Seakeeper 4 / 4.5 Installation Manual (90762-1)
3.0 Electrical Installation
3.1 Electrical Installation Introduction
This section for electrical installation explains how to mount the electrical equipment and connect the electrical cables.
Reference Documents:
- 90737 – Seakeeper 4.5 Hardware Scope of Supply
- 90696 – Seakeeper 4.5 Cable Block Diagram
- 90699 – Seakeeper 4 Cable Block Diagram
- TB-90191 – Seawater Cooling Pump Recommendations
- TB-90621 – Seakeeper Battery Sizing Recommendations
- TB-90640 – ConnectBox Connection Requirements
- Seakeeper MFD Compatibility Technical Bulletins:
- Optional 5″ Touch Display
Because of the different motor power requirements between Seakeeper 4 and Seakeeper 4.5, the Motor Power Connections are separated into independent subsections (Sect. 3.2.1 and 3.2.2). The Control Power, Seawater Power, Ground, and ConnectBox connection requirements (Sect. 3.3 through 3.6) are the same for both models.
The following images show the electrical equipment included with the Seakeeper 4 and 4.5 Hardware Scope of Supply (Drawing No. 90737):
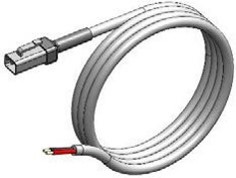
16.4 ft (5 m), P/N 20248
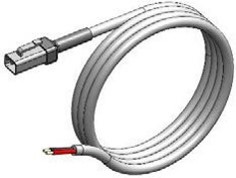
16.4 ft (5 m), P/N 30327
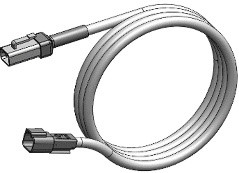
16.4 ft (5 m), P/N 20334
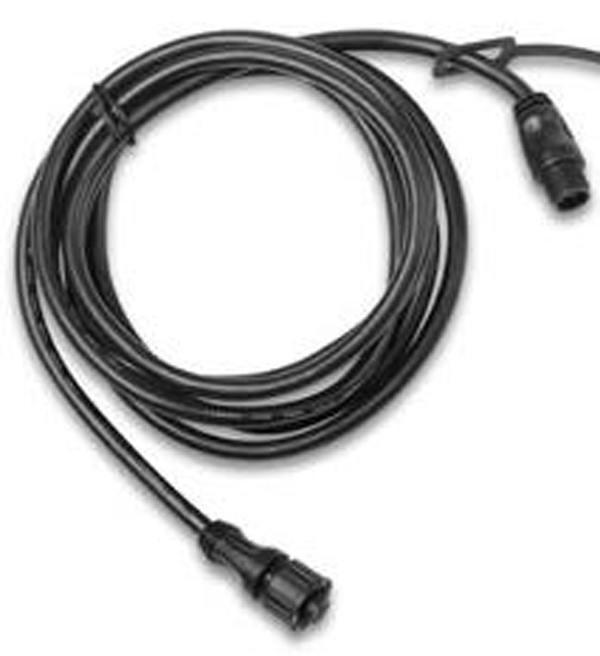
19.7 ft (6 m), P/N 30332
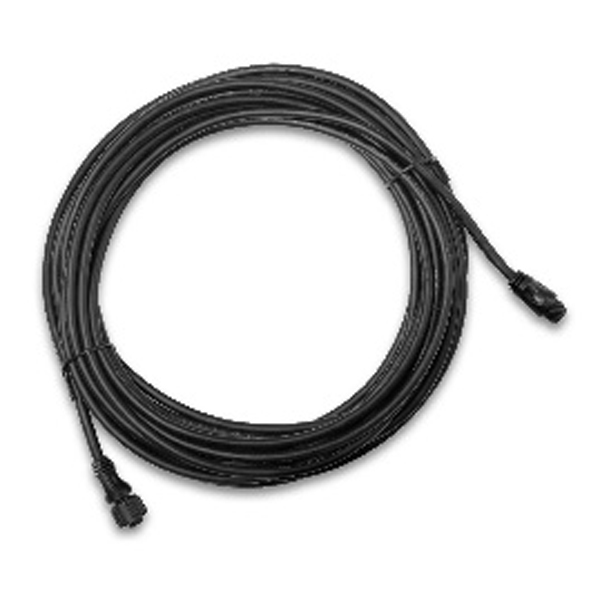
32.8 ft (10 m), P/N 30330
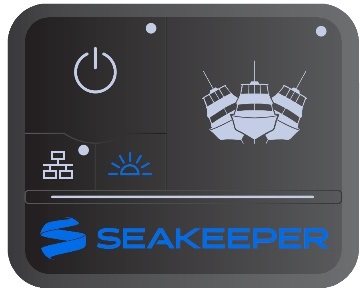
3.2 Motor Power Connections
3.2.1 Seakeeper 4 Motor Power Connection
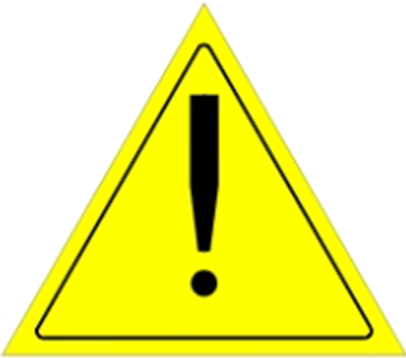
Reversing polarity on the DC power input to the Seakeeper can result in damage to electronics in the control system.
High Current 12 VDC Power Source Requirements
- One 12 VDC, 100 A (Customer supplied) for Seakeeper flywheel motor power.
- A dedicated breaker should be used for each Seakeeper in a multiple Seakeeper installation.
High Current 12 VDC Power Connection
- Connect high-current power red and black cables, 2 AWG conductors, to the 12 VDC power source.
- Both cables (red and black) are supplied at length 13 ft (4 m) and approximately 0.5 m is routed within the gyro frame.
- Connect high-current power positive (B+, red) conductor through 100 A overcurrent protection device, dedicated battery isolation switch (customer supplied), and to battery positive (B+) terminal.
- Connect high-current power negative (B-, black) conductor directly to battery negative (B-) terminal or to vessel main negative bus.
- If the 2 AWG high current 12 V power input conductors are shortened or lengthened, use heavy-duty eyelet (closed end) terminal such as Molex 19221-0235 and follow instructions outlined in the following steps.
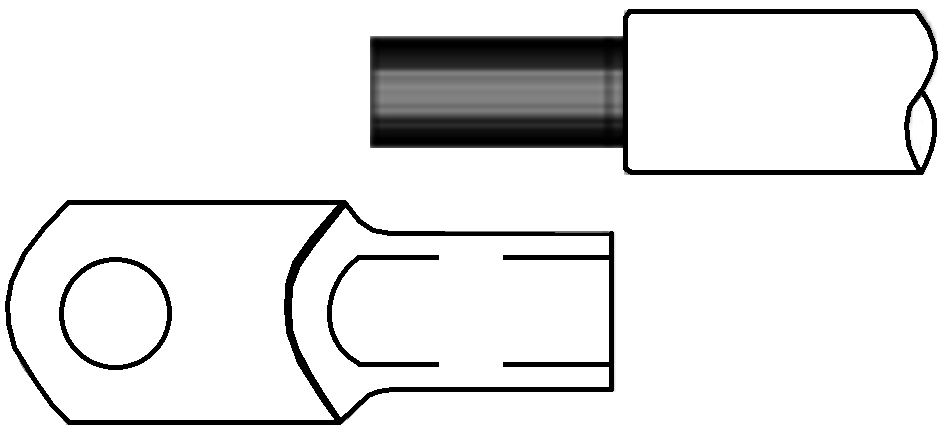
- The bare wire strands should extend fully into the barrel of the heavy-duty eyelet and be crimped in two places if possible then sealed with double-wall heat shrink tubing. Crimp heavy-duty terminals with Quick Cable 4245 Crimp Tool, Molex19284-0034 Crimp Tool, or equivalent using manufacturer’s instructions.

- Use heavy-duty eyelet (closed end) terminal such as Molex 19221 – Strip insulation from 2AWG conductor to the length of the terminal barrel approximately as shown.
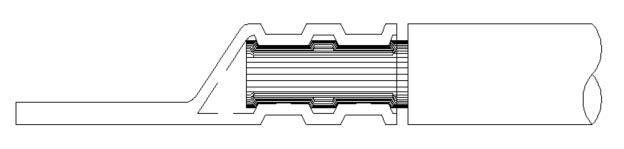
- Insert stripped end of 2 AWG conductor fully into barrel of heavy-duty eyelet (closed end) terminal, approximately as shown.
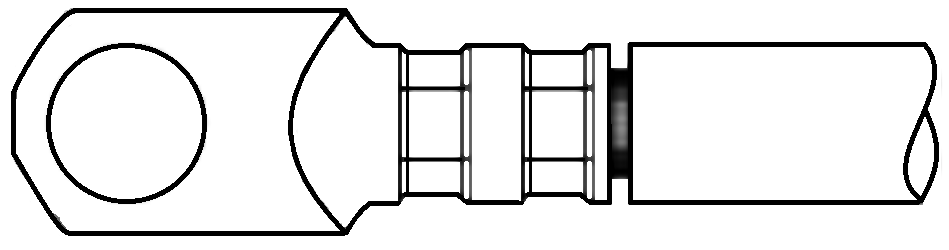
4. Crimp with quick cable 4245 cub crimp tool or equivalent, double
crimp, as shown.
- The resultant crimp(s) should fully enclose and confine the conductor strands from all sides and withstand an aggressive manual pull test.
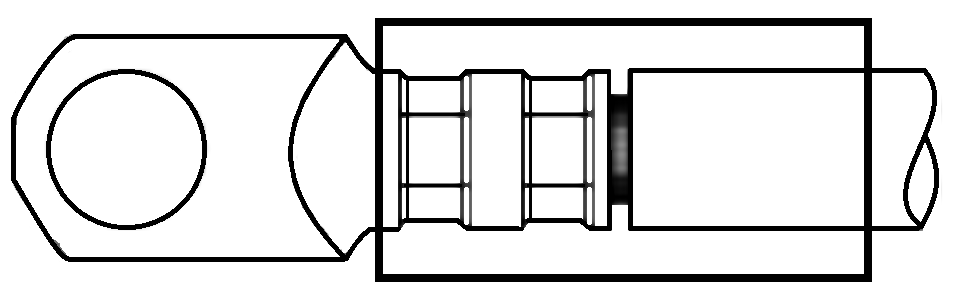
- Install approximately 1.5 in. (38 mm) of double wall (adhesive lined) heat shrink tubing over both the terminal barrel and the conductor insulation. Heat shrink in place until tubing conforms to barrel and conductor shape and adhesive seals the junction (See figure below).
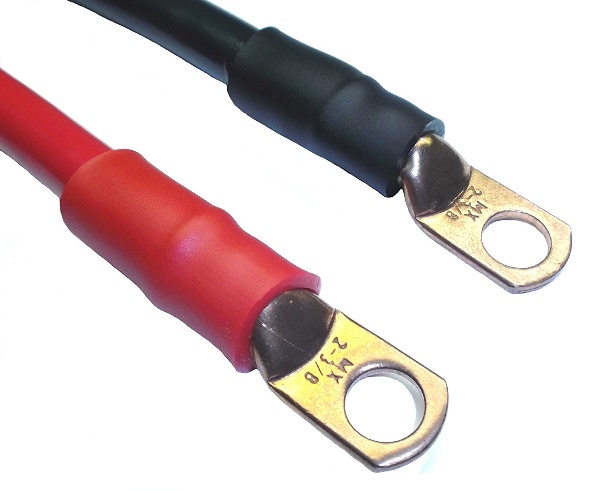
3.2.2 Seakeeper 4.5 Motor Power Connection
AC Input Power Source Requirements
- Either of two AC input voltages are acceptable:
- 110 – 120 VAC (nominal) (+/- 10%), 1 Phase, 50/60 Hz, 30 A
- 208 – 230 VAC (nominal) (+/- 10%), 1 Phase, 50/60 Hz, 20 A
- A separate circuit breaker should be used for each Seakeeper Drive Box in multiple Seakeeper installations.
AC Power Input Connection Instructions
AC Input Cable (3 X 10 AWG or 3X 0.6mm2 CSA), 10 ft (3 m) length, Seakeeper supplied pre-installed.
- Locate AC Input Cable for AC power input to the Drive Box.
ADD IMAGE IF DESIRED (SHOWING AC CABLE OUT OF SK 4.5)
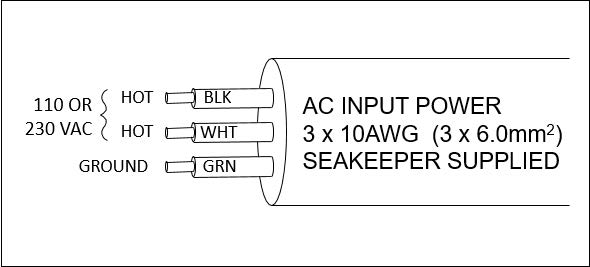
- Connect AC wires in to a 230 V, 20 A (or 110 V, 30 A), double-pole Circuit Breaker at an AC power distribution panel.
3.3 Control Power Connections
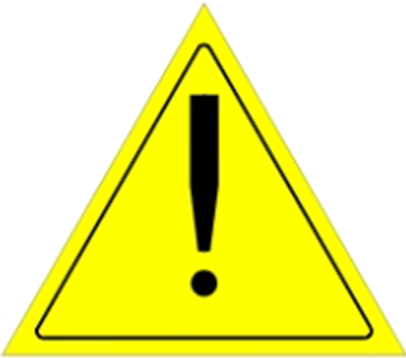
Reversing polarity on the DC power input to the Seakeeper can result in damage to electronics in the control system.
Low Current 12 V Power Source Requirements
- One 12 VDC, 15 A (Customer supplied) for Seakeeper Control Power.
- A dedicated breaker should be used for each 12 VDC load on the Seakeeper: one breaker for Control Power and one breaker for Seawater Pump power (Drawing No. 90696 and 90699).
- , A dedicated breaker should be used for each Seakeeper‘s Control and Seawater Pump power if multiple units installed.
12 VDC Control Power Connection
- Install Seakeeper provided DC Power Input Cable, P/N 20248 (Drawing No. 90696 and 90699).
- Route DC Power Input Cable to DC Power Distribution Panel.
- Terminate positive (B+, Red) conductor to +12 VDC.
- Terminate negative (B-, Black) conductor directly to battery negative or negative bus terminal.
- Before connecting DC Power Input Cable to Seakeeper wire harness, check for proper voltage and polarity with a multimeter using figure below.
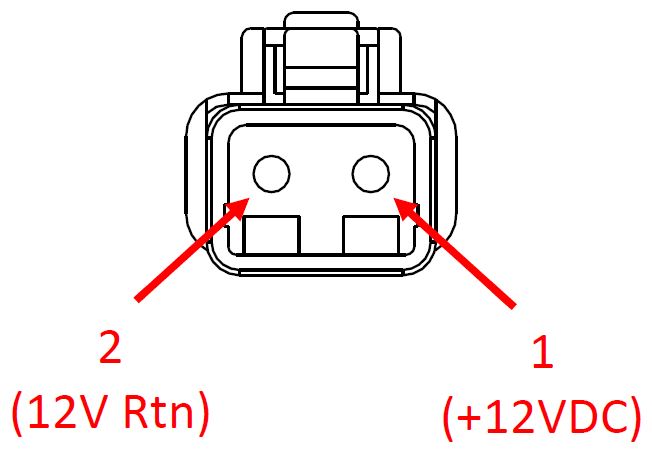
Contact Assignments (front)
- Connect control power cable to 12 VDC power input connector (labelled “INPUT POWER”) on the Seakeeper, Deutsch DTP04-2P connector.
3.4 Seawater Pump Power Connections
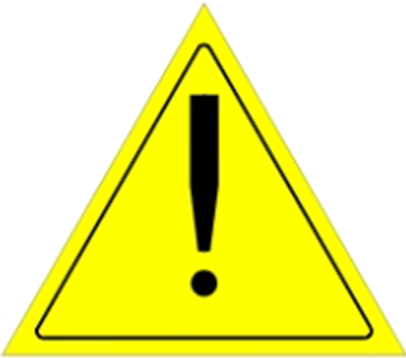
Reversing polarity on the DC power input to the Seakeeper can result in damage to electronics in the control system.
DC Seawater Pump Power Source Requirements
- One 12 VDC, 15 A (Customer supplied) for DC Seawater Pump.
- OPTIONAL: Seakeeper 4.5 may use one 24 VDC, 10 A (Customer supplied) source for the DC Seawater Pump.
- A dedicated breaker should be used for each 12 VDC load on the Seakeeper: one breaker for Control Power and one breaker for Seawater Pump power (Drawing No. 90696 and 90699).
- A dedicated breaker should be used for each Seakeeper‘s Control and Seawater Pump power if multiple units installed.
DC Seawater Pump Input Power Connection
- Install Seakeeper provided DC Seawater Pump Input Cable, P/N 30327 (as shown in Drawing No. 90696 and 90699).
- Route Seawater Pump Input Cable to DC Power Distribution Panel.
- Terminate 16 AWG positive (B+, Red) conductor through 12 VDC dedicated overcurrent protection device (customer supplied), maximum of 15 A, to dedicated battery isolation switch.
- 24 VDC, 10 max can be used for Seakeeper 4.5 Seawater Pump power.
- Terminate 16 AWG negative (B-, Black) conductor directly to battery negative terminal or DC main negative bus bar.
- Before connecting Seawater Pump Input Cable to Seakeeper wire harness (at “SW PUMP VDC IN”), check for proper voltage and polarity with a multimeter using figure below.
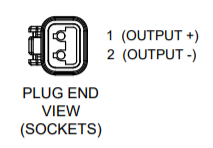
- Connect Seawater Pump Input Cable to “SEAWATER IN” connector on the Seakeeper wire harness Deutsch DT04-2P connector.
DC Seawater Pump Output Power Connection
- Connect Seawater Pump Output cable (P/N 20334) to the Seakeeper 4.5 “SW PUMP VDC OUT” connector.
- The Seawater Pump Output cable is a 2 X 16 AWG cable, 16 ft (5 m) length, with a size 16 female Deutsch plug.
- Pumps rated at 12 VDC, 15 A maximum (24 VDC, 10 A), customer-supplied, must be configured with a Deutsch DT series, 2-pin receptacle to mate with the connector shown in figure below.
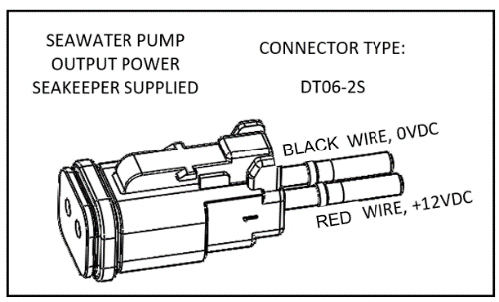
- The Seawater Pump Output cable must be routed and installed in the vessel from the Seakeeper “SEAWATER OUT” connector (male) to the DC seawater pump cable Deutsch connector (female).
- Connect Seawater Pump Output cable plug (female) to the customer-supplied receptacle (male). The recommended wiring is shown in figure below.
- Contact Seakeeper if desired to install customer-supplied relay on Seawater Pump Output cable to power Seawater Pump.
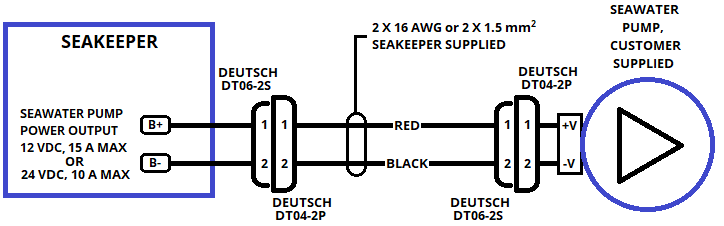
3.5 Electrical Equipment Ground Connections
- Connect the Seakeeper foundation ground to vessel ground as shown in figure.
- Install Ground Cable (10 AWG or 6.0 mm2, customer-supplied) from the M6 brass ground stud on the Seakeeper rear brace to a suitable vessel ground.
- EN/IEC 90204-1 Clauses 6.3.3 and 8.2.3
- ABYC E-11 July 2018 Clauses 11.5.2 and 11.16.1
NOTE: USE ONLY THIS LOCATION TO GROUND THE SEAKEEPER TO THE VESSEL GROUND.
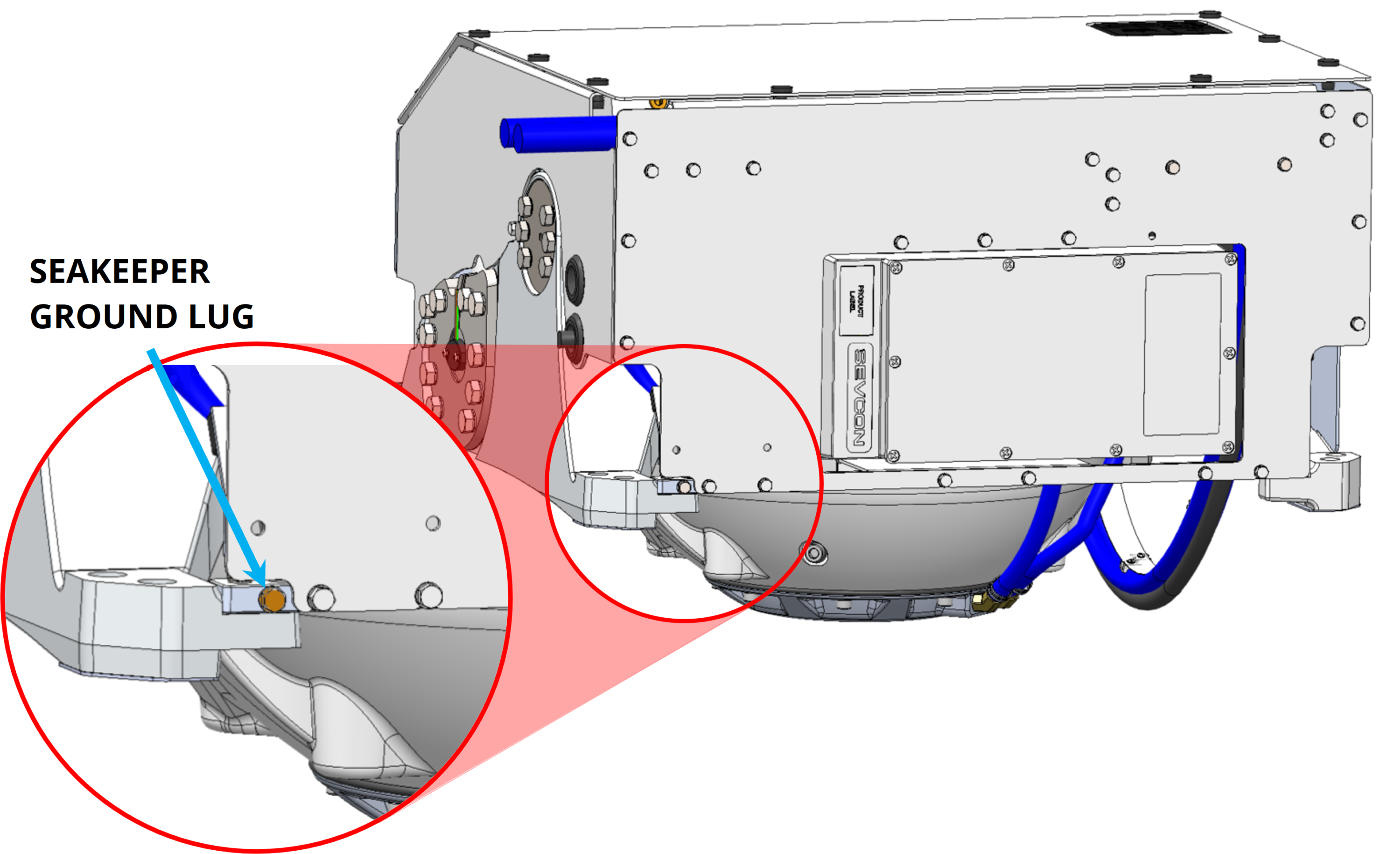
- Ground should be made with the vessel bonding system, if available. However, the ground is not referring specifically to a bonding system but for outboard boats generally refers to the outboard engine negative terminal. Per ABYC E-11 (2018), Clause 11.5.2.7.4: If the negative side of the DC system is to be connected to the ground, the connection shall be made only from the engine negative terminal, or its bus, to the DC grounding bus. This connection shall be used only as a means of maintaining the negative side of the circuit at ground potential and is not to carry current under normal operating conditions.
- A proper ground connection is critically important for corrosion protection and helps to ensure the ignition protection of the unit by ensuring it does not carry any stray current.
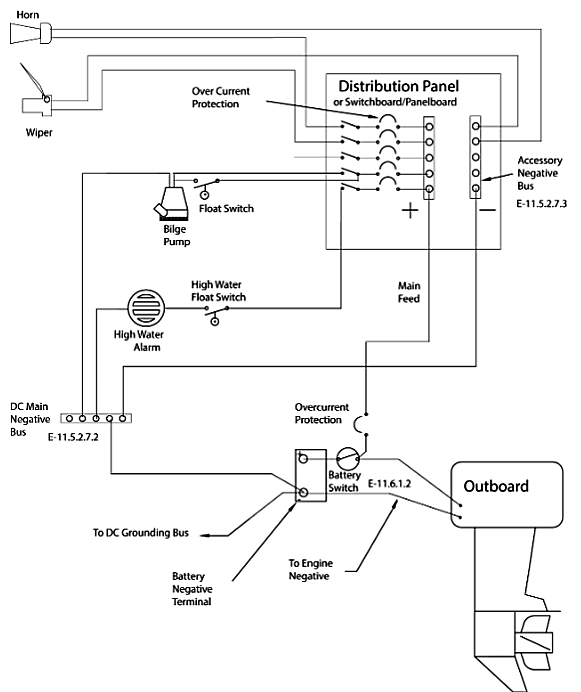
3.6 ConnectBox Connections
Reference Documents:
- 90696 – Seakeeper 4.5 Cable Block Diagram
- 90699 – Seakeeper 4 Cable Block Diagram
- Seakeeper MFD Compatibility Technical Bulletins:
- Optional 5″ Touch Display
Seakeeper 4 / 4.5 Display Options
A Seakeeper display is required with the installation of a Seakeeper 4 / 4.5 to support the full functionality of the unit through the Seakeeper App in addition to the ConnectBox. The Seakeeper App provides an interface for controlling the Seakeeper or viewing the Settings, Service, Info, and Alarm pages. The Seakeeper ConnectBox can be helm-mounted to provide an additional interface for the control of the Seakeeper but does not replace the need for a Seakeeper compatible display.
The Seakeeper 4 and 4.5 have two options for establishing a Seakeeper display interface to support the Seakeeper App:
- Connect the Seakeeper to a compatible Multifunction Display (MFD).
- Install an optional Seakeeper 5″ Touch Display (P/N 90600).
The following figure provides a schematic of the two display options. The subsequent sections outline the instructions and references for connecting the Seakeeper to each of these display options.
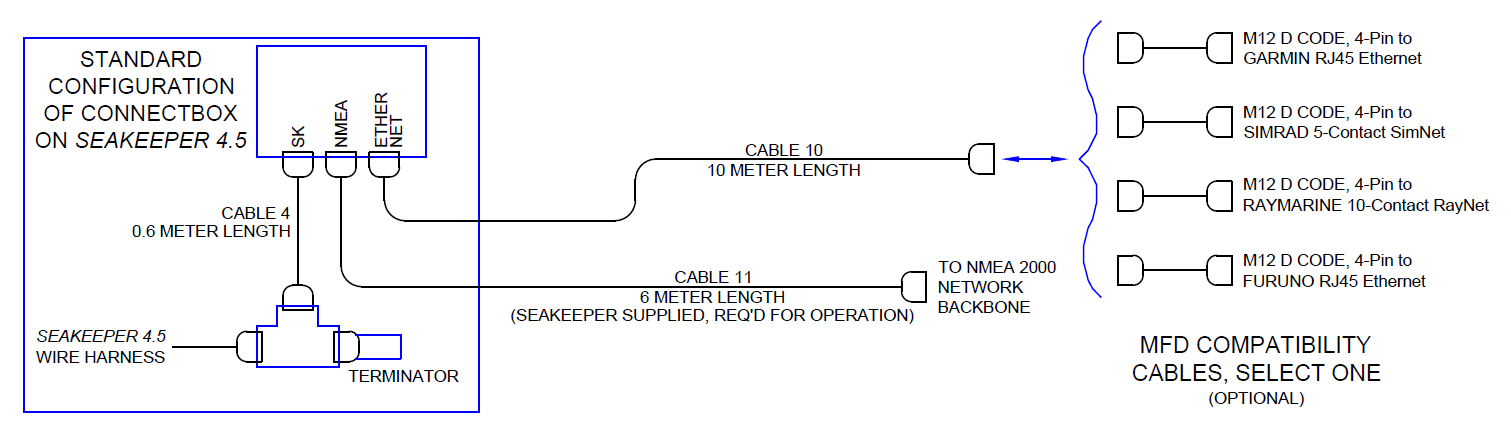
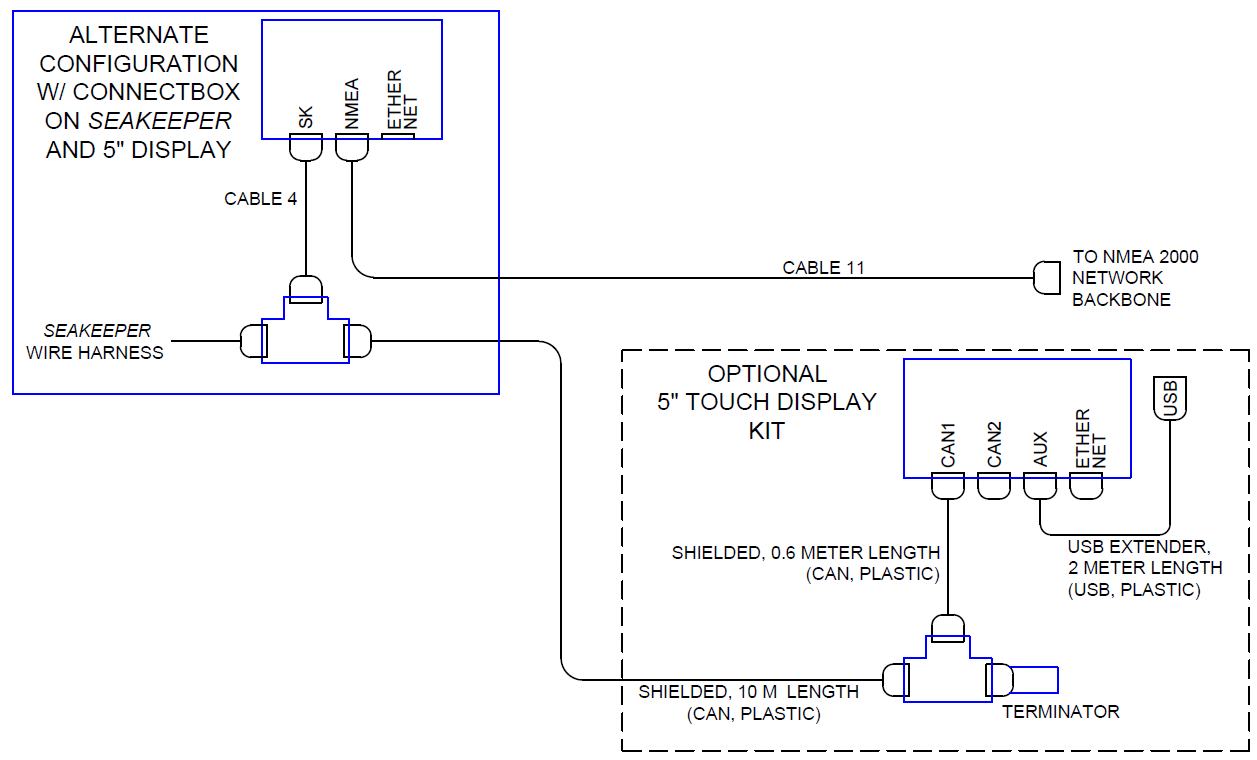
Connecting to a Compatible MFD
- The Seakeeper 4 / 4.5 can be connected to a variety of available MFD systems. Refer to the Technical Bulletins Section of the Seakeeper Technical Library for manufacturer specific MFD compatibility technical bulletins.
- MFD specific Technical Bulletins will be updated regularly as new MFD systems become compatible. Currently GARMIN, RAYMARINE, SIMRAD, and FURUNO offer compatible MFD models.
- Once a compatible MFD has been selected, refer to the appropriate manufacturer specific Technical Bulletin for integration instructions.
- Connect Seakeeper-supplied Ethernet adapter cable 10, D-Code 10 m cable to MFD manufacturer-specific Ethernet adapter cable. Custom Ethernet cables for specific MFD manufacturers are available through Seakeeper and must be purchased with the Seakeeper if connecting to an MFD.
Connecting to an Optional Seakeeper 5″ Touch Display
If not utilizing a compatible MFD display, a Seakeeper 5” Touch Display must be purchased from Seakeeper. The Seakeeper 5” Touch Display (P/N 90600) includes the components shown in the following figure and will be integrated with the ConnectBox.
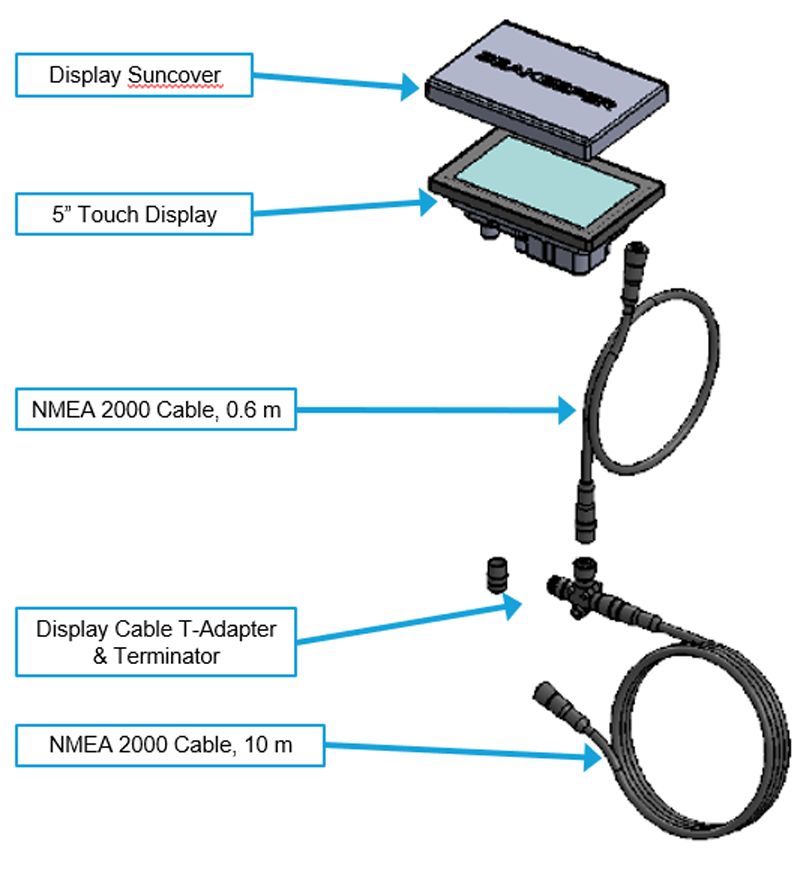
(P/N 90600)
- Determine location of Seakeeper 5” Touch Display:
- The desired location of the 5” Touch Display must be determined with respect tothe vessel’s arrangement.
- The 5” Touch Display should be located on or near the helm or another easily accessible location.
- Route CAN communications cable:
- The CAN Cable, (labelled NMEA 2000 Cable in figure), is a 10 m shielded cable that connects the ConnectBox Tee adapter to the 5” Touch Display.
- The NMEA 2000 cable must be routed and installed in the vessel from the Seakeeper wire harness CAN Tee to the Tee Adapter at the Seakeeper 5” Touch Display, included with P/N 90600.
- Install Seakeeper 5″ Touch Display equipment:
- Console space required: Approx. 5.24 W x 3.70 H in. (133 x 94 mm)
- Mounting Instructions, Surface Mount: see Envelope and Mounting Details, in Drawing No. 90438 – 5” Display Envelope and Mounting Details.
- CAN communications tee adapter and terminator mounting instructions:
- Console space required, Rear: Approx. 4 W x 3 H in. (102 x 76 mm)
- Mounting Instructions: Rear mount on vessel console panel, within 2 ft (0.6 m) of Display.
- Hardware required: One mounting screw for .197 in. (5 mm) diameter mounting hole on Tee Adapter.
- Connect Seakeeper 5” Touch Display Equipment:
- The Seakeeper 5” Touch Display is connected in accordance with the figure above.
NMEA 2000 Network Connection
The Seakeeper 4 / 4.5 requires a connection to the vessel’s NMEA 2000 network backbone. The Seakeeper will monitor information on the NMEA network to support and optimize the performance of the Seakeeper.
- Install customer-supplied NMEA 2000 Tee Adapter (space required: approximately 4 W X 3 H in. (102 X 76 mm).
- Connect NMEA Backbone to Tee Adapter.
- Connect Seakeeper-supplied NMEA CAN cable to the customer-supplied NMEA 2000 Tee Adapter on vessel’s NMEA 2000 backbone.
- An active NMEA 2000 compatible GPS signal is required on the vessel’s NMEA 2000 backbone to operate the Seakeeper.
- If no GPS signal is detected, a warning will be present on the Seakeeper app.
- An active NMEA 2000 compatible GPS signal is required on the vessel’s NMEA 2000 backbone to operate the Seakeeper.
ConnectBox Helm Mounting – Optional
- Console space required: Approx. 3.41 L x 4.15 W in. (87 x 106 mm).
- Mounting Instructions, Surface Mount: See Drawing No. 90558 – Seakeeper ConnectBox Helm Mounting Kit, for details. Seakeeper ConnectBox 3D Model available upon request.
- Mount ConnectBox Replacement Blank insert into Seakeeper 6 / 5 top cover at the original location of the ConnectBox.