Seakeeper 9 Installation Manual (90222-10); S/N 9-212-3388 to 9-234-4899
3.0 Electrical Installation
3.1 Electrical Installation Introduction
This section for electrical installation explains how to mount the electrical equipment and how to connect the electrical cables.
Reference Documents & Drawings:
- 90221 – Seakeeper 9 Hardware Scope of Supply
- 90223 – Seakeeper 9 Operation Manual
- 90467 – 2nd Helm Control Station Kit
- 90257 – Seakeeper 9 Cable Block Diagram
- 90438 – Touchscreen Display Envelope and Mounting Details
- MFD Compatibility Technical Bulletins
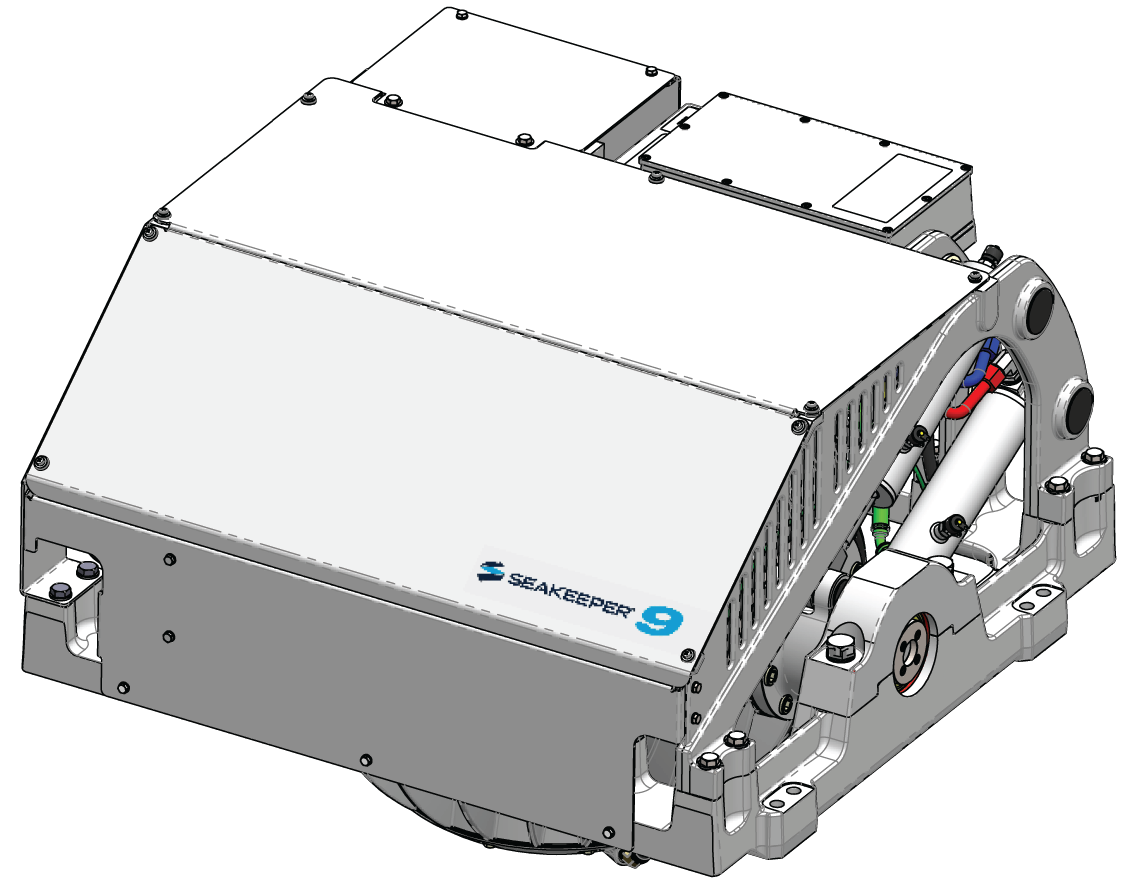
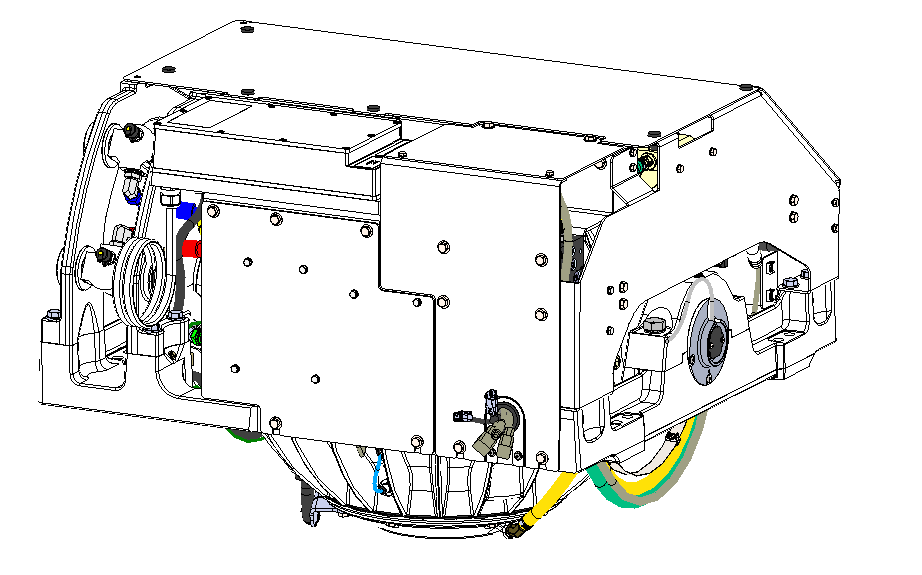
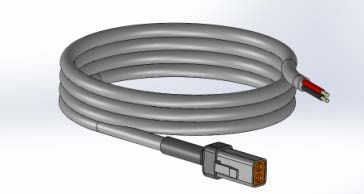
24 VDC Power Input Cable
P/N 20248
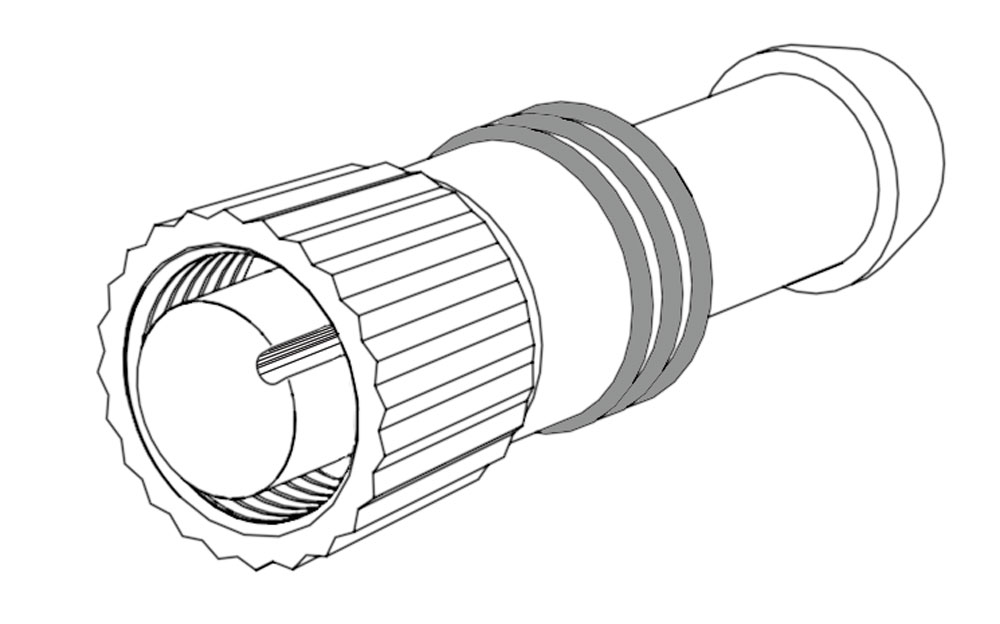
P/N 30249
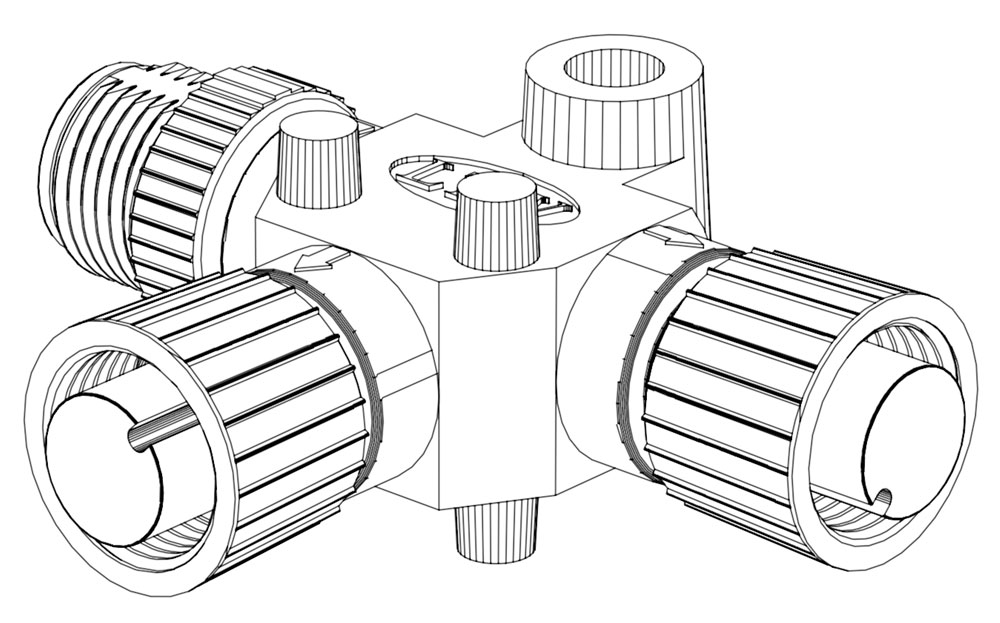
P/N 30244

P/N 30298
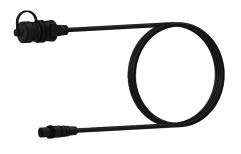
USB Extension Cable
P/N 30300
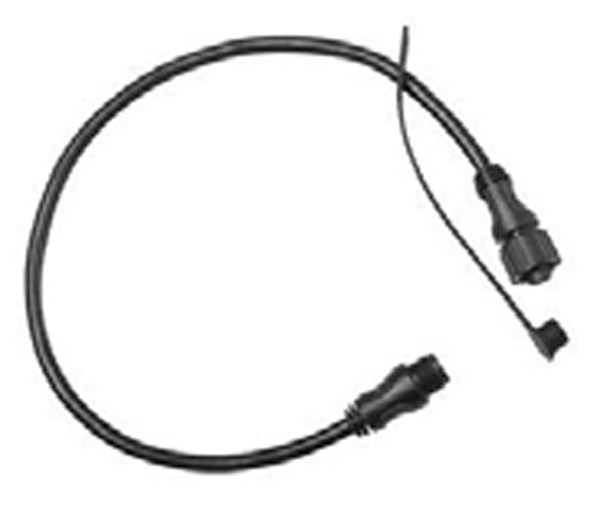
2 ft. Cable
P/N 30301
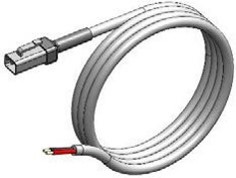
DC SW Pump Input
P/N 30327
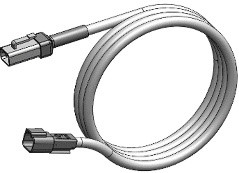
DC SW Pump Output
P/N 30327
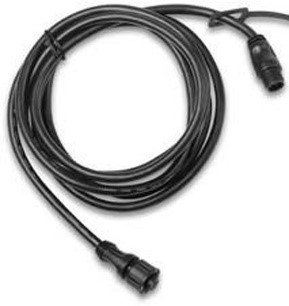
25 m Cable
P/N 30243
Figure 1 – Electrical Equipment for Seakeeper 9
3.2 Electrical Equipment Power Connections
3.2.1 230 VAC Power Source Requirements
- 230 VAC (nominal), 1 Phase, 50/60 Hz, 20 A
- For installations of more than one Seakeeper, a separate circuit breaker should be used for each Seakeeper Motor Drive Box.
3.2.2 Drive Box AC Power Input Connection Instructions
- Cable 2: 3 x 10 AWG (3 x 6 mm2 CSA), 10 ft. (3 m) length, Seakeeper supplied pre-installed.
- Locate Cable 2 for AC power input to the Drive Box at the outward of three cable glands.
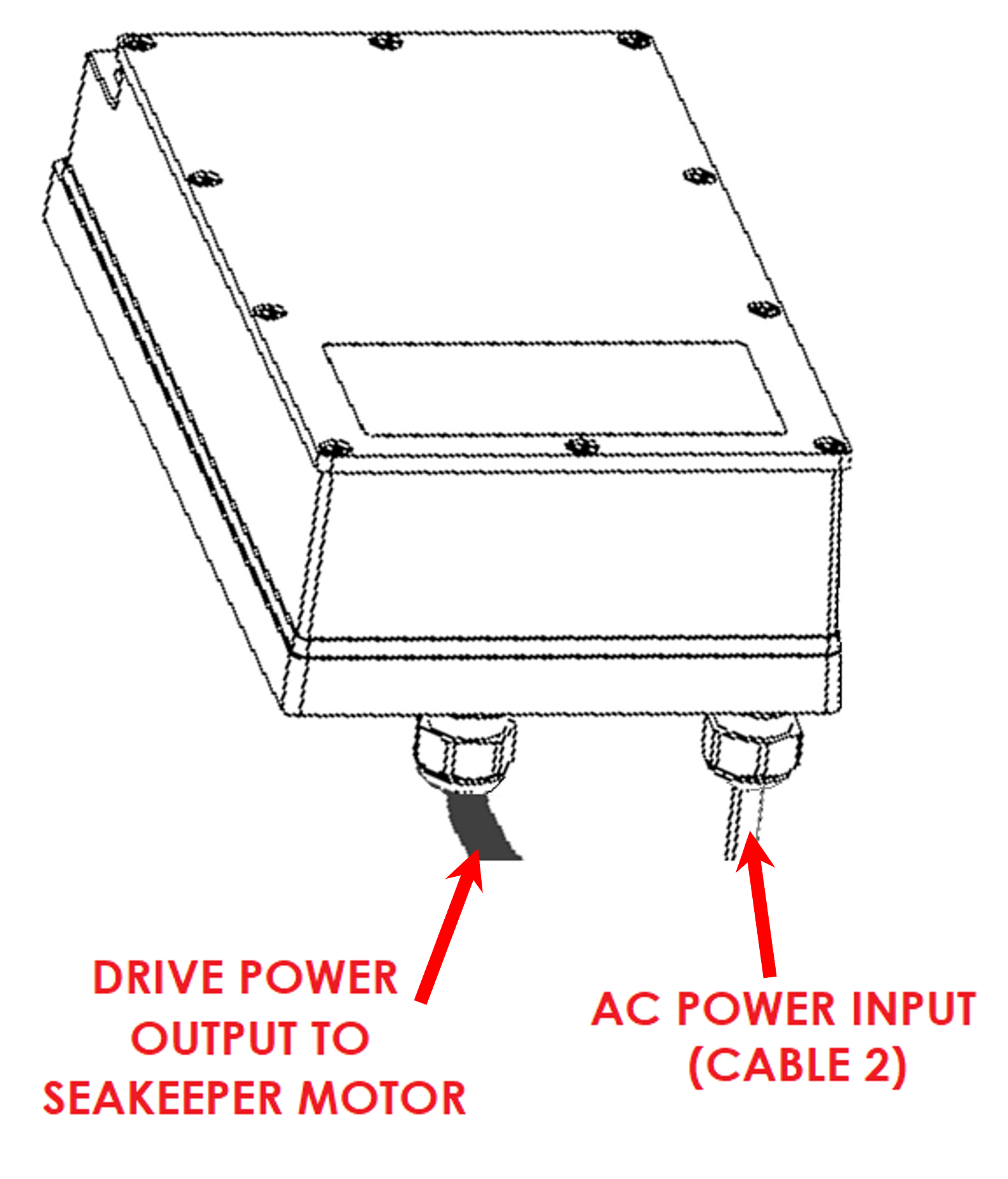
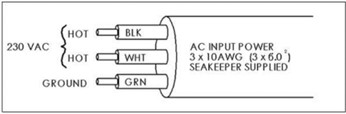
- Connect 230 VAC wires in Cable 2 to a 20 A, double-pole Circuit Breaker at an AC power distribution panel according to Figure 3 above.
3.2.3 24 VDC Power Source Requirements
- One 24 VDC, 10 A (Customer supplied) for Seakeeper Control Power, AND
- One 24 VDC, 10 A (Customer supplied) for DC Seawater Pump.
- A separate breaker should be used for each Seakeeper.
3.2.4 DC Power Connection Instructions
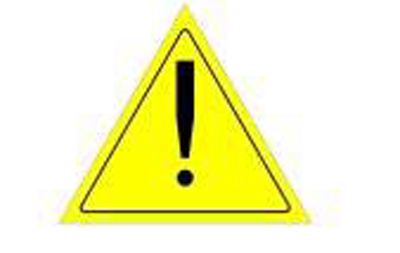
Reversing polarity on the DC power input to the Seakeeper can result in damaging the electronics in the control system.
- 24 VDC, 10 A, 2 x 12 AWG (3 x 4.0 mm2 CSA) customer supplied.
- Install Seakeeper provided DC Power Input Cable, P/N 20248 as Cable 1 (as shown in Drawing No. 90257).
- Route Cable 1 to DC Power Distribution Panel.
- Terminate positive (B+, Red ) conductor to +24 VDC.
- Terminate negative (B-, Black) conductor directly to battery negative terminal.
- Before connecting Cable 1 to Seakeeper, check for proper voltage and polarity with a DC multimeter using Figure 7 below.
- Connect Cable 1 to 24 VDC input receptacle on Seakeeper.
- Install Seakeeper provided DC Power Input Cable, P/N 20248 as Cable 1 (as shown in Drawing No. 90257).
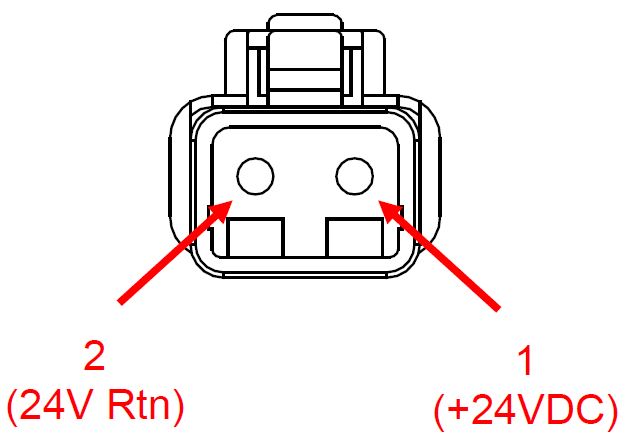
3.2.5 DC Seawater Pump 24 VDC Power Input Connection Instructions
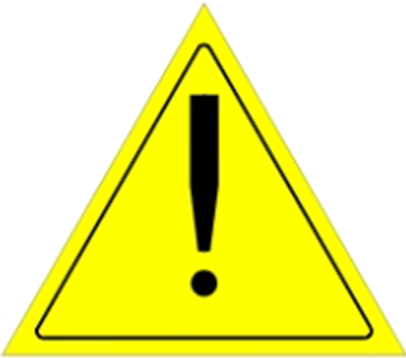
Connecting the DC Seawater pump in any other manner than recommended by Seakeeper may cause internal failure.
- Install Cable 8 (P/N 30327) to Seakeeper 9 “SW Pump DC In” (as shown in Drawing No. 90257) with overcurrent protection corresponding to seawater pump selected.
- Connect the 16AWG positive conductor (Red) through dedicated overcurrent protection device (customer supplied), maximum of 10 A, to dedicated battery isolation switch.
- Connect the 16 AWG negative conductor (Black) directly to battery negative terminal or DC main negative bus bar.
- Before connecting Cable 8 to Seakeeper, check for proper voltage and polarity with a DC multimeter using Figure 8 below.
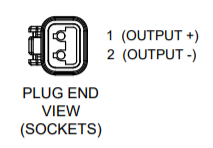
- Connect Cable 8 to Seawater Pump 24 VDC In connector on the Seakeeper, DEUTSCH DT04-2P connector.
3.2.6 DC Seawater Pump 24 VDC Power Output Connection Instructions
- Connect Cable 5 to the Seakeeper 9 “SW Pump 24VDC Out” for DC power to the seawater pump.
- Cable 5 is a 2 x 16 AWG cable, 16 ft (5m) length with a size 16 female Deutsch plug.
- Pumps rated at 24 VDC, 10 A maximum, customer-supplied, must be configured with a Deutsch DT series, 2-pin receptacle to mate with the connector shown in Figure 9.
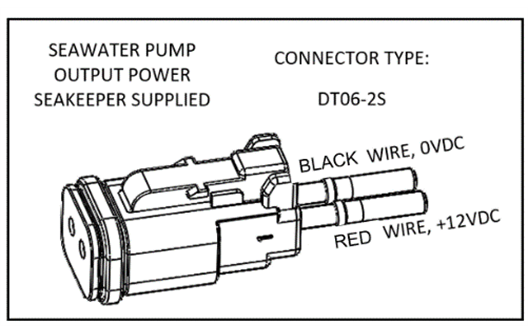
- Cable 5 must be routed and installed in the vessel from the Seakeeper 9 “SW Pump 24VDC Out” Deutsch connector (pins end) to the DC seawater pump cable Deutsch connector (socket end).
- Connect Cable 5 plug end (socket end) to the customer-supplied receptacle end (pins end). The recommended wiring is shown in Figure 10.
- Contact Seakeeper if desired to install customer-supplied relay on Cable 5 to power seawater pump.
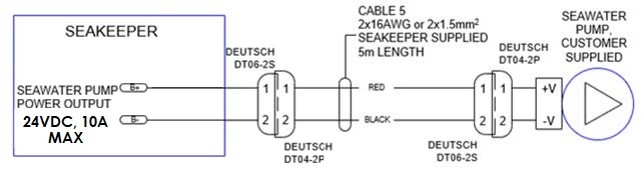
3.3 Electrical Equipment Ground Connections
3.3.1 Seakeeper to Vessel Ground Connection Instructions
- Connect the Seakeeper foundation to vessel ground, as shown in Figure 8.
- Install Cable 6 (10 AWG or 6 mm2, Customer supplied) from the M6 brass ground stud on the Seakeeper rear brace to a suitable vessel ground.
- EN/IEC 90204-1 Clauses 6.3.3 and 8.2.3
- ABYC E-11 July 2018 Clauses 11.5.2 and 11.16.1.
- Ground connection should be made with vessel bonding system, if available. However, the ground is not referring specifically to a bonding system but for outboard boats generally refers to the outboard engine negative terminal. Per ABYC E-11 (2018), Clause 11.5.2.7.4: If the negative side of the DC system is to be connected to the ground, the connection shall be made only from the engine negative terminal, or its bus, to the DC grounding bus. This connection shall be used only as a means of maintaining the negative side of the circuit at ground potential and is not to carry current under normal operating conditions.
- A proper ground connection is critically important for corrosion protection and helps to ensure the ignition protection of the unit by ensuring it does not carry any stray current.
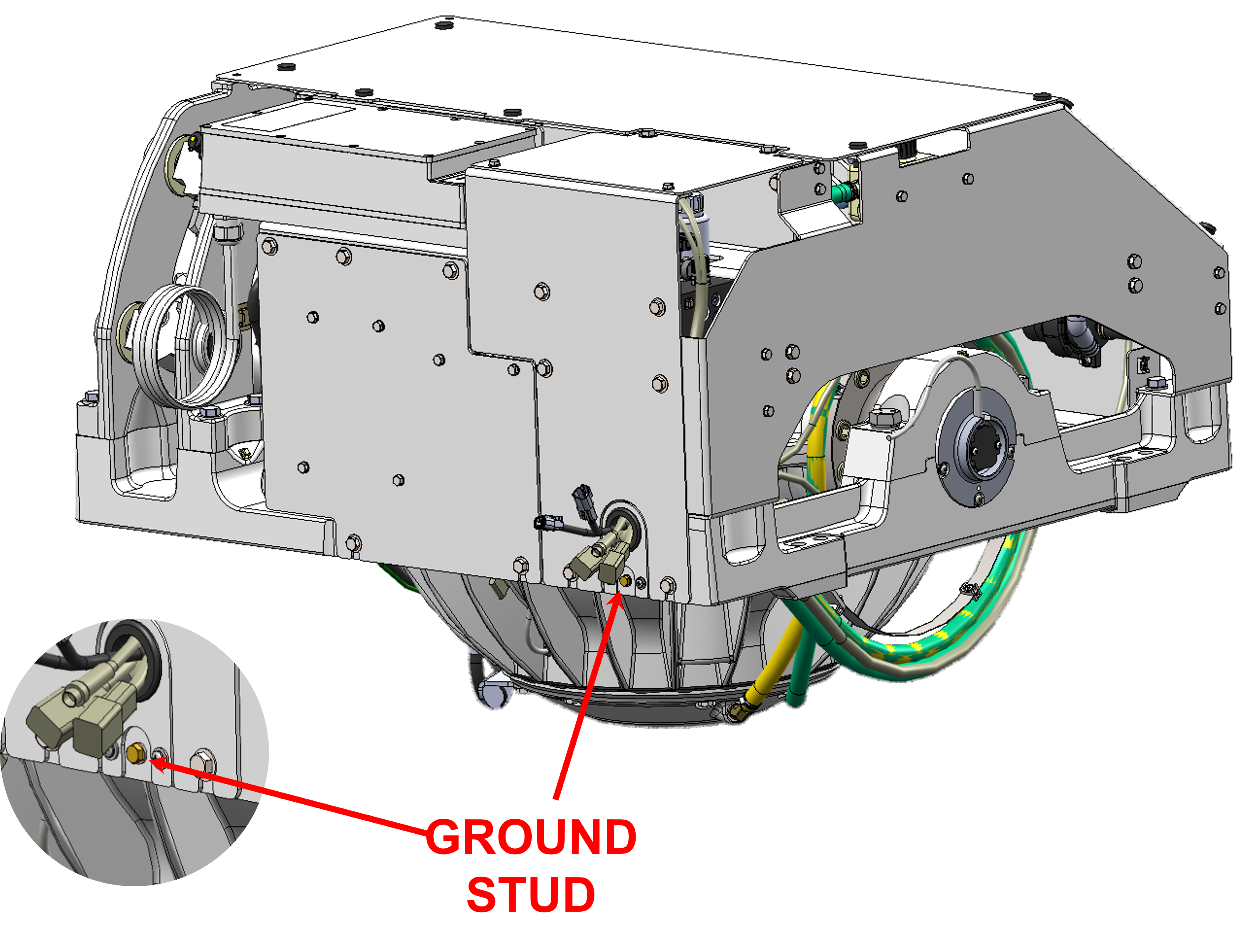
Note: THIS LOCATION SHOULD ONLY BE USED FOR GROUNDING THE SEAKEEPER TO THE VESSEL GROUND
3.4 Electrical Equipment Mounting
Precautions: Each item of electrical equipment has specific mounting instructions. These instructions
should be followed to ensure proper function of the Seakeeper.
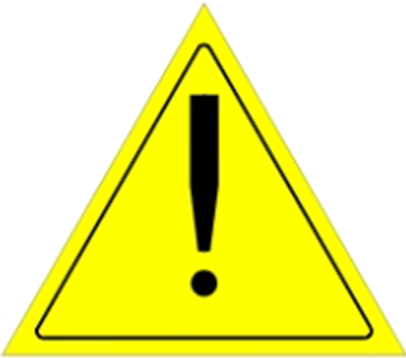
Do NOT move Seakeeper mounted components from their
locations or incorrect Seakeeper operation will result.
3.4.1 Seakeeper 9 Display Options
The Seakeeper 9 includes a 5″ Touch Screen Display (P/N 30296) standard. The 5″ Touch Display can be integrated with compatible Multifunction Display systems, per the MFD Compatibility Technical Bulletins.
The Seakeeper MFD App provides an interface for controlling the Seakeeper 9 and viewing the Settings, Service, Info, and Alarm pages from a compatible MFD.
The following figures provide schematics of display options. The subsequent sections outline the instructions and references for connecting the Seakeeper 9 to MFD display option peer Figure 9.
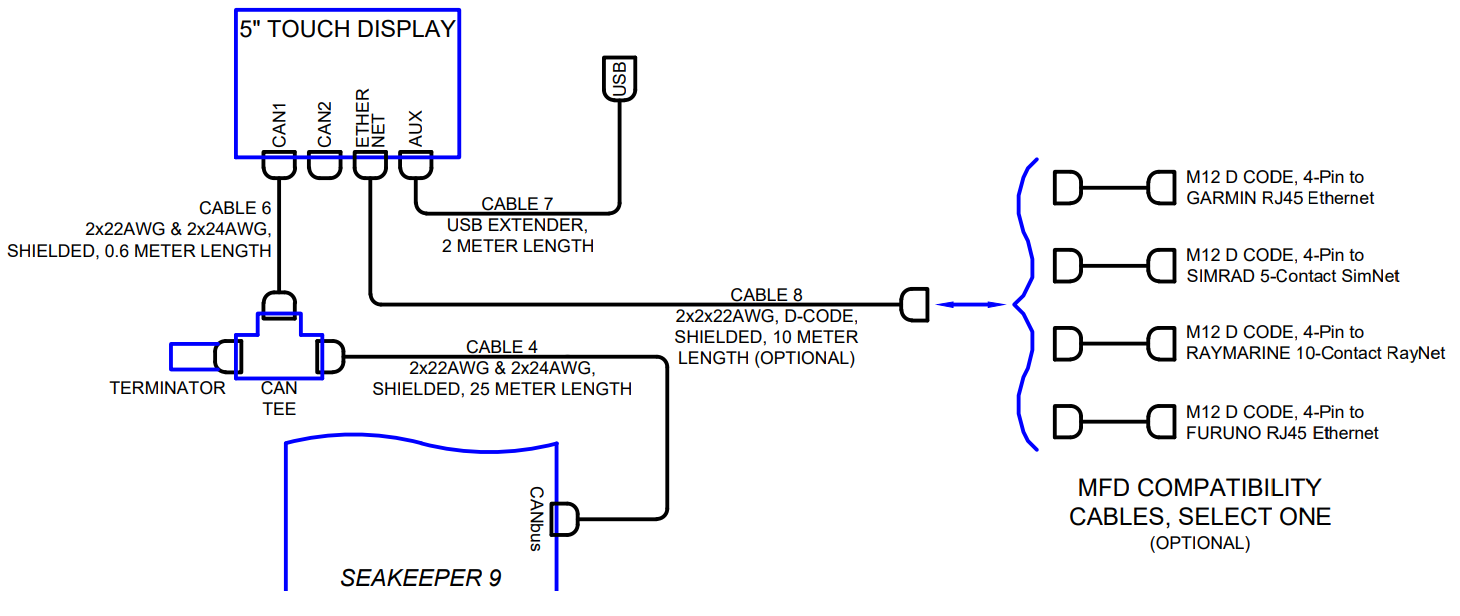
3.4.2 Installing the Seakeeper 5″ Touch Display
The desired location of the Operator Station must be determined for the vessel arrangement. For example, the operator display may be located on the bridge console or near the Seakeeper if integrated with a compatible MFD.
- Touch Display Mounting Instructions, Surface Mount
- Console space required: Approx. 5.24 W x 3.70 H in. (133 x 94 mm)
- Mounting Instructions, Surface Mount: See Drawing No. 90438 – 5″ Operator Display Envelope and Mounting Details, for details.
- CAN Communications Cable, Tee Adapter, and Terminator Mounting Instructions (See Figure 10)
- Rear mount Tee Adapter (P/N 30244) on vessel console panel, within 2 ft (0.6 m) of Display.
- Hardware required: One mounting screw for .197 in. (5 mm) diameter mounting hole on Tee Adapter. Terminator goes on the far end of the tee adapter from the Seakeeper.
- Run CAN Communications Cable (P/N 30332, Cable 4) from Seakeeper (female end) to Tee Adapter (male end).
- Install Can Cable (P/N 30301, Cable 6) from Tee Adapter (male end) to CAN1 connector at rear of 5″ Touch Display.
- Install Terminator (P/N 30249) into male connector of Tee Adapter.
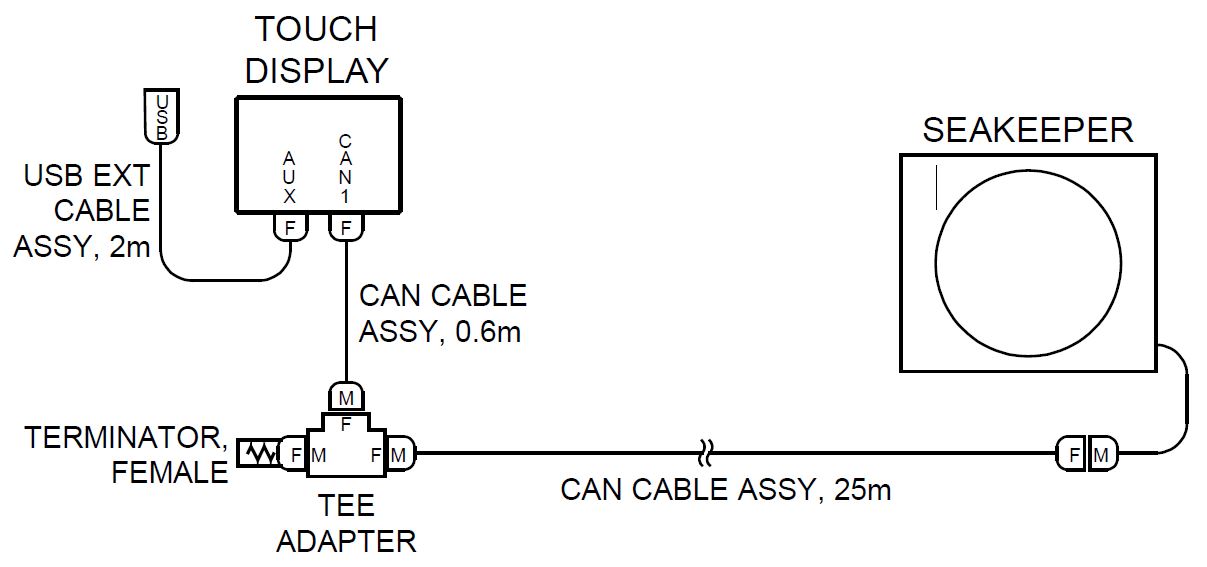
- USB Extension Cable Assembly Mounting Instructions
- Console space required: Approx. 2 W x 2 H in. (51 x 51 mm), within 6 ft (2 m) from Touch Display.
- Mounting Instructions, Surface Mount: Use panel cutout as shown in Section: Display Installation Template. Maximum panel thickness 1/8 in. (3.2 mm).
- Install sealed USB connector end of the extender cable assembly in panel from rear and secure with hex jam nut (provided) on front.
- Connect M12 connector end of the extender cable assembly to the rear of the Touch Display on receptacle AUX.
3.4.3 Connecting an Optional Compatible MFD
- The Seakeeper 9 can be connected to a variety of available MFD systems. Refer to the Technical Bulletins Section of the Seakeeper Technical Library for manufacturer specific MFD compatibility technical bulletins.
- MFD specific Technical Bulletins will be updated regularly as new MFD systems become compatible. Currently GARMIN, RAYMARINE, NAVICO (Simrad, Lowrance, B&G), and FURUNO offer compatible MFD models.
- Once a compatible MFD has been selected, refer to the appropriate manufacturer specific Technical Bulletin for integration instructions.
- Connect Seakeeper-supplied Cable 8 (P/N 30330), D-Code 10 m cable to MFD manufacturer-specific Ethernet adapter cable. Custom Ethernet cables for specific MFD manufacturers are available through Seakeeper and must be purchased with the Seakeeper 9 if connecting to an MFD.
3.4.4 Connecting a Second Operator Station
NOTE: A compatible MFD over the Seakeeper 5” Touch Screen Display is recommended as they economically provide broader features and functionality. Reference Seakeeper drawing 90467 – Helm Display 2nd Operator Station Kit and 90257 – Seakeeper 9 Cable Block Diagram for installation details.
Second Operator Station locations may be on a flybridge or in an engine room.
- Install 2nd 5″ Touch Display as first 5″ Touch Display in desired location.
- Install 2nd Operator Station Tee Adapter (P/N 30244) with Terminator (P/N 30249).
- Figure 11 shows the entire serial communications link for 2 Operator Stations. The Terminator must be installed on the Tee Adapter farthest from the Seakeeper.
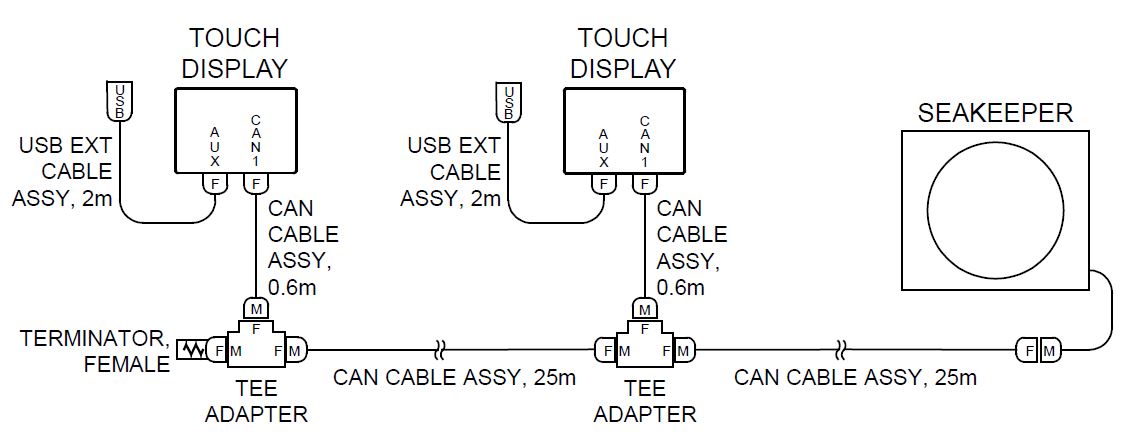
- Route a second CAN Cable Assembly (P/N 30332) from the 1st operator station (female end) to the 2nd Operator Station Tee Adapter as shown in Figure 11.