Seakeeper 3 Operation Manual (90379-5) 3-232-4223 to Current
4.0 Power Failures, Alarms, and Troubleshooting
4.1 Power Failures and Alarms Introduction
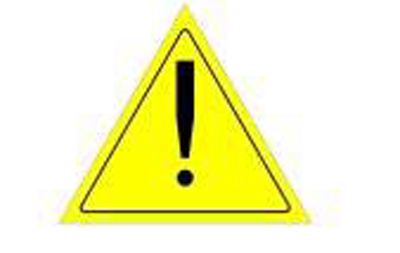
The operator should physically examine the Seakeeper following an alarm. Continuing to reset alarms without service intervention can result in damage or personnel injury.
__________________________________________________________
The Motor Connections should not be touched when the Seakeeper is Powered on, or the motor is running. This voltage hazard exists even if the flywheel is coasting down, and the supply voltage has been shut off.
__________________________________________________________
The flywheel must be at Zero (0) RPM and DC input power disconnected for at least 10 minutes prior to any service work on the Seakeeper.
The Seakeeper 3 has safety features, such as alarms and warnings, that pop-up on the Seakeeper
Application and are signaled on the ConnectBox to protect the Seakeeper as well as the vessel. The brake can be locked from the Application, ConnectBox or by shutting off DC power at the supply breakers, preventing the Seakeeper from precessing.
In the event of a power failure, the brake automatically locks the Seakeeper so it cannot generate anti-rolling torque loads. When a power failure occurs, it is important to identify the three sources of power to the Seakeeper 3:
- 12 VDC high current powers the Motor Drive.
- 12 VDC low current powers the Seakeeper control electronics, ConnectBox, and optional 5″ Touch Display.
- Seawater Pump 12 VDC input powers the seawater cooling pump.
These are supplied on cables which are shown on Drawing No. 90377 – Seakeeper 3 Cable Block Diagram.
Voltage-Related alarms include the following:
- DC INPUT VOLTAGE HIGH – Code 40
- Alarms when low current DC input voltage varies from a reasonable range for the design voltage.
- DC INPUT VOLTAGE LOW – Code 41
- Alarms when low current DC input voltage varies from a reasonable range for the design voltage.
- DC INPUT VOLTAGE LOW [SPEED LOSS DURING OPERATION] – Code 111
- DC INPUT VOLTAGE LOW [SLOW SPOOL UP] – Code 112
- Code 11 and 112 occur to adjust power consumption as voltage drops below 11.1 VDC to prevent battery depletion. If battery voltage drops to 10 VDC, code 167 will trigger.
- BATTERY STATE OF CHARGE – Code 123
- This alarm alerts the operator of a low state of charge (SoC) if the Seakeeper is receiving a SoC signal over the NMEA 2000 network and SoC based protection is enabled in the Battery Monitor Configuration. The SoC will depend on the cut-off threshold slider setting (see Section 3.3).
- The Battery icon on the Home screen will appear red and empty.
- HIGH CURRENT DC VOLTAGE LOW – Code 167
- HIGH CURRENT DC VOLTAGE HIGH – Code 168
- This alarm protects the Seakeeper 3 from an over-voltage of 16 VDC or higher.
4.2 12 VDC High Current Failure
If the 12 VDC high current is disconnected during operation, a notification screen will indicate “High Current DC Voltage Low”. If the failure is not corrected within two minutes, a “High Current DC Voltage Low” alarm will occur. The brake will lock.
- Verify the boat’s circuit breaker or fuse supplying +12 VDC high current has not tripped or blown.
- When +12 VDC high current is restored, operation may be restored.
- Press Power On/Off button
. The progress bar will appear and indicate flywheel speed. When the flywheel is at minimum operating speed, the Stabilize button will appear so stabilization can be turned on. This may take up to 30 minutes, depending on the speed of the flywheel when the +12 VDC high current is restored.
4.3 12 VDC Failure
12VDC Low Current
If the 12 VDC low current is disconnected during operation, the display will be blank, flywheel speed will decrease, and the Seakeeper will be turned off (no stabilization).
- Verify the boat’s circuit breaker or fuse supplying +12 VDC low current has not tripped or blown.
- When +12 VDC low current is restored, the display will power up, the Splash Screen will appear, and then the Home Screen will appear.
- Press Power On/Off button
. The progress bar will appear and indicate flywheel speed. When the flywheel is at minimum operating speed, the Stabilize button will appear so stabilization can be turned on. This may take up to 30 minutes, depending on the speed of the flywheel when the +12 VDC low current is turned back on.
SW Pump Power
If Seawater Pump input 12 VDC power is disconnected during operation, the Seawater Pump will fail to provide cooling seawater flow when required. The resulting high temperatures would result in the Seakeeper being turned off (no stabilization) due to high temperature alarm(s).
- Verify the boat’s circuit breaker or fuse supplying +12 VDC SW Pump power has not tripped or blown.
- When +12 VDC SW Pump power is restored, reset any alarm and continue Seakeeper operation.
4.4 Alarms and Troubleshooting
Alarms
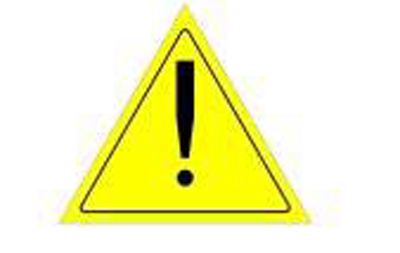
The operator should physically examine the Seakeeper following an alarm. Continuing to reset alarms without service intervention can result in damage or personnel injury.
Sensors, alarms, and shutdowns are provided to allow unattended operation. Sensors measure drive temperatures, gimbal angle, brake pressure, and vessel motion. The Seakeeper controller sends sensor values and alarm information to the display and locks the brake and shuts down the motor drive in the event of an alarm condition. Seakeeper operating history during faults or alarms is recorded in the controller’s memory for subsequent recall if service is needed. Seakeeper and Seakeeper Dealers may access the Seakeeper’s software to gather run hours, bearing loading, and hull slamming information.
NOTE: Only the Seakeeper 5” Touch Display or the MFD can identify and address the alarm. The alarm will not clear until the operator presses the Reset Alarm button, AND the alarm condition is no longer present. The operator can then press the POWER button again to resume Seakeeper operation.
- A view of a typical Alarm screen.
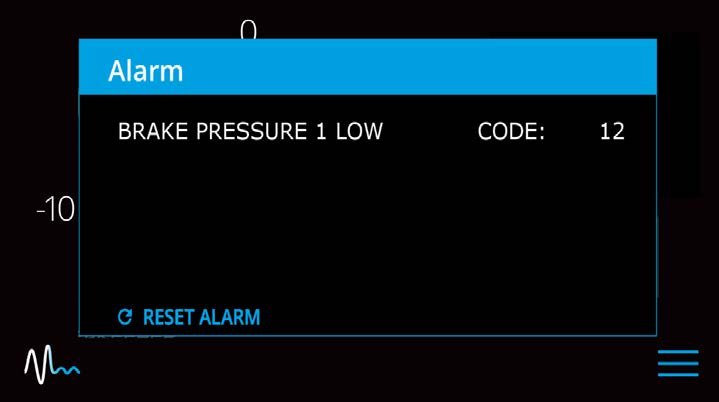
- To reset the alarm, press the Reset Alarm button:
Troubleshooting
- At MFD app or 5″ Touch Display, check for alarms or warnings.
- Power Supply: Check electrical power source breakers ON or fuses installed and NOT blown.
- Mechanical Components:
- For temperature -related alarm, verify the coolant reservoir is filled with glycol mixture (50% ethylene glycol/50% distilled water). Verify seawater pump power aligned.
- Visually check mechanical fittings and joints for leakage.
- Visually check coolant and brake hoses for chaffing and leakage.
- Contact an authorized Seakeeper dealer for further assistance in diagnosing and resolving complex alarms.
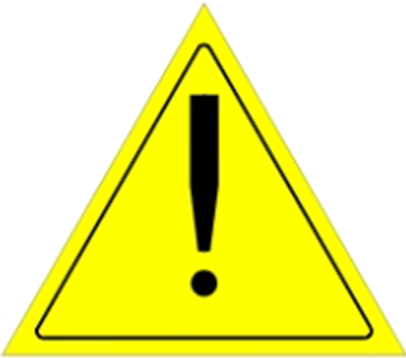
If a GPS signal is lost, a warning message will appear in the Alarm History and a message will appear on the Home Screen, as seen below. The Seakeeper will not spool down, however the precession rate and angle of the sphere will be reduced until GPS signal returns.
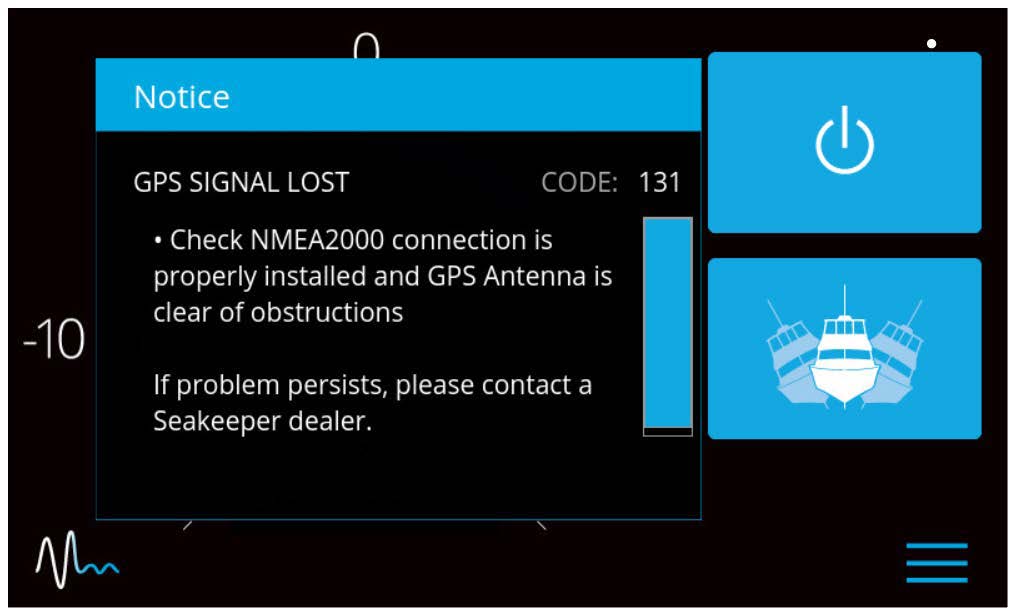
4.5 Alarm History
The ALARM HISTORY page on the Seakeeper application shows the recent alarms and warnings. Alarms trigger a pop-up message to be displayed on the display or Seakeeper App. Warnings will be listed in the alarm history but do not affect Seakeeper operation. The alarms and warnings are in chronological order starting with the most recent. Warnings included in the history page are for issues that do not affect gyro operation.
Press the Menu button to show the page options and then the ALARM button
to show alarm history.
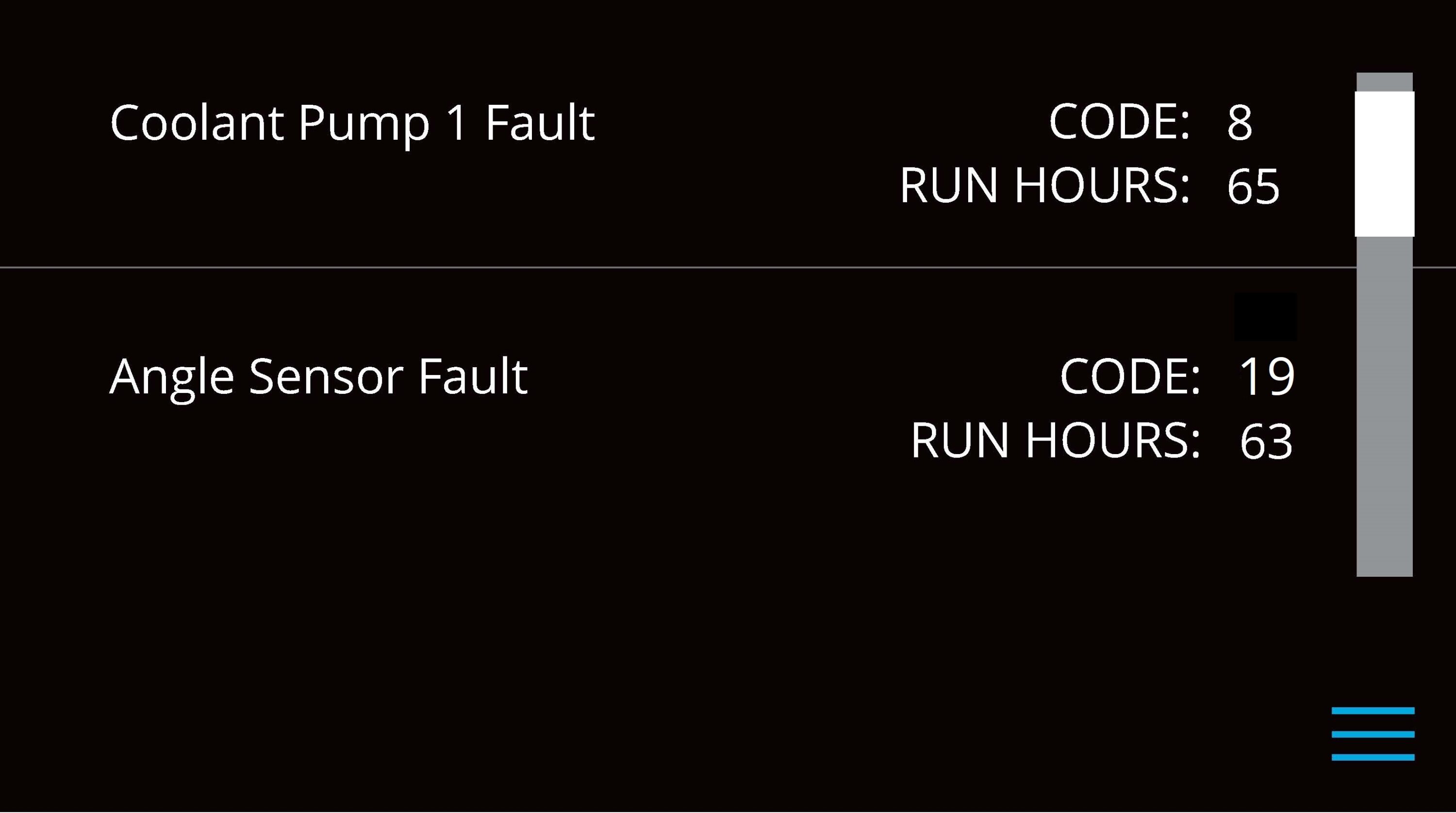