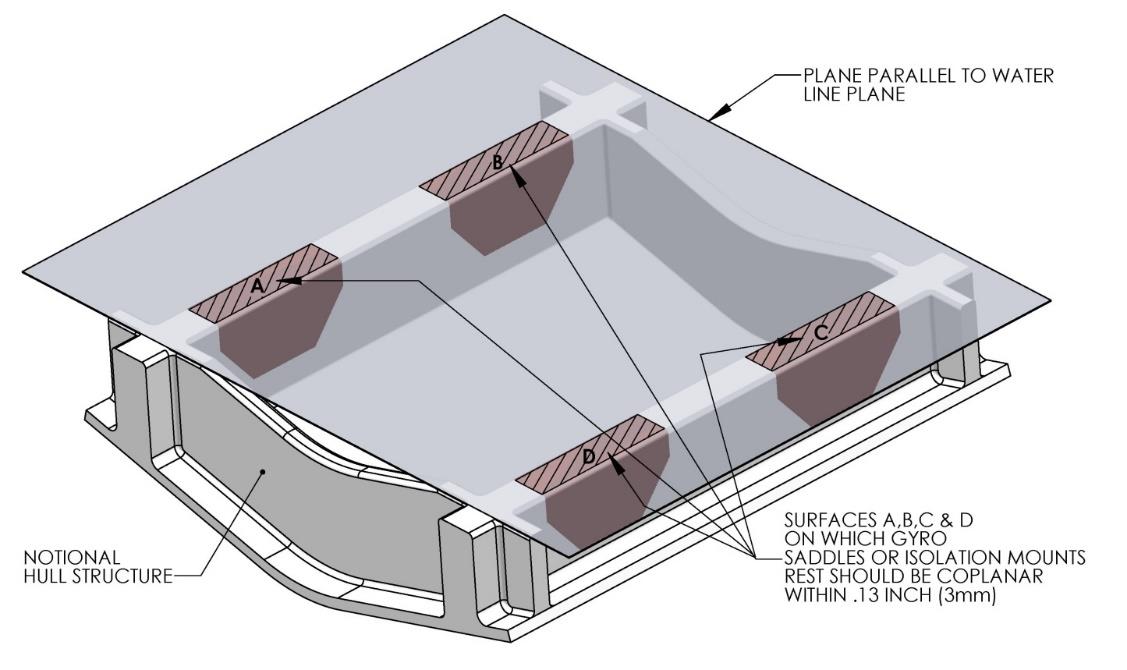
- Thoroughly clean with alcohol or acetone all areas (highlighted in brown, Figure 9) of girders to be bonded to remove any contaminates. Use new paper towels for cleaning, not shop rags.
- Remove any paint or gel-coat from bond surfaces so that adhesive will bond directly to laminate fibers and resin.
- Thoroughly sand girder bond surfaces with 80 grit sandpaper in cross-hatch pattern. (IMPORTANT – BOND STRENGTH MAY BE REDUCED IF THIS STEP IS SKIPPED.)
- Wipe surfaces clean from dust with alcohol or acetone using new paper towels, not shop rags.
- Re-position installation fixture on girders and double-check that the adhesive gap is within the adhesive manufacturer’s maximum recommended thickness. (Note gap will be larger due to absence of gel-coat.) Seakeeper recommends a maximum gap of 3 mm if using Plexus MA590 or Sci-Grip SG300.
- Lift installation fixture clear of foundation. Apply Seakeeper provided adhesive backed foam strips at the eight locations shown (each end of four saddles) in Figure 12 below. These strips are to serve as a dam to minimize adhesive escaping out the ends of the saddles as they are positioned over the bond area.
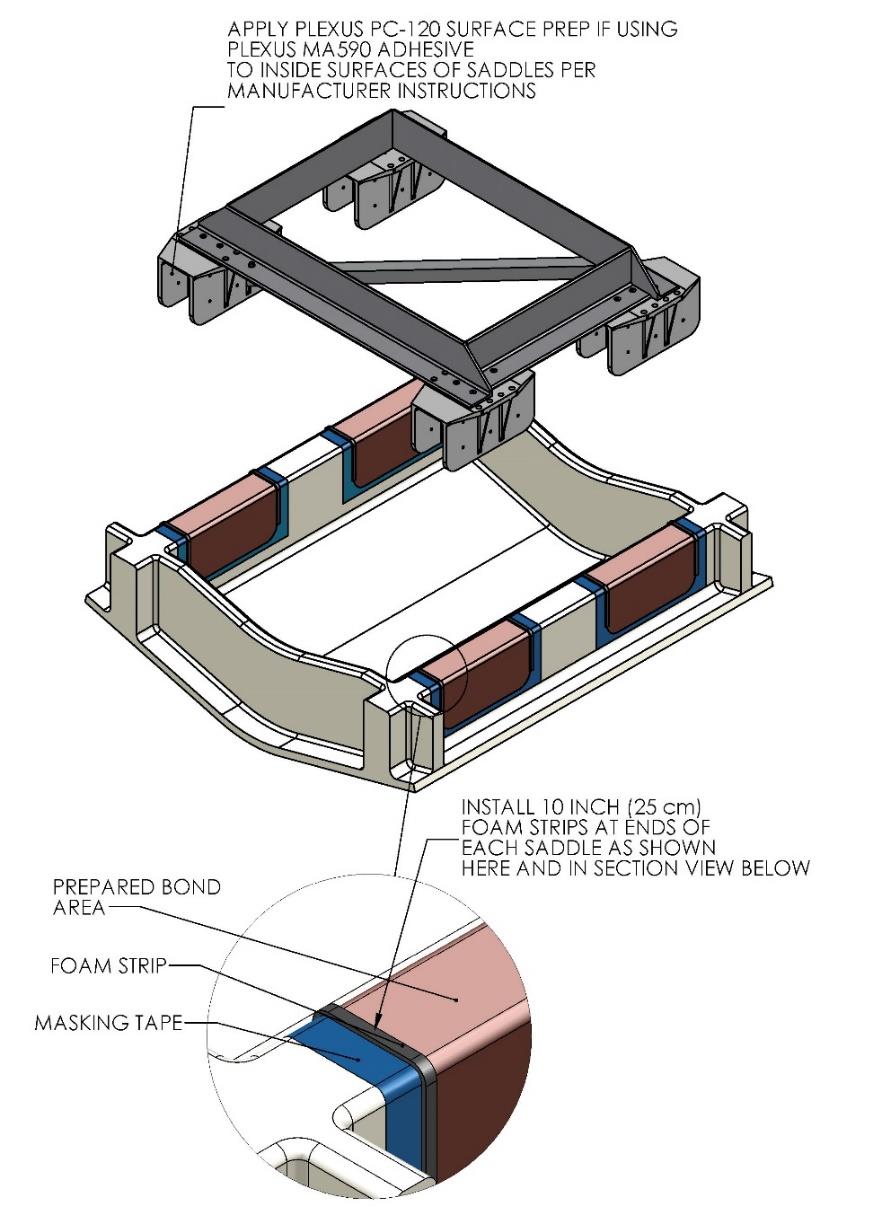
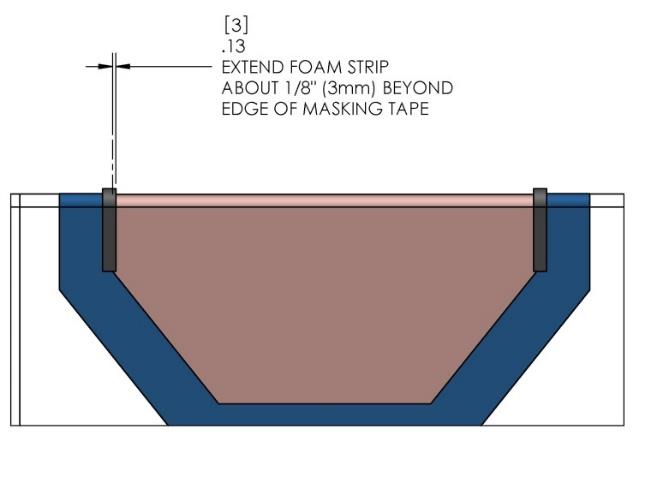
Note: If bonding saddles to a non-composite hull, contact Seakeeper for hull preparation instructions.
2.5.4 Seakeeper Saddle Preparation
- Ensure that screws fastening saddles to the installation fixture are tight (Figure 7).
- Check that each saddle contains 4 plastic screws which will ensure an adhesive gap of .080 in. (2 mm) on top surface of hull as shown in Figure 13. Do not remove these screws.
- Thoroughly clean with alcohol or acetone the inside surfaces of Seakeeper foundation saddles to remove any contaminates as shown in Figure 13. Use new paper towels for cleaning, not shop rags.
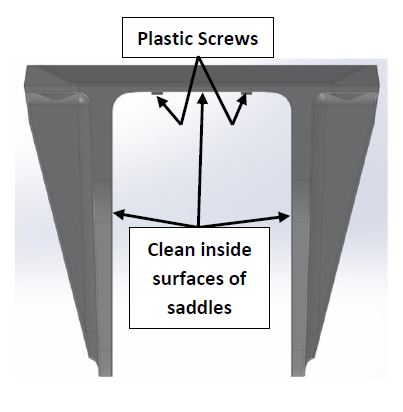
- Thoroughly sand all saddle inside surfaces with 80 grit sandpaper in a cross-hatch pattern. (IMPORTANT – BOND STRENGTH MAY BE REDUCED IF THIS STEP IS SKIPPED.)
- Wipe surfaces clean from dust with alcohol or acetone using new paper towels, not shop rags.
- If using Plexus MA590 adhesive, apply Plexus PC-120 surface conditioner to inside surfaces of Seakeeper foundation saddles in accordance with manufacturer instructions. These instructions are located at the end of this section. If using an alternate adhesive, check with manufacturer if any surface conditioner/etch is required for the aluminum saddles.
2.5.5 Bonding Saddles to Hull
Note: This is a sample if using Plexus, if using another adhesive follow manufacturer’s recommendations.
If using Plexus MA590 adhesive, the Seakeeper saddles should be installed when PC-120 is confirmed dry.
- Assemble Plexus cartridge into either the manual or pneumatic gun as shown. Remove cap on cartridge and attach mixing tip. For pneumatic gun, start with low air pressure and increase until desired flow rate is achieved.
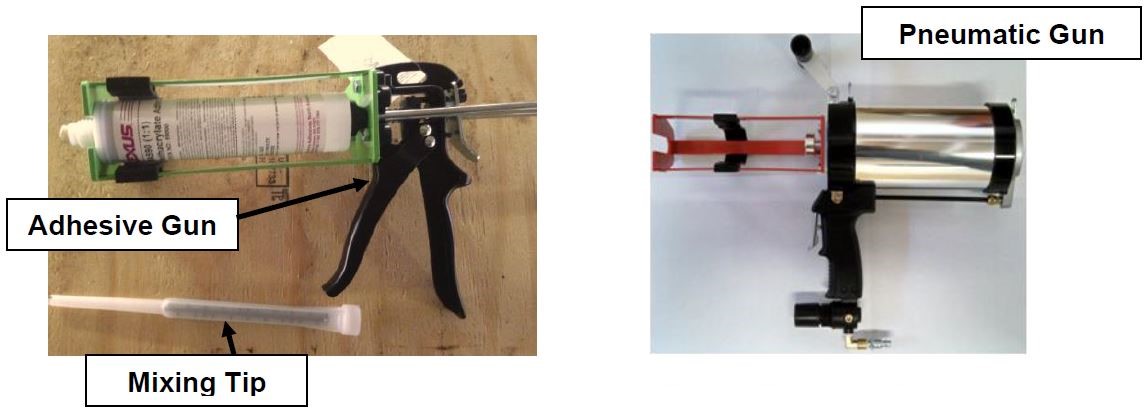
- Cut tip of mixing wand as shown in photo below.
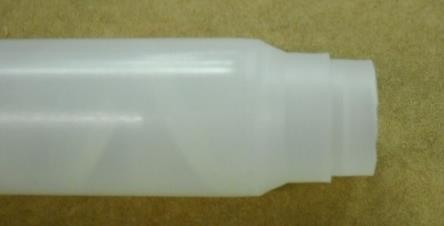
- Prepare a second mixing wand as shown in photo below by attaching the simple flexible nozzle to the end of the mixing tip. Set aside for now as this will be used to inject adhesive into the sides of each saddle after the fixture / saddles are in position.
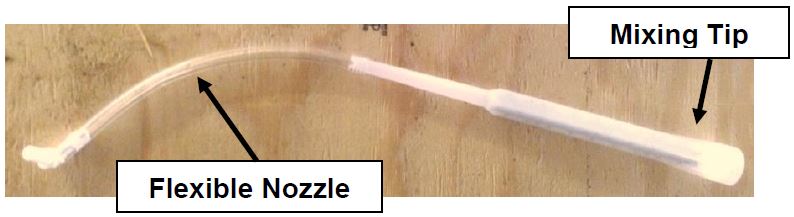
- Install provided rubber plugs in 12 holes of each saddle. The plugs will limit the adhesive being forced out of the injection holes in step 6 below.
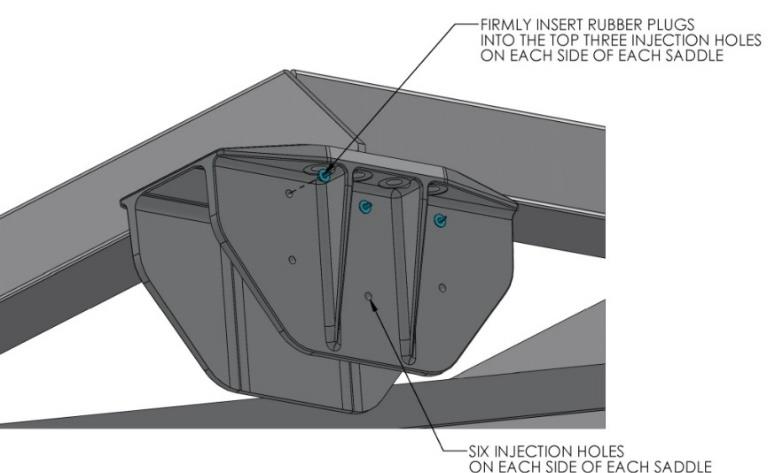
- Apply large bead of Plexus adhesive to the hull structure as shown in the figure below. Apply approximately 350 mL at each of the four locations (the adhesive should completely fill the gap between the hull structure and Seakeeper saddles, and generate squeeze out along the sides when the saddles are placed onto the structure). Work deliberate and fast as it takes some time to apply the adhesive to the structure. MA590 has a 90-minute working time at room temperature (73°F / 23°C). This working time can reduce to 40-50 minutes at elevated temperatures. Two workers should apply the adhesive at the same time to finish the installation before the adhesive starts to cure.

- Lower fixture and saddles over the hull structure and apply light downward pressure to each of the four saddles until the four nylon screws rest on the hull structure (see Figure 9). The adhesive will be forced towards the forward and aft ends of each saddle and partially down the sides of the foundation beams.
- Insert full adhesive cartridge along with mixing wand / nozzle assembled in Step 3 above, into gun.
- Begin to inject adhesive into the six holes provided on each side of each of the four saddles. Follow the numbered sequence shown until the adhesive pushes out the edges of the saddle perimeter. The intent is to pump in the adhesive working from the top down and from the middle to the ends to fill the gaps and displace any air. A complete bond is required – excess adhesive will be needed to make sure all bond gaps are filled.
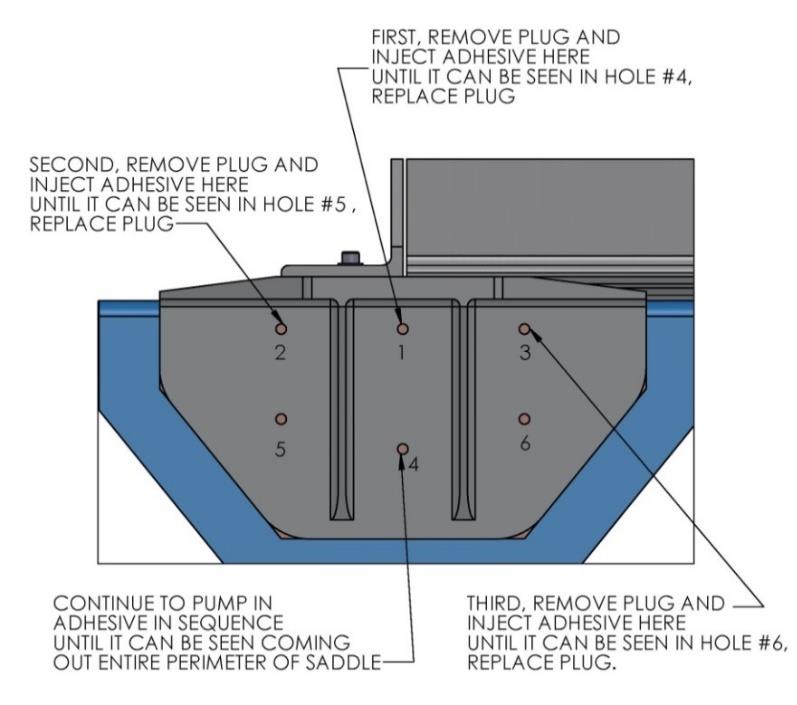
- Repeat above step for remaining 7 sides of the saddles.
- When gaps have been completely filled, clean off excess adhesive, remove foam tape, remove plugs, and remove masking tape.
- Allow adhesive to cure per manufacturer’s recommendations. Follow adhesive guidelines for curing time versus temperature prior to removing the fixture.
- Bonding of Seakeeper saddles onto the hull is now complete. Remove installation fixture.
2.5.6 Installation of Seakeeper
- Rig Seakeeper for lifting and lower it into position onto top surface of four saddles.
- Adjust position of the Seakeeper until alignment is achieved for the 32 fasteners that will attach the Seakeeper foundation frame to saddles.
- Install Seakeeper supplied M16 fasteners as shown in figure below – apply a moderate coat of nickel based anti-seize compound to the threads of each bolt prior to installation.
- Torque all fasteners to 100 ft-lbs (136 N-m).
- Apply a small bead of sealant (silicone or caulk) around the perimeter of each isolation mount where it rests on the saddle. This will prevent water from wicking between the parts and setting up corrosion.
- Proceed to electrical and cooling portion of the installation.
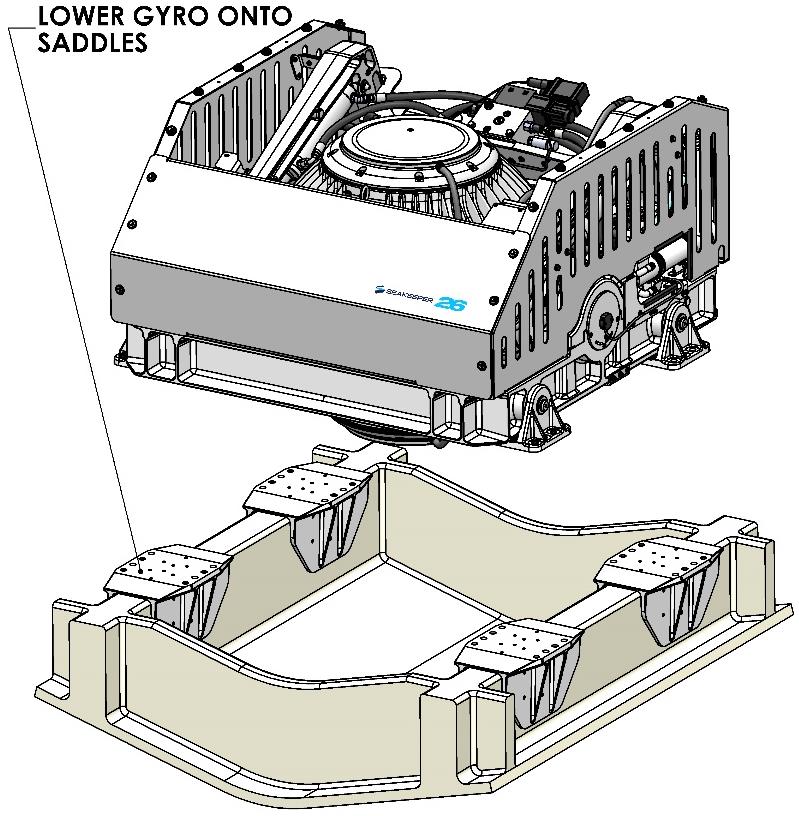
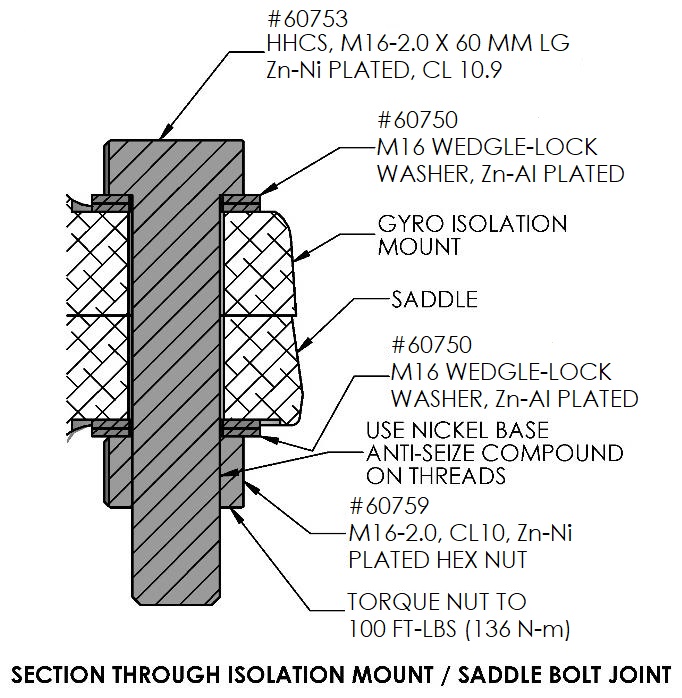
3.0 Electrical Installation
3.1 Electrical Introduction
This section for electrical installation explains how to mount the electrical equipment and how to connect the electrical cables.
Reference Documents & Drawings:
- 90310 – Seakeeper 26 Cable Block Diagram (includes 2nd Display Kit)
- 90438 – 5″ Operator Display Envelope and Mounting Details
- 90467 – Seakeeper 5″ Display Kit
- 90266 – Seakeeper 26 Operation Manual
- Seakeeper Compatibility Technical Bulletins
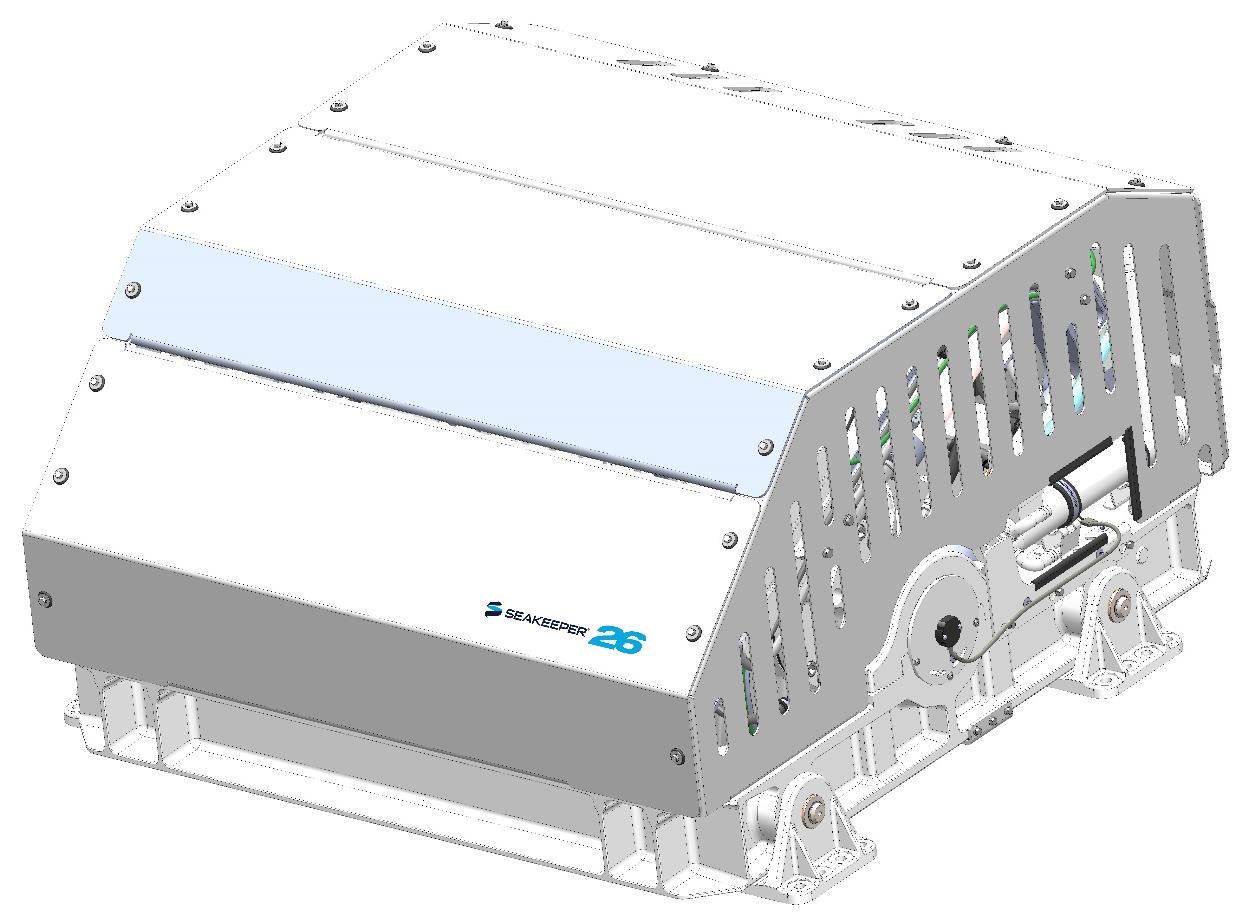
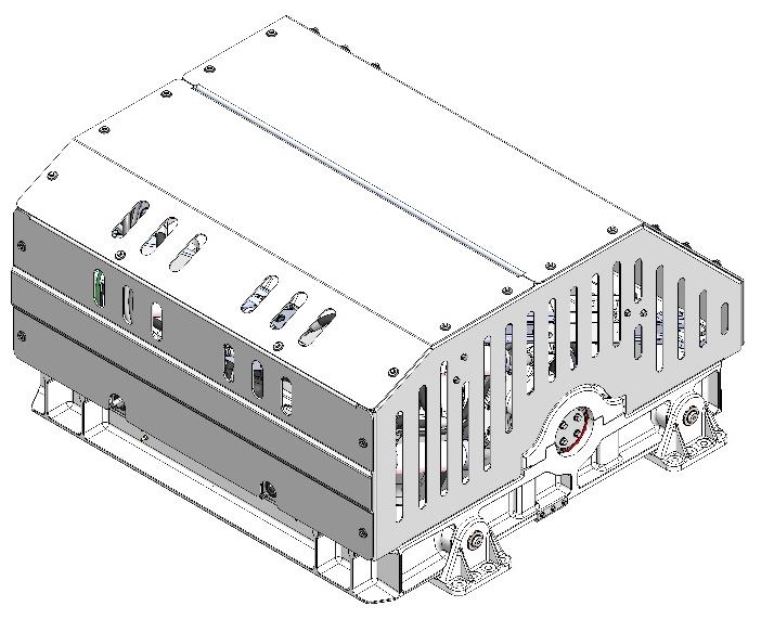
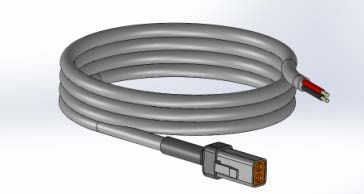
Cable 1 – P/N 20248
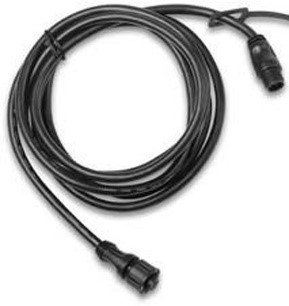
19 ft (6 m)
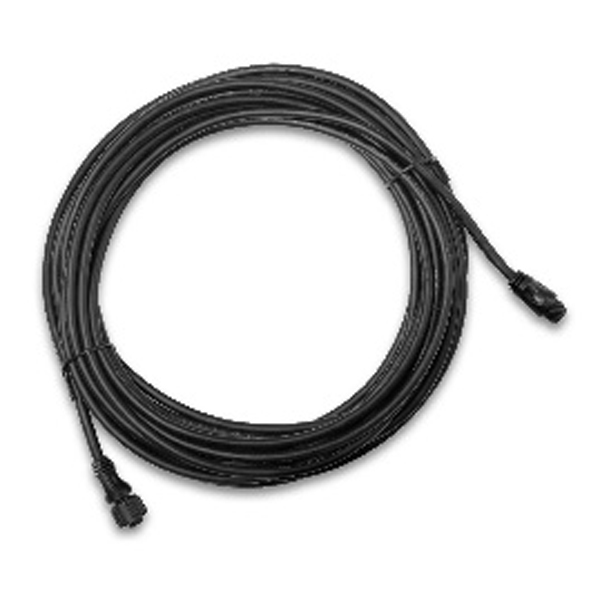
Figure 1 – Electrical Equipment for Seakeeper 26
3.2 Electrical Equipment Power Connections
230 VAC Power Source Requirements
- 230 VAC (nominal), 1 Phase, 50/60 Hz, 30 A
- For installations of more than one Seakeeper, a separate circuit breaker must be used for each Seakeeper Motor Drive Box.
Drive Box AC Power Input Connection Instructions
- Cable: 3 x 10 AWG (3 x 6 mm2 CSA), 10 ft (3 m) length, Seakeeper supplied pre-installed.
- Locate AC Power Input Cable to the Motor Drive Box.
Figure 2 – Motor Drive Box AC Power Input & Output Cable Glands
Figure 3 – AC Power Input Cable Wire Connections at AC Power Distribution Panel - Connect 230 VAC wires in AC Power Input Cable to a 30 A, double-pole Circuit Breaker at an AC power distribution panel according to Figure 3 above.
- Locate AC Power Input Cable to the Motor Drive Box.
Drive Box AC Power Output to Seawater Pump Connection Instructions
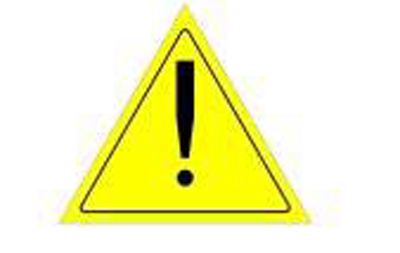
Verify that AC power is OFF to the Drive Box before connecting Seawater Power Cable to a Seawater Pump.
- Cable: 3 x 14 AWG (3 x 2 mm2 CSA), 10 ft (3 m) length, Seakeeper supplied pre-installed.
- Pumps rated at 230 VAC, 5 A max., Customer-supplied.
- Locate AC Power Output Cable to the Seawater Pump from the Drive Box at the middle of three cable glands. (See Figure 2 above).
Figure 4 – AC Seawater Output Power Cable - Connect the 230 VAC wires in AC Seawater Power Cable to a 5 A (maximum), Seawater Pump (approximately 1/3 horsepower or 250 W) according to Figures 4 and 5.
Figure 5 – Seawater Pump Power Cable Wire Connections to Seawater Pump
- Locate AC Power Output Cable to the Seawater Pump from the Drive Box at the middle of three cable glands. (See Figure 2 above).
- If the customer-supplied Seawater Pump is not rated for 230 VAC, the Seawater Pump Power Cable output may be used to switch a customer-supplied relay.
- Locate AC power output to the Seawater Pump from the Drive Box at the middle of three cable glands as shown in Figure 2.
- The recommended wiring is shown in Figure 6. Refer to Figure 4 for Seawater Pump Cable wire connections.
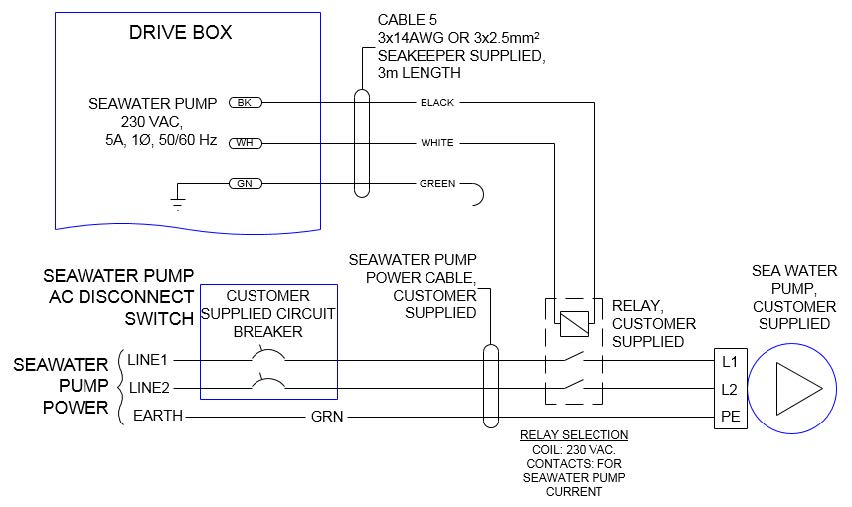
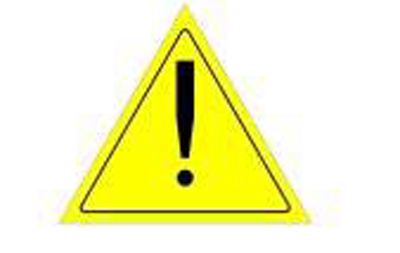
Seawater Power Cable contains live voltage when Seakeeper is in operation. Do NOT cut Seawater Power Cable. Do not remove Seawater Power Cable from Drive Box.
- If Seawater Power Cable is not used, bundle cable and secure to forward brace or other area nearby which will not come in contact with moving parts during Seakeeper operation. Do NOT cut Seawater Power Cable as it contains live voltage when Seakeeper is in operation. Seakeeper ships with Seawater Power Cable permanently sealed at end of cable with protective cap in the event it is not used. Do NOT remove Seawater Power Cable from Drive Box as moisture will be free to enter box through open cable gland and corrode internal electronic components
24 VDC Power Source Requirements
- 24 VDC, 15 A
- A separate breaker should be used for each Seakeeper control power input.
DC Power Connection Instructions
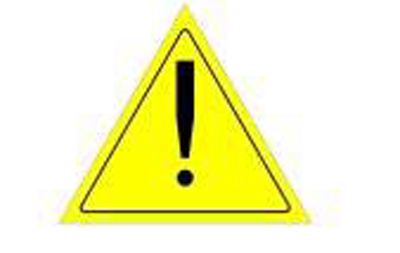
Reversing polarity on the DC power input to the Seakeeper can result in damaging the electronics in the control system.
________________________________________________________
When energizing DC power for the first time, if Display does not power up immediately then disconnect and inspect connector polarity.
- 24 VDC, 15 A, 2 x 12 AWG (3 x 4 mm2 CSA) customer supplied.
- Install Seakeeper provided DC Power Input Cable, P/N 20248.
- Route DC Power Cable to DC Power Distribution Panel.
- Terminate positive (B+, Red) conductor through dedicated over-current protection device (customer supplied) and to +24 VDC.
- Terminate negative (B-, Black) conductor to battery negative terminal or negative bus.
- Before connecting DC Power Cable to Seakeeper, check for proper voltage and polarity with a DC multimeter using Figure 7 below.
- Connect DC Power Cable to 24 VDC input receptacle on Seakeeper.
- Install Seakeeper provided DC Power Input Cable, P/N 20248.
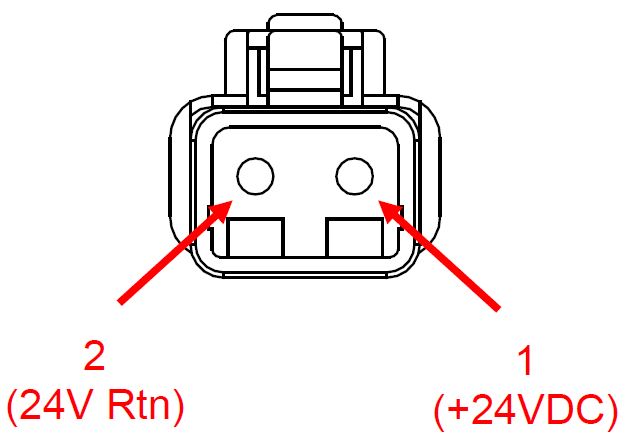
3.3 Electrical Equipment Ground Connections
- Connect the Seakeeper foundation to vessel ground.
- Install properly-sized ring terminals on 10 AWG (or 6 mm2) Ground Cable. Seakeeper connection requires ring terminal for M6 screw.
- Install Ground Cable (10 AWG or 6 mm2, Customer supplied) from the M6 brass ground stud at the rear of the Seakeeper frame to a suitable vessel ground.
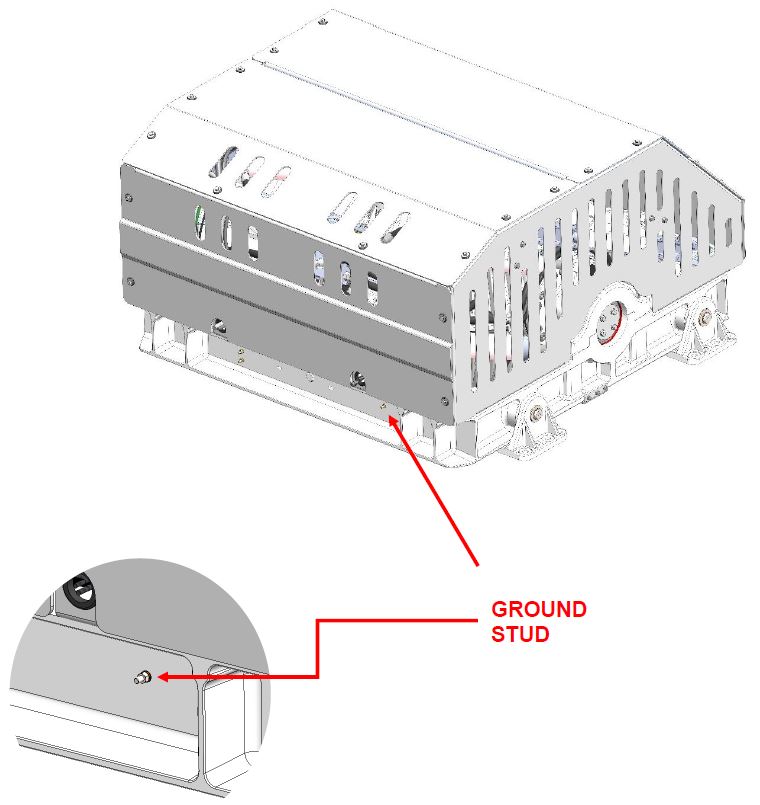
- Connect 10 AWG (6 mm2) conductor with ring terminal to vessel grounding bus to comply with:
- EN/IEC 60204-1 CLAUSE 6.3.3
- ABYC E-11.5.4.
3.4 ConnectBox Display Connections
Seakeeper 26 Display Options
A display is required with the installation of a Seakeeper 26 to support the full functionality of the unit through the Seakeeper App in addition to the ConnectBox. The Seakeeper App provides an interface for controlling the Seakeeper or viewing the Settings, Service, Info, and Alarm pages. The Seakeeper ConnectBox can be helm-mounted to provide an additional interface for the control of the Seakeeper but does not replace the need for a Seakeeper compatible display.
The Seakeeper 26 has several options for establishing a Seakeeper display interface to support the Seakeeper App:
- Preferably, connect the Seakeeper to a compatible Multifunction Display (MFD).
- Install an optional Seakeeper 5″ Touch Display (P/N 90467).
- A combination of a compatible MFD and an optional 5″ Touch Display is also available.
The following figure provides a schematic of the preferred display option. The subsequent sections outline the instructions and references for connecting the Seakeeper 26 in each of these display options.
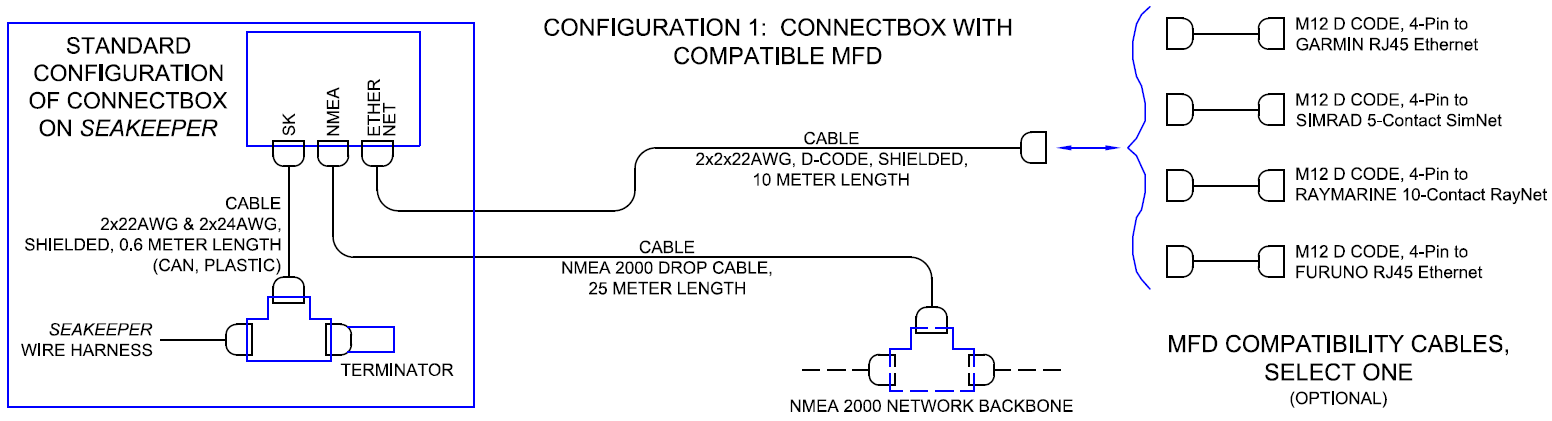
Connecting to a Compatible MFD
- The Seakeeper 26 can be connected to a variety of available MFD systems. Refer to the Technical Bulletins Section of the Seakeeper Technical Library for manufacturer specific MFD compatibility technical bulletins.
- MFD specific Technical Bulletins will be updated regularly as new MFD systems become compatible. Currently GARMIN, RAYMARINE, NAVICO (Simrad, Lowrance, B&G), and FURUNO offer compatible MFD models.
- Once a compatible MFD has been selected, refer to the appropriate manufacturer specific compatibility Technical Bulletin listed above for integration instructions.
- Connect Seakeeper-supplied M12 D-Code, 82 ft (25 m), cable (P/N 30355) to MFD manufacturer-specific Ethernet adapter cable. Custom Ethernet cables for specific MFD manufacturers are available through Seakeeper and must be purchased with the Seakeeper 26 when connecting to an MFD.
Connecting to an Optional 5″ Touch Display
- If not utilizing a compatible MFD display, a Seakeeper 5” Touch Display must be purchased from Seakeeper. The Seakeeper 5” Touch Display (P/N 90467) includes the components shown in the following figure and will be integrated with the ConnectBox.
- Determine location of Seakeeper 5” Touch Display:
- The desired location of the 5” Touch Display must be determined with respect to the vessel’s arrangement.
- The 5” Touch Display should be located on or near the helm or another easily accessible location.
- Route CAN communications cable:
- The CAN Cable, (labelled NMEA 2000 Cable in figure above), is a 32 ft (10 m) shielded cable that connects the ConnectBox Tee adapter to the 5” Touch Display.
- NOTE: Cable lengths are also available in 25, 35, 50, and 65 meters
- The NMEA 2000 cable must be routed and installed in the vessel from the Seakeeper 26 wire harness CAN Tee to the Tee Adapter at the Seakeeper 5” Touch Display, included with P/N 90467.
- The CAN Cable, (labelled NMEA 2000 Cable in figure above), is a 32 ft (10 m) shielded cable that connects the ConnectBox Tee adapter to the 5” Touch Display.
- Install Seakeeper 5″ Touch Display equipment:
- Console space required: Approx. 5.24 W x 3.70 H in. (133 x 94 mm)
- Mounting Instructions, Surface Mount: see Envelope and Mounting Details, in Drawing No. 90438 – 5” Display Envelope and Mounting Details.
- CAN communications tee adapter and terminator mounting instructions:
- Console space required, Rear: Approx. 4 W x 3 H in. (102 x 76 mm)
- Mounting Instructions: Rear mount on vessel console panel, within 2 ft (0.6 m) of Display.
- Hardware required: One mounting screw for 0.197 in. (5 mm) diameter mounting hole on Tee Adapter.
- Connect Seakeeper 5” Touch Display Equipment:
- The Seakeeper 5” Touch Display is connected in accordance with figure below.
- The USB Extension Cable is 6.5 ft (2 m) long cable that enables software updating on a 5″ Touch Display where accessibility to rear panel is limited.
NMEA 2000 Network Connection
The Seakeeper 26 requires a connection to the vessel’s NMEA 2000 network backbone via a drop cable for access to the GPS signal. The Seakeeper 26 will monitor information on the NMEA network to support and optimize the performance of the Seakeeper 26. If no GPS signal is detected, a warning will appear on the Seakeeper display. The Seakeeper will not spool-down, but the operation of the unit will be limited until the GPS signal returns.
- Install customer-supplied NMEA 2000 Tee Adapter (space required: approximately 4 W X 3 H in. (102 X 76 mm).
- Connect NMEA Backbone to Tee Adapter.
NOTE: NMEA drop cable can be no longer than 19.6 ft (6 m) in length. - Connect Seakeeper-supplied NMEA cable (P/N: 30332) to the customer-supplied NMEA 2000 Tee Adapter on vessel’s NMEA 2000 backbone.
- An active NMEA 2000 compatible GPS signal is required on the vessel’s NMEA 2000 backbone to operate the Seakeeper 26.
- If no GPS signal is detected, a Speed Over Ground (SOG signal) warning will be present on the Seakeeper app. See TB-90640 for NMEA connectivity guidance.
- An active NMEA 2000 compatible GPS signal is required on the vessel’s NMEA 2000 backbone to operate the Seakeeper 26.
ConnectBox Helm Mounting – Optional
- Console space required: Approx. 3.41 L x 4.15 W in. (87 x 106 mm).
- Mounting Instructions, Surface Mount: See Drawing No. 90558 – Seakeeper ConnectBox Helm Mounting Kit, for details. Seakeeper ConnectBox 3D Model available upon request.
- Mount ConnectBox Replacement Blank insert into Seakeeper 26 top cover at the original location of the ConnectBox.
4.0 Cooling Installation
4.1 Cooling Installation Introduction
The Seakeeper 26 is shipped with the cooling circuit filled and ready for use. Only a quick confirmation of glycol level is required.
Reference Documents & Drawings:
- 90244 – Seakeeper 26 Hardware Scope of Supply
- 90310 – Seakeeper 26 Cable Block Diagram
- 90320 – Seakeeper 26 Cooling Water Schematic
- TB-90191 – Seawater Cooling Pump Recommendations
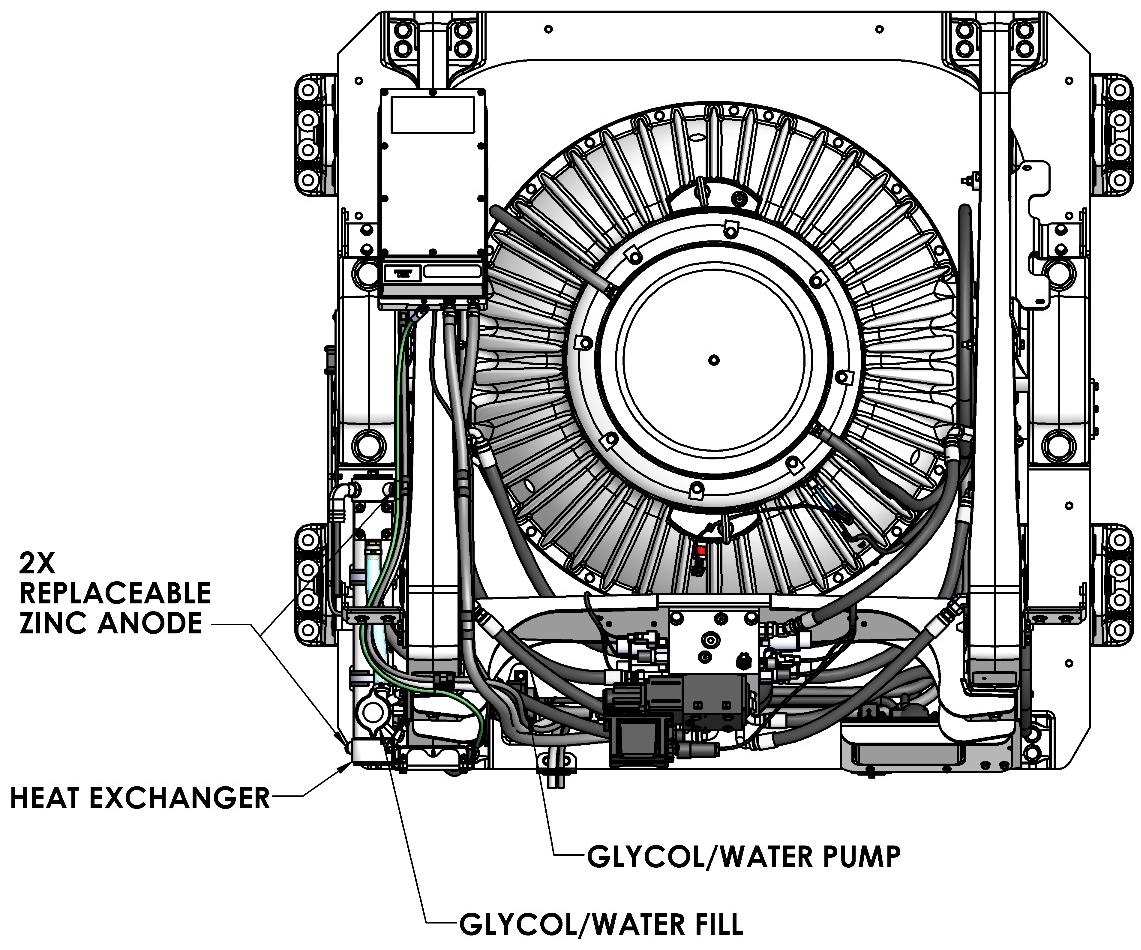
4.2 Connecting Seawater to Heat Exchanger
4.2.1 Installation Considerations
- Installer is responsible for supplying a dedicated seawater pump and associated plumbing. Seawater connections on the Seakeeper heat exchanger mate with ¾ in. (19 mm) hose.
- There is no need to disconnect hose from glycol pump except to replace the pump. In this case, provision will need to be made to catch draining glycol as plumbing is disconnected. Use caution to avoid breaking plastic hose connections on pump casing.
- An output is available from motor drive box to power and automatically control seawater pump (Cable 5). This pump must operate on 230 VAC single phase and consume less than 5 A. Pumps requiring other voltages or higher current can still be controlled by using this supply from motor drive to trigger an installer-supplied contactor, but a separate source of power must be provided.
- A dedicated through-hull fitting should be installed for each Seakeeper unit onboard the vessel to ensure sufficient seawater flow to each unit.
- Maximum seawater pressure in heat exchanger is 20 psi (1.4 bar).
- Seawater flow requirement through heat exchanger is 4 GPM (15.1 LPM) minimum and 8 GPM (30.3 LPM) maximum under all operating conditions of the boat. When sizing seawater pump, installer should factor in losses for raw water plumbing. In addition to initial operation at dock, new Seakeeper installations should be checked to be within the flow requirements while vessel is at speed. Flows higher than 8 GPM (30.3 LPM) could affect heat exchanger life.
4.2.2 Connecting Seawater to Heat Exchanger
Refer to Figure 4 for typical seawater plumbing arrangement.
- Connect seawater pump to Seakeeper dedicated through-hull fitting. A strainer and seacock valve should generally be installed between the seawater inlet and the pump.
- Connect seawater from installer-supplied pump to lower ¾ in. (19 mm) hose barb on heat exchanger. Use the same practices as other below waterline seawater plumbing. Required flow rate is 4 GPM (15.1 LPM) minimum and 8 GPM (30.3 LPM) maximum. Refer to Figure 1, in Section: Cooling Installation – Introduction.
- Connect seawater discharge (upper hose barb) to overboard drain. Use the same practices as typical below waterline seawater plumbing.
- In addition to initial operation at dock, new installations should be checked with a flow meter for minimum 4 GPM (15.1 LPM) flow while vessel is at speed and when backing down.
- If no other method of confirming flow is available, discharge line may be temporarily diverted to a bucket. Flow is calculated from time to fill a known volume.
- A self-priming seawater pump (customer/installer supplied) may be required due to installation location to maintain water flow in all underway conditions where cavitation near the intake may occur and potentially cause an air-lock condition restricting seawater flow to the heat exchanger.
- Inspect raw water plumbing after sea trial for any signs of leakage.
- Heat exchanger contains removable end-caps to provide access for cleaning the tube bundle.

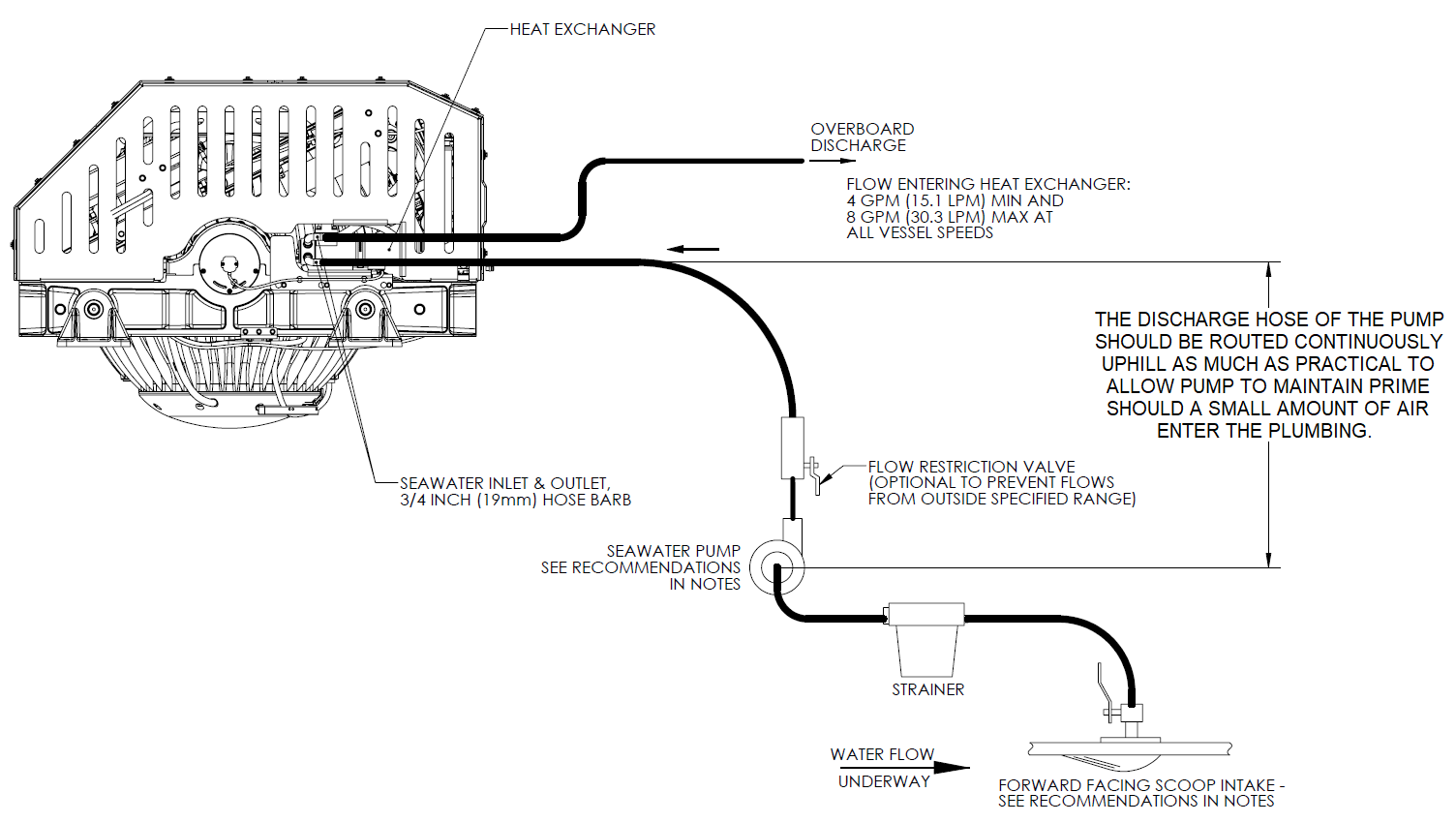
4.3 Adding Coolant
- Cooling system is filled to proper level when shipped, with a mixture of 50% ethylene glycol and 50% distilled water. The clear tube between the thermostat housing and reservoir should be filled with green coolant mixture. If level has dropped, check for evidence of leaks at all connections before adding fluid as described below. If coolant is at the correct level, skip to Section: Connecting Seawater to Heat Exchanger.
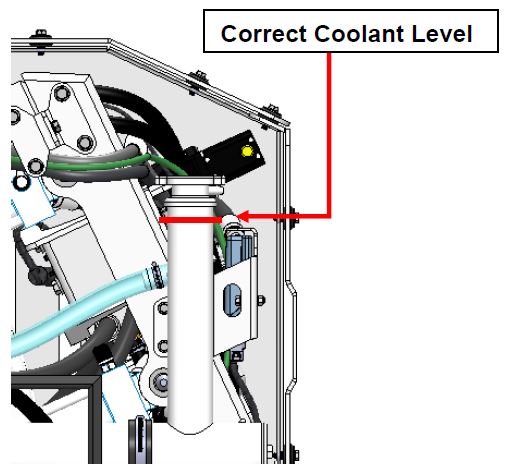
- Mix 50% ethylene glycol with 50% distilled water in a clean container. Refer to Table 1 or glycol manufacturer’s literature for freezing points.
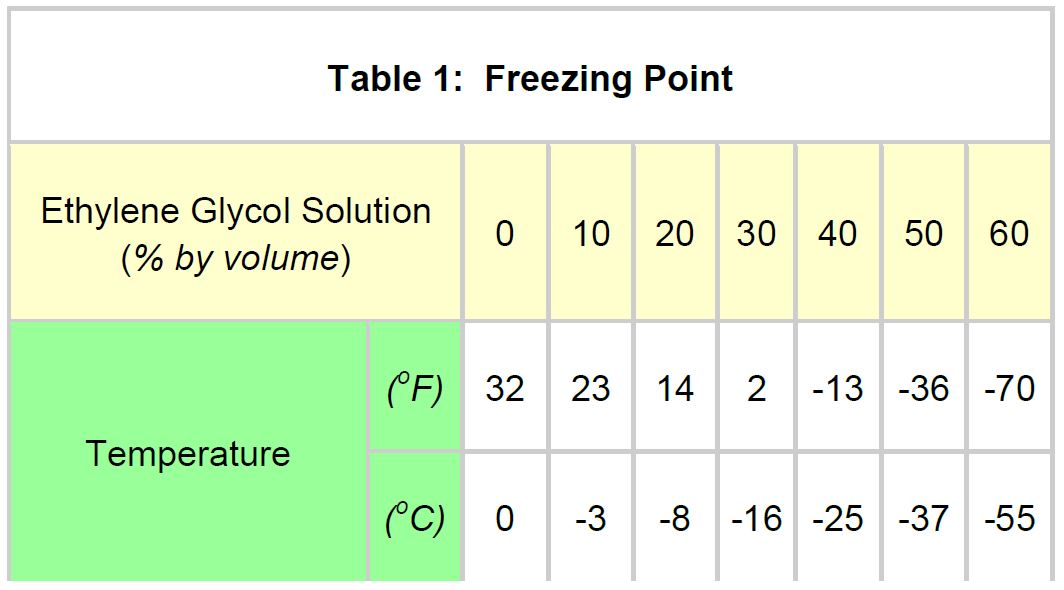
- Remove pressure cap on top of reservoir. Pour mixture in until level reaches top of clear tube as shown in Figure 5. Filling reservoir above this level will not cause any damage but coolant may be expelled from pressure relief port below cap due to normal thermal expansion of coolant.
- Connect 24 V to controller.
- At the Display check for any ALARMS
- Press the POWER ON/OFF button.
- The flywheel will start to spin and the glycol pump will start.
- Recheck glycol level with fluid circulating in coolant circuit. Sight down inside reservoir and check that coolant level is above upper port on reservoir as shown in Figure 5. Replace cap.
- After several minutes of running, press POWER ON/OFF button
to turn power off to the flywheel and glycol pump. The glycol pump will stop, and the flywheel will coast to a stop.
- At the Display check for any ALARMS
- The cooling system is self-purging. If small amounts of air are in the system, they will most likely be dislodged during the first sea trial. Re-check level after sea trial and add fluid if required.
5.0 Installation Requirements
5.1 Installation Requirements Introduction
This section describes the first start up of the Seakeeper.
Reference Documents & Drawings:
Link to Seakeeper manuals
- 90266 – Seakeeper 26 Operation Manual
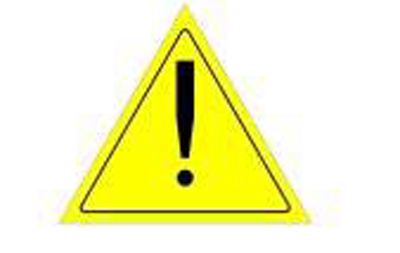
- Previous sections for mechanical, electrical and cooling installation must be completed before this start up sequence is initiated.
- Before continuing, covers must be installed unless the Seakeeper is inaccessible and there is no risk to injury. Also, the area around the Seakeeper must be clear of personnel and equipment.
5.2 Required Supplies for Seakeeper Installation
(Not Supplied With the Seakeeper)
Item | Description | Qty | Installation Manual Reference Section | Other Reference | System |
---|---|---|---|---|---|
1 | Adhesive and cleaning supplies for bonding to hull | Mechanical Installation | Mechanical | ||
2 | Soundproofing Considerations | Selection of Installation Location | Mechanical | ||
3 | Spreader bar for lifting Seakeeper | Transport and Unpacking | P/N 80029 | Mechanical | |
4 | Circuit Breaker, AC, 2-Pole, 30 A | 1 | Electrical Equipment Power Connections | Dwg 90310 | Electrical |
5 | Circuit Breaker, DC, 1-Pole, 15 A | 1 | Electrical Equipment Power Connections | Dwg 90310 | Electrical |
6 | M6 terminal lug for grounding Seakeeper at rear brace | 1 | Electrical Equipment Ground Connections | Electrical | |
7 | Cable, 10 AWG, for grounding Seakeeper at rear brace to vessel ground | AR | Electrical Equipment Ground Connections | Dwg 90310 | Electrical |
8 | Sili-Thane 803 Marine Sealant (or equivalent) | AR | Bolt-In Installation, Installation of Seakeeper and Saddle Installation, Installation of Seakeeper | Mechanical | |
9 | Nickel-based Anti-Seize | AR | Bolt-In Installation, Installation of Seakeeper and Saddle Installation, Installation of Seakeeper | Mechanical | |
10 | Seawater Pump, 24 VAC | 1 | Electrical Equipment Power Connections | Dwg 90320 | Electrical |
11 | Relay for seawater pump control (Not required if using 230 VAC pump) | 1 | Electrical Equipment Power Connections | Electrical | |
12 | ¾ in. (19 mm) ID seawater hose | AR | Cooling Installation | Dwg 90320 | Cooling |
13 | Hose clamps for seawater plumbing to ¾ in. (19 mm) hose barb (2 per hose barb) | 4 | Cooling Installation | Dwg 90320 | Cooling |
14 | Through-hull fittings (1 high-speed pick-up / 1 overboard discharge) | 2 | Cooling Installation | Dwg 90320 | Cooling |
15 | Seawater strainer | 1 | Cooling Installation | Dwg 90320 | Cooling |
16 | Seacock valve | 1 | Cooling Installation | Dwg 90320 | Cooling |
17 | Flow restriction valve (optional) | 1 | Cooling Installation | Dwg 90320 | Cooling |
AR = As Required
Dwg = Drawing
6.0 Installation and Start Up Checklist
6.1 Installation and Start Up Introduction
Reference Documents & Drawings
- 90271 – Seakeeper 26 Bolt-In Installation Details
- 90272 – Seakeeper 26 Bond-In Installation Details
- 90310 – Seakeeper 26 Cable Block Diagram
- 90320 – Seakeeper 26 Cooling Water Schematic
- 90437 – Seakeeper Commissioning Form
- SWI-105 – Commissioning Checklist
The Installation and Start Up Checklists in this section provide an overview of the primary steps covered in the installation manual and should be referenced throughout the installation process. Upon completing the installation, the installer should commission each Seakeeper unit with the Seakeeper Commissioning Form (90437). The Commissioning Checklist (SWI-105) provides a checklist of items to inspect and verify during the commissioning process and serves as a supplement to the Commissioning Form.
All Seakeeper stabilizers should be commissioned to verify that installation specifications and requirements have been implemented properly. The commissioning process should include completion of the Commissioning Form, all the items in the Installation Checklist, and verification of operation without alarms or abnormal behavior.
Please Complete Checklist and E-mail to support@seakeeper.com.
6.2 Installation Checklist
6.2.1 Mechanical Checklist
(Reference Installation Manual Section: Mechanical Installation)
- Seakeeper foundation installed in hull
- Foundation bolts torqued to specification
- Clearances around the Seakeeper meet service and operating specifications and no obstructions are within the Seakeeper envelope
6.2.2 Electrical Checklist
(Reference Seakeeper Drawing No. 90310 – Seakeeper 26 Cable Block Diagram & Installation Manual Section: Electrical Installation)
Mount Components
- Display (near helm)
Connect Cables
- DC Power Input Cable:
- Connect DC Power Input Cable (P/N 30179, 10 ft (3 m)) from Seakeeper to 24 VDC power at customer-supplied connection box or directly to circuit breaker.
- Plug connector of DC Power Input Cable into mating connector on Seakeeper wire harness.
- Ground Cable (Customer Supplied):
- Install lugs on both ends of customer-supplied 10 AWG ground cable.
- Connect one end of Ground Cable to nearest vessel ground and other end to Seakeeper rear brace.
- AC Power Input Cable (Seakeeper Supplied):
- Connect the AC Power Input Cable from Drive Box to 230 VAC single phase at customer-supplied connection box or directly to circuit breaker.
- Seawater Power Output Cable (Seakeeper Supplied):
- Connect the Seawater Power Output Cable (P/N 30239, 9.8 ft (3 m)) from Drive Box to customer-supplied 230 VAC seawater pump.
- CAN Communications (Display) Cable (Seakeeper Supplied):
- Connect female end of CAN Communications Cable (P/N 30243, 82 ft (25 m)) to mating connector on Seakeeper wire harness.
- Route CAN Communications Cable from Seakeeper to helm (male end goes to helm).
- Connect male end of CAN Communications Cable at helm to CAN Tee Adapter.
- Connect Display and Seakeeper-supplied (P/N 30301, 2 ft (0.6 m)) cable to CAN Tee Adapter (P/N 30244) with CAN Terminator (P/N 30249).
6.2.3 Cooling Checklist
(Reference Installation Manual Section: Cooling Installation)
- Verify coolant level in heat exchanger coolant reservoir.
- Connect seawater hoses / open sea cocks to heat exchanger and test seawater pump.
- Verify 4 GPM (15 LPM) minimum and 8 GPM (30 LPM) maximum seawater flow through heat exchanger under all operating conditions of the boat.
7.0 Revision History
Revision | Description | Date |
7 | Minor edits. | 01MAR2021 |
8 | ConnectBox launch modifications. Removed 20HD model. Removed bonding installation. Minor edits throughout. | 10OCT2023 |
5.3 Tools Required for Installation
List of Common Tools That May Be Required for Installation
Item | Description | Use |
---|---|---|
1 | Hoist, Forklift, or Crane | Unpacking and lifting the Seakeeper |
2 | Transfer punch kit | Locating foundation holes |
3 | Drill / Drill Press | Bolt holes |
4 | ½ in. drive Torque wrench | Foundation bolts |
5 | ½ in. drive extensions | Foundation bolts |
6 | 24 mm Socket | Foundation bolts |
7 | Wire cutter | DC Power, AC Power cables |
8 | Wire stripper | DC Power, AC Power cables |
9 | Phillips head screwdriver | Cover Panels |
10 | 13 mm Socket Wrench | Cover Panels |
11 | 3 mm hex key | Gimbal sensor mount plate |
12 | 2.5 mm hex key | Gimbal angle sensor |
13 | ¼ in. nutdriver | Hose clamps |
14 | Terminal or quick disconnect crimper | Power cables |
15 | Utility knife | Scoring cable jackets |
16 | 10 mm Socket Wrench | Ground Stud |
6.3 Start Up Checklist
(Reference Installation Manual Section: Start Up & Operation Manual Section: System Operation)
- Remove lifting eye bolts, replace with sealing screw/washers provided, and install cover panels
- Turn on 24 VDC circuit breaker
- Turn on 230 VAC circuit breaker
- Verify display works and no ALARMS are present
- If display does not work, turn off both circuit breakers immediately.
- Check polarity of 24 VDC power per Section: Electrical Equipment Power Connections – DC Power Connection Instructions.
- Follow instructions in Section: Start Up Instructions to turn on the Seakeeper
- Verify seawater pump turns on when the Seakeeper is turned ON
- Verify that no ALARMS are present
- Follow instructions in Section: Start Up Instructions to turn off the Seakeeper
- AC & DC power and seawater pump may be turned off after the Seakeeper is turned off by placing the Seakeeper in LOCK mode and turning the Seakeeper off.
- Seakeeper 26 takes 6+ hours to coast down to 0 RPM from full speed