Seakeeper 9 Operation Manual (90223-10); S/N 9-233-4900 to Current
4.1 Power Failures and Alarms Introduction
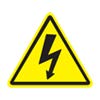
The Motor Drive Box contains hazardous voltage and the cover should not be removed while the flywheel is spinning and the AC input voltage is present. This high voltage exists even if the flywheel is coasting down and the supply voltage has been shut off. The flywheel must be at 0 RPM and AC input power disconnected for at least 10 minutes prior to any service work on the motor drive box.
____________________________________________________________________________________________
The operator should physically examine the Seakeeper following an alarm. Continuing to reset alarms without service intervention can result in damage or personnel injury.
____________________________________________________________________________________________
The flywheel must be at Zero (0) RPM and AC input power disconnected for at least 10 minutes prior to any service work on the Seakeeper.
The Seakeeper 9 has safety features, such as alarms and warnings, that pop-up on the Seakeeper
Application and are signaled on the ConnectBox to protect the Seakeeper as well as the vessel. The brake can be locked from the Application, ConnectBox or by shutting off power at the supply breakers, preventing the Seakeeper from precessing.
In the event of a DC control power failure, the brake automatically locks the Seakeeper so it cannot generate anti-rolling torque loads.
There are three sources of power to the Seakeeper 9:
- 24 VDC powers the Seakeeper for all the control electronics.
- 24 VDC powers the DC Seawater Pump for cooling water supply.
- 208 – 230 VAC powers the Motor Drive Box to drive the motor inside the Seakeeper.
These are supplied on cables shown on Drawing No. 90257 – Seakeeper 9 Cable Block Diagram.