Seakeeper 10 Installation Manual (90841-1)
2.0 Mechanical Installation
2.1 Mechanical Installation Introduction
The Seakeeper 10 is capable of producing loads up to 5,274 lbs (23.46 kN) at each of the four mounts. These forces should be considered to be acting simultaneously, fully reversing, and will repeat an infinite number of times. Careful consideration should be given to foundation design to ensure it is capable of transferring these loads into the hull. These loads do NOT include vessel motion accelerations, such as vertical slam loads which can be high for higher speed vessels. The responsible party for designing the supporting structure (boat builder, installer, or hired sub-contractor) must accommodate the above forces plus a reasonable factor of safety. Seakeeper recommends a minimum safety factor of 3.0 (yielding a Safety Margin of 2.0).
It is assumed that the installer is familiar with installing mechanical fasteners in marine structures or using high strength adhesives on aluminum and fiberglass (FRP), and has performed structural analysis to assure the structure to which the Seakeeper mounts can properly transfer the loads the Seakeeper creates into the hull structure. If the installer has any doubt about the ability of the structure to transfer the loads to the hull, then a licensed naval architect or marine engineer should be contacted to perform a structural analysis.
The installer should review the following list of reference drawings to ensure the installation procedure is fully understood.
Reference Documents & Drawings:
2.2 Selection of Installation Location
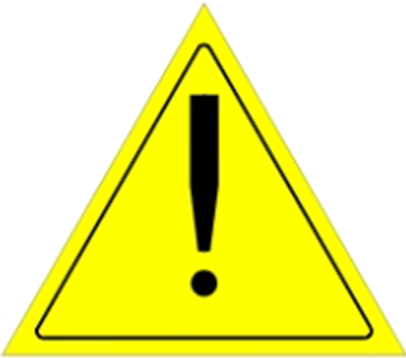
The Seakeeper should be installed aft of amidships to minimize high acceleration loadings due to hull/wave impacts during operation at high speed or in large waves. If the only possible Seakeeper location is forward of amidships then the installer should have Seakeeper review the installation location prior to finalizing the design.
Seakeeper can only assess installation location regarding its impact on Seakeeper operation and serviceability. Seakeeper cannot determine how the installation location will affect the vessel static or directional stability other than cyclic roll reduction. The Installer is responsible for considering the Seakeeper’s effect on the Center of Gravity location, trim, overall stability, and performance of the vessel.
The Installer is solely responsible for ensuring that the Seakeeper is properly located and installed on the vessel foundation with an adequate margin of safety for the specified design loads and vessel operating characteristics.
Selection of mounting location of the Seakeeper should consider the following desirable features:
- Adequate service access for scheduled maintenances and overhaul of the Seakeeper 10 is required. See Figure 4 and Drawing No. 90831 – Seakeeper 10 Bolt-In Installation Details for service clearance requirements.
- The Seakeeper should be installed in a dry space to minimize effects of corrosion.
- The minimum service clearances shown are based on the size of serviceable components and tools required for removal and replacement of these components including field replaceable bearings. The clearances do not consider how the technician will be positioned for access to these areas. Access for a technician must be considered by the installer .
- The clearance and access requirements do not need to be permanent and can be provided via hatches, removable panels, or other temporary means where applicable.
- The installer/designer should consider all these factors for serviceability when defining the installation arrangement.
- Top down access must be incorporated into installation design to allow for adequate regular maintenance, service, and repair.
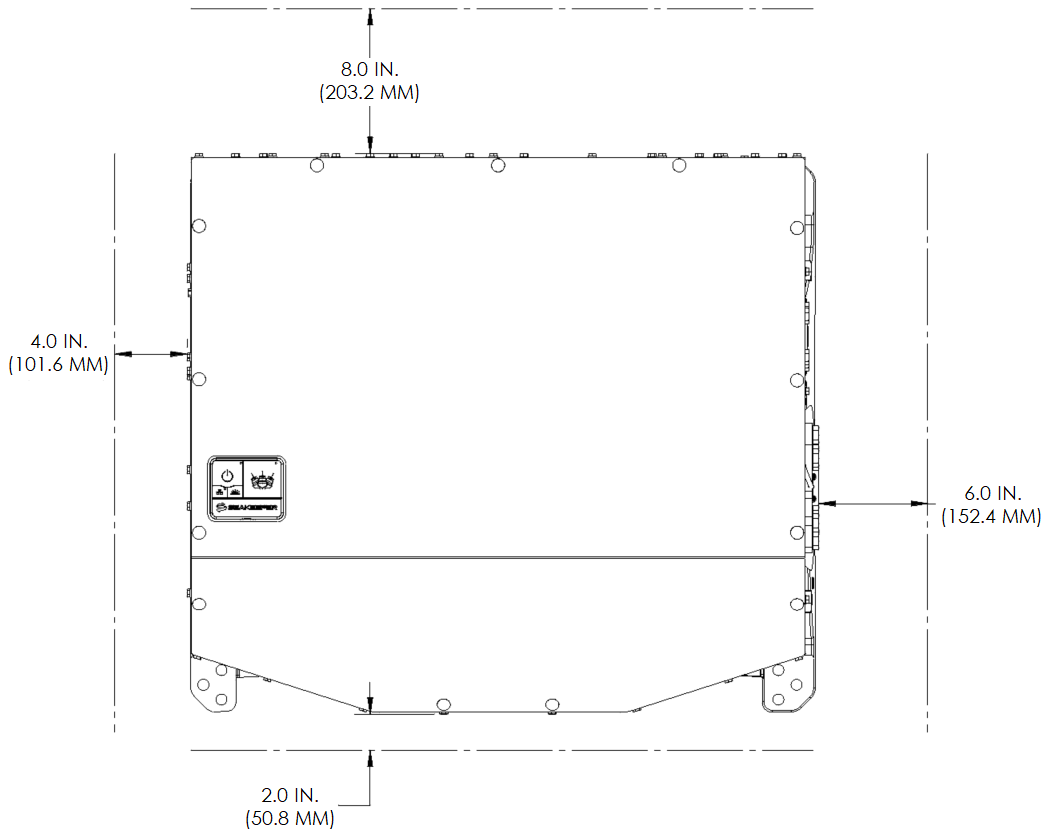
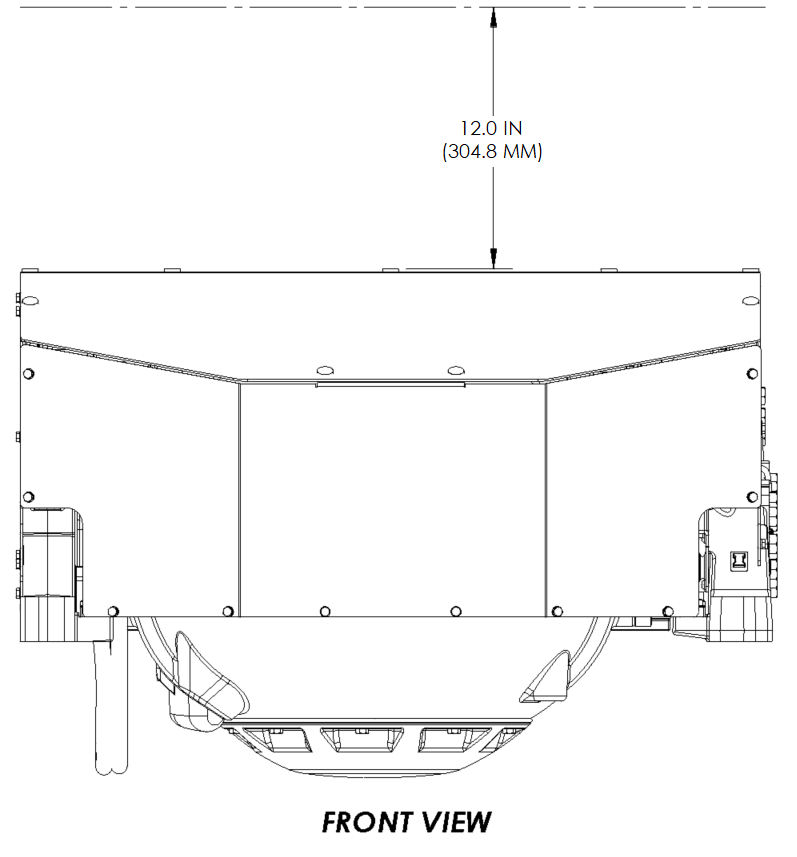
VIEWS SHOWING RECOMMENDED CLEARANCES AROUND THE SEAKEEPER FOR USE OF HANDTOOLS, EASE OF MAINTENANCE, INSTALLATION, AND PROPER OPERATION.
Figure 3 – Seakeeper 10 Installed Clearance Considerations
2.2.1 Overhead and Service Clearance Considerations
Access above the Seakeeper 10 must be considered for maintenance and service space. Figure 4 shows space considerations around and above Seakeepers installed below deck surface.
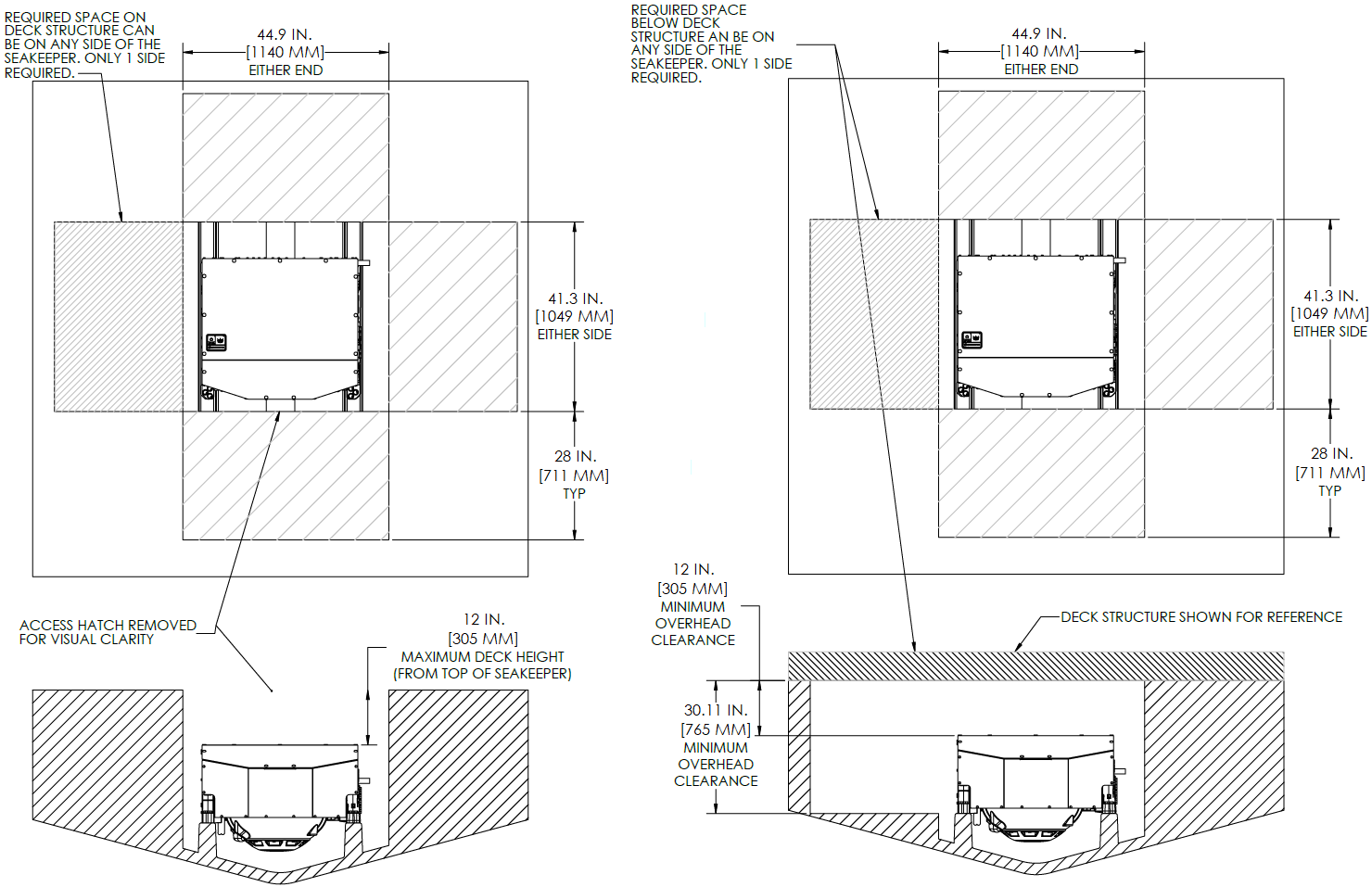
2.2.2 Noise/Soundproofing
Seakeeper 10 noise has been measured under steady state conditions (no wave load) in Seakeeper‘s Engineering Lab. The steady state noise is typically <72 dCB at 1 meter. As the frequencies emitting the highest sound pressures are low (like other marine machinery), it is recommended that the Seakeeper be installed in an enclosed space such as a machinery space, lazarette, or bilge. If additional noise reduction is needed, sound proofing insulation can be used in the space around the Seakeeper unit.
2.3 Bolt-In Installation
2.3.1 Preparation of Vessel Structure
Seakeeper provided mounting hardware is intended to apply to typical installation arrangements. However, each installation, especially custom aftermarket foundations, should be thoroughly reviewed to ensure the provided hardware meets the required thread engagement for the Seakeeper unit being installed. The mounting bolt thread engagement requirements are outlined in the Installation Manuals and Installation Details Drawings for each Seakeeper model. This also applies to Seakeeper model adapter kits and OEM built frames where the bolt hole depth should be checked to ensure the bolts will not bottom, preventing the bolts from achieving the intended preload.
When the Seakeeper provided hardware is not appropriate, the bolt specification (diameter and thread pitch) and grade should be matched in the required length and used with the Seakeeper provided washers. Mounting bolts should always be torqued to the Seakeeper specification. All Seakeeper provided bolts are metric course thread. Hardware specifications are also listed in the Installation Manuals and Installation Details Drawings.
Refer to Seakeeper Drawing No. 90834 – Seakeeper 10 Bolt-In Installation Details. Important dimensional and load information is given in this drawing that will impact the design details of the structure that will receive the Seakeeper. It is assumed that a proper structural analysis has been performed for the hull structure to which the Seakeeper will be fastened to ensure proper strength margins for the loads the Seakeeper will create during operation. Seakeeper recommends a safety factor of 3.0.
Marine-grade aluminum (6061-T6, or equivalent) bar stock is recommended for both blind hole tapping and thru-bolt installations. For blind-hold installations, helical threaded inserts (Helicoils) with a length of 1.5 x bolt-diameter (21 mm) are required to ensure the strength of the tapped holes exceeds that of the mounting bolts (Grade 10.9), which ensures a secure bolted connection between the Seakeeper and hull structure.
The Seakeeper supporting structure should be parallel to the vessel waterline, with up to 2 degrees of allowance for trim. It must be installed in a fore- and aft orientation parallel to the vessel centerline.
In addition, the four areas on top of the structure on which the Seakeeper frame and isolation gaskets will rest need to be co-planar within .06 in. (1.5 mm) to minimize potential distortion of the Seakeeper support frame when installed. The isolation gaskets are only used when the Seakeeper 10 is mounted to a dissimilar metal structure.
Seakeeper provides an installation template kit, P/N 90839, which contains plates matching the mating surfaces of the four feet on the Seakeeper’s frame. These plates have 4 holes located at the same centers as the mounting holes on the Seakeeper. The fixture locates the hole patterns at the proper spacing both in the forward-aft direction and the port-starboard direction. See Figure 6 below. Once assembled, the fixture can be used to check clearances and alignment of the hull structure.
Note: Do NOT use the installation fixture to establish Seakeeper envelope dimensions. Refer to Drawing No. 90834 – Seakeeper 10 Bolt-In Installation Details, for envelope dimensions. A 3-D model of the Seakeeper is available on the Seakeeper Technical Library (www.seakeeper.com/technical-library/) to aid in designing the Seakeeper foundation and the space around the Seakeeper.
NOTE: MAKE SURE NO OBSTRUCTIONS FROM THE HULL STRUCTURE CAN BE SEEN WITHIN THE INSIDE OF THE INSTALLATION TEMPLATE KIT (INSIDE THE MARKED RED LINES) AS SEEN IN FIGURE 6. REFERENCE SEAKEEPER DRAWING NO. 90834 – SEAKEEPER 10 BOLT-IN INSTALLATION DETAILS.
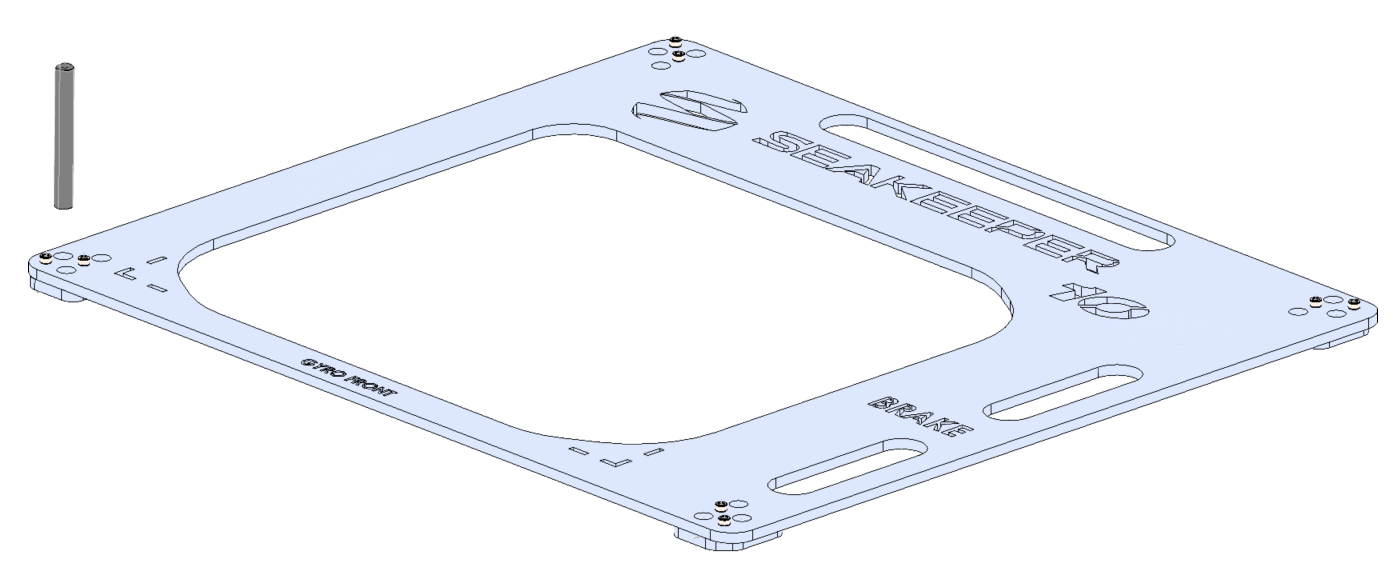
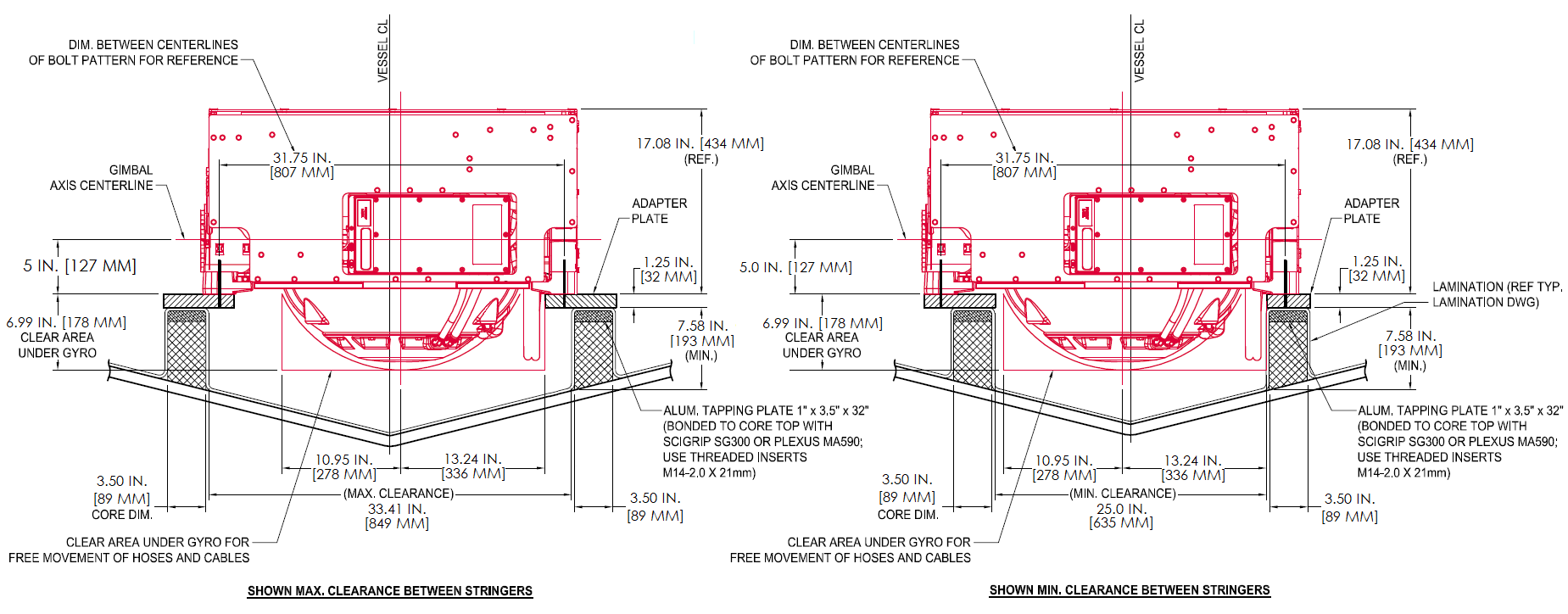
CAUTION: Tight clearances from cable guide bands to hull structure.
See above figure for dimensions and reference Seakeeper Drawing No. 90834 – Seakeeper 10 Bolt-In Installation Details for complete Seakeeper 10 envelope.
2.3.2 Transfer of Holes to Boat Structure
- Lower assembled fixture onto hull structure, see Figure 8.
- The four areas where the feet of the Seakeeper will rest should be coplanar to within .06 in. (1.5mm). See figure below.
- Align fixture in desired location and transfer holes from fixture plate to the hull structure by transfer punch. Note: Holes in fixture plate are ø 0.55 in. (14 mm).
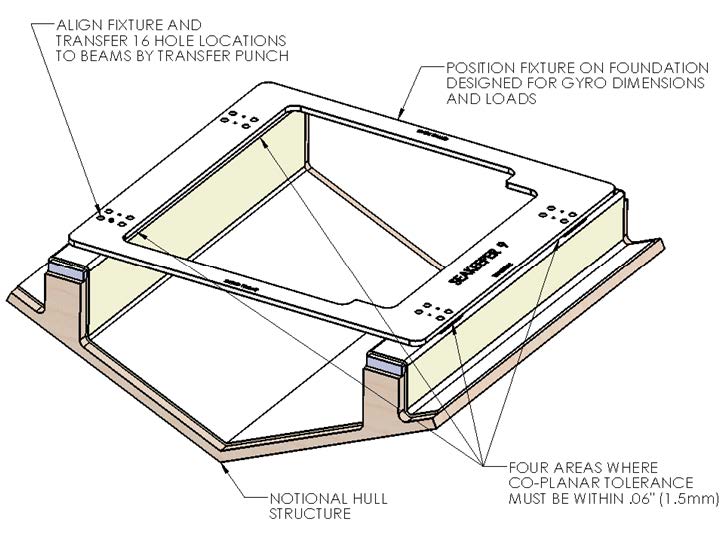
2.3.3 Bolt-in Installation
Blind-Hole Instructions
- Remove the Template Fixture and drill TWELVE (12) 0.571 in. ø (14.5 mm ø) holes perpendicular to the vessel structure to a minimum depth of 0.84 in. (21 mm). Take special care to drill perpendicular to the mounting surface.
- Tap drilled holes for M14-2.0 threaded inserts.
- Install twelve (12) M14-2.0 x 1.5 D (21 mm length) locking threaded inserts into holes in the hull structure at drilled and tapped locations using the threaded insert manufacturer’s installation tool.
- Remove the threaded insert prong/tang after the threaded inserts have been installed.
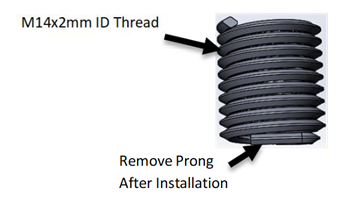
Through-bolt Instructions
Remove the Template Fixture and drill twelve (12) 0.59 IN. (15 mm) ø perpendicular to the vessel structure. Take special care to drill perpendicular to the mounting surface. A drill guide is recommended.
2.3.4 Installation of Seakeeper
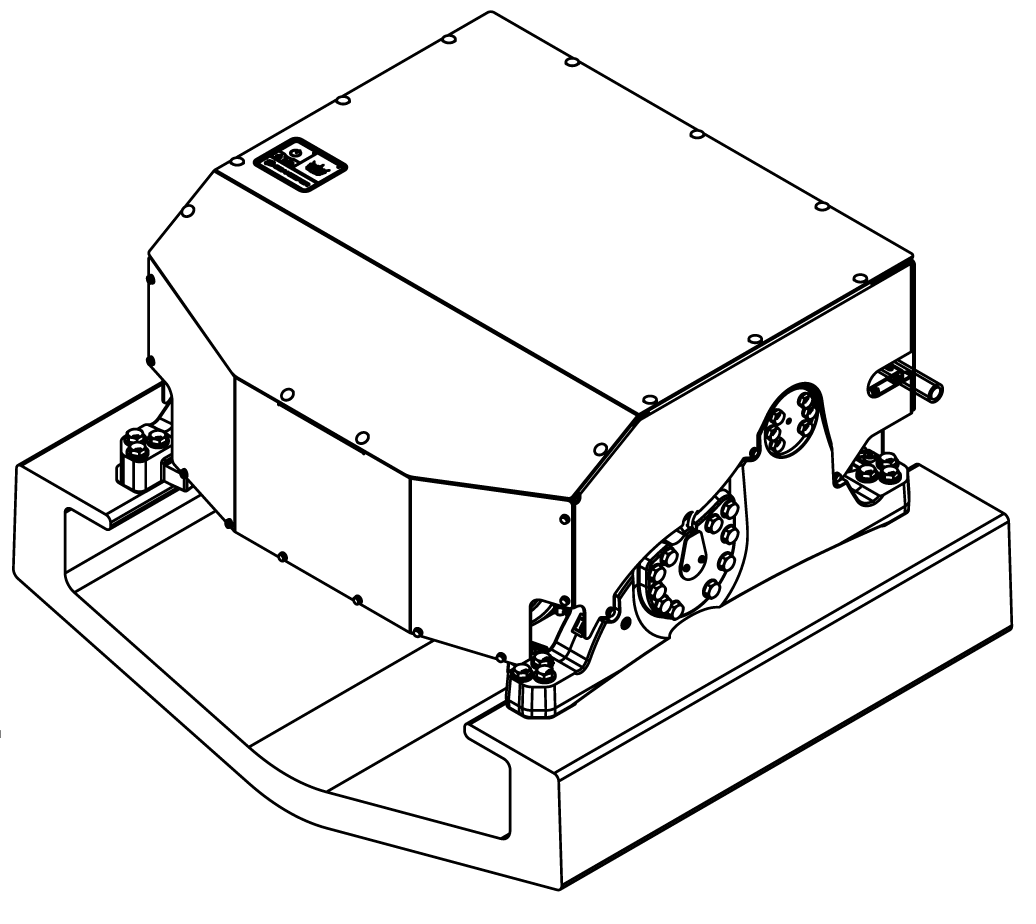
- Lower Seakeeper into position onto the hull foundation beams and align over drilled holes. Apply a small bead of marine sealant (e.g., SILI-THANE 803 or equivalent) between mating surfaces of Seakeeper frame and hull structure to prevent moisture wicking into bolt holes.
- For dissimilar metal foundations, locate and position the 4 isolation gaskets (P/N 13550) onto foundation beams and apply a small bead of marine sealant (e.g., SILI-THANE 803 or equivalent) between both mating surfaces of each isolation gasket where it contacts the beam and Seakeeper.
- Install Mounting Bolts, as shown in Figure 10:
- For Blind-Hole installations (P/N 90837 – Seakeeper 10 Bolt-In Installation Kit), install the Seakeeper supplied Grade 10.9, M14-2.0 x 85 mm fasteners or alternative Grade 10.9, M14-2.0 bolts to maintain a minimum thread engagement of 0.83 in. (21 mm). Apply a moderate coat of nickel-based anti-seize (e.g., SAF-T-EZE nickel-based anti-seize, SBT-4N or equivalent) to the threads of each bolt and include a small bead of marine grade sealant (e.g., SILI-THANE 803 or equivalent) under each bolt head and washer before installation.
- For Through-Bolt Installations (P/N 90838 – Seakeeper 10 Through-Bolt Installation Kit), install the Seakeeper supplied Grade 10.9, M14-2.0 x 100 mm fasteners or alternative Grade 10.9, M14-2.0 bolts to maintain a minimum of 2 threads protruding past nut. Apply a moderate coat of nickel-based anti-seize (e.g., SAF-T-EZE nickel-based anti-seize, SBT-4N or equivalent) to the threads of each bolt and include a small bead of marine grade sealant (e.g., SILI-THANE 803 or equivalent) under each bolt head and washer before installation.
- Torque all fasteners to 135 ft-lbs (183 N-m).
- New bolts, matching the Seakeeper specification, must be used for each installation and reinstallation that meet the requirements listed above.
- Proceed to electrical and cooling portion of the installation.
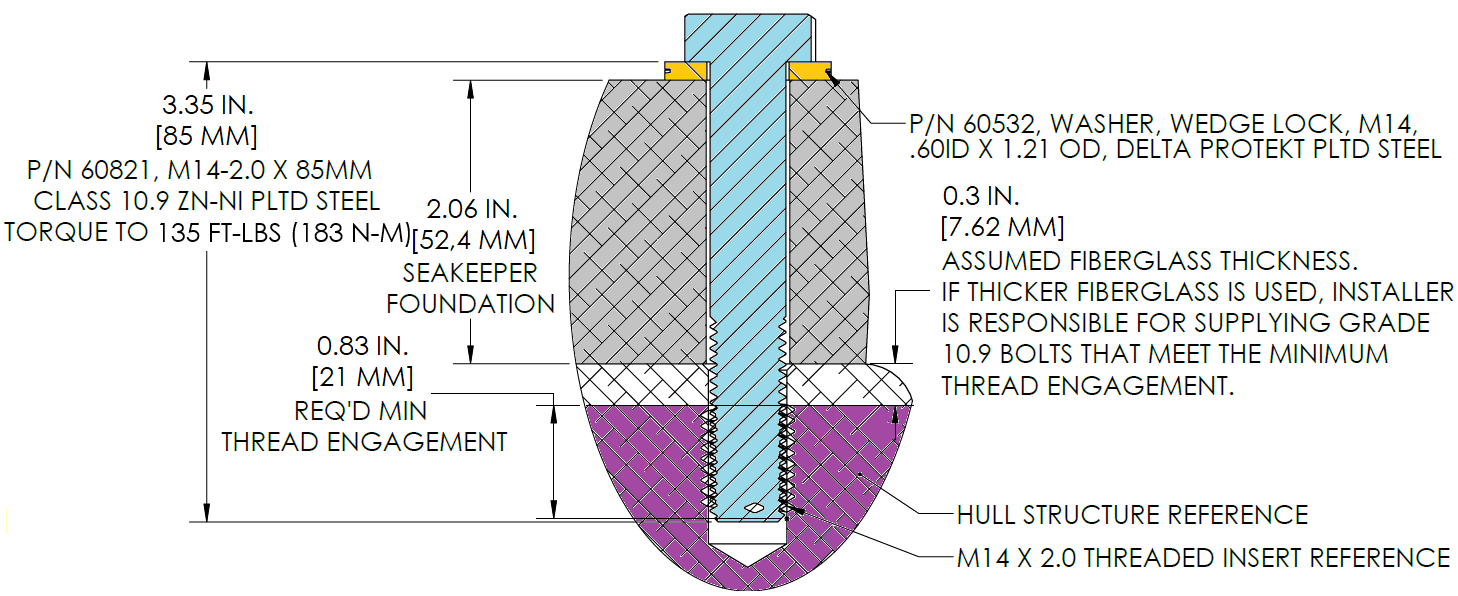
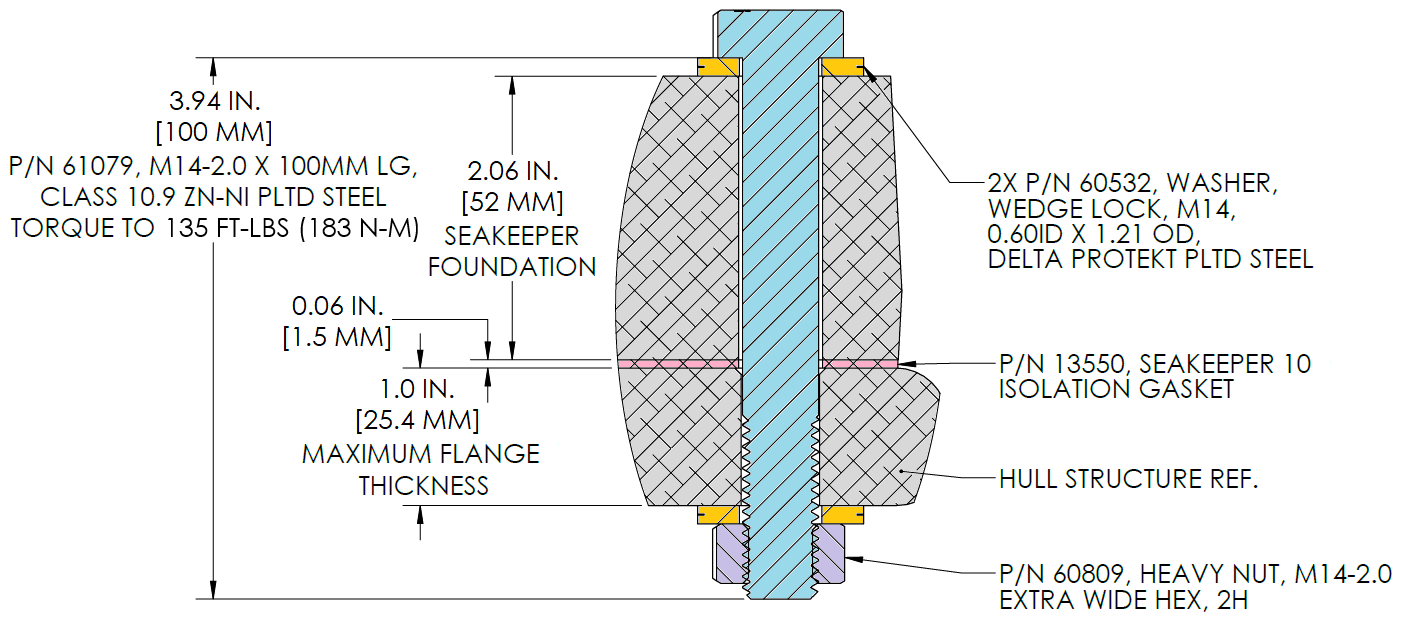