Seakeeper 1 Installation Manual (90519-2) 1-233-0631 to Current
Seakeeper 1 Installation Manual (90519-2) 1-233-0631 to Current
1.0 Introduction
Seakeeper 1
Installation Manual
90519, Rev 2
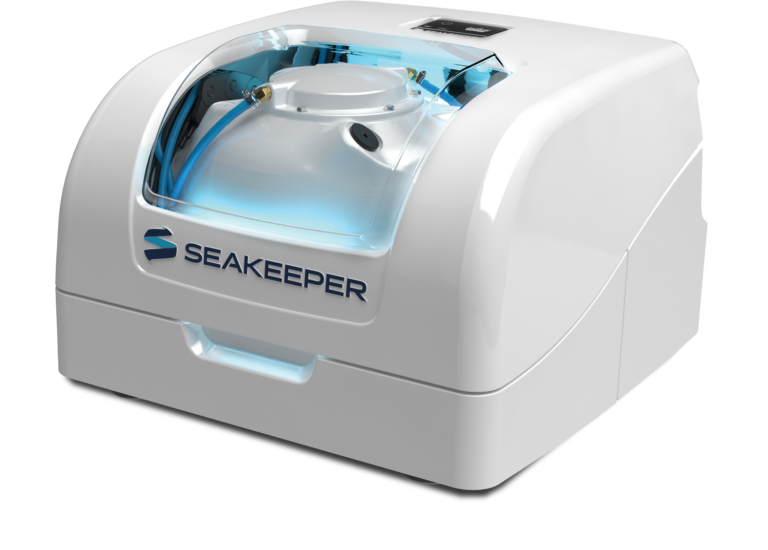
This document is intended to give details and guidance for a boat builder or equipment installer to properly install the Seakeeper 1 (applicable to serial numbers 1-233-0631 to current).
Reference Documents:
Precautions
- The Seakeeper must only be lifted from the supplied lifting eyes (see Section: Transport and Unpacking).
- Precision bearings support the Seakeeper flywheel. While unpacking and lifting the Seakeeper assembly, DO NOT drop or impart mechanical shock, as this could damage the bearings.
- While handling or installing the Seakeeper assembly, protect exposed hydraulic brake cylinder rods (see Figure 1) from scratches or damage, as this could lead to premature seal failure and oil leaks.
- Exercise care to protect any exposed surfaces, as damage to the finish could lead to the Seakeeper‘s early appearance degradation.
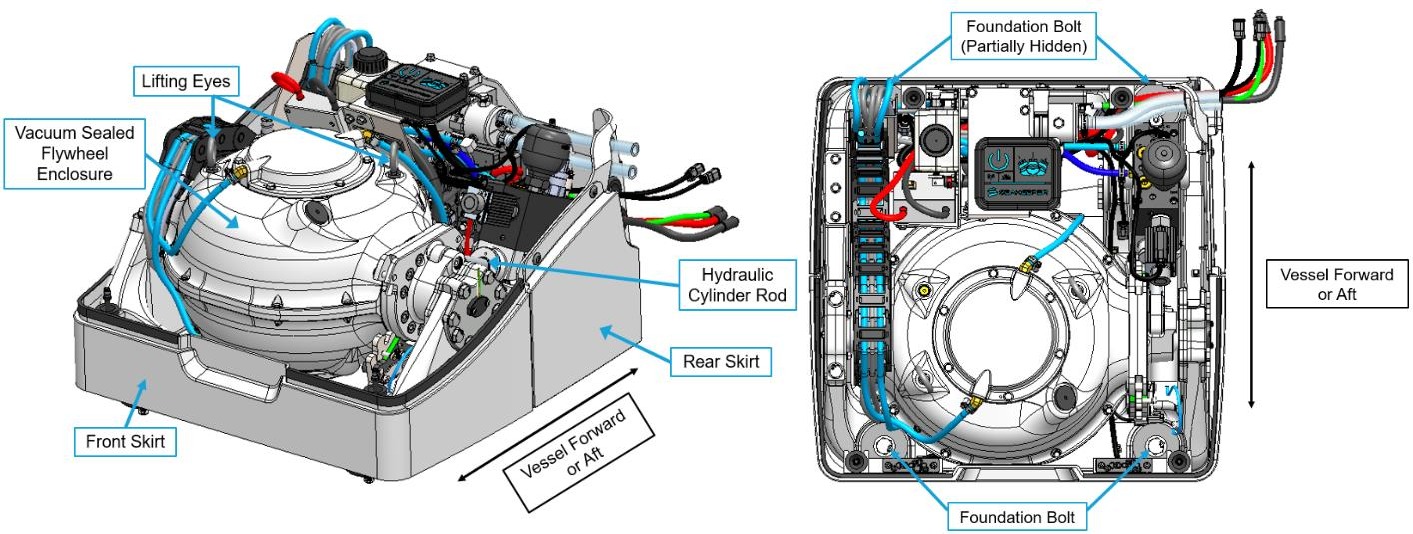
Safety
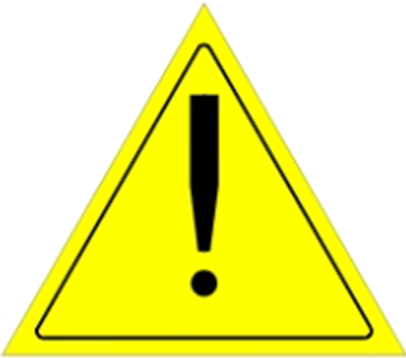
There is a large torque about the gimbal axis when the Seakeeper is precessing. Seakeeper cover panels are provided to prevent personnel or equipment from contacting the Seakeeper while it is in operation. These covers should not be stepped on or have anything placed on top. The covers should always be in place during operation.
_________________________________________________________________________________________
If it is ever necessary to access the Seakeeper while the flywheel is spinning, the Seakeeper must be locked at the display to stop the Seakeeper from precessing.
_________________________________________________________________________________________
Stand clear of the Seakeeper and all moving components during operation.
_________________________________________________________________________________________
Unit may be started remotely. Assume it could move without warning.
_________________________________________________________________________________________
The following must be true before accessing the Seakeeper:
• Input power must be disconnected for at least 10 minutes
• Seakeeper must be locked
• Flywheel must be at zero speed
Transport and Unpacking
Reference Documents:
- 90515 – Seakeeper 1 Unpacking Instructions
- 90510 – Seakeeper 1 Hardware Scope of Supply
- 11766 – DC Seakeeper Lifting Bar Kit
Transport
- Use a Seakeeper-provided shipping crate for transport, P/N 12098. The overall dimensions of a fully-packed Seakeeper 1 crate are 27.5 L x 27.5 W x 23.25 H in. (0.70 L x 0.70 W x 0.60 H m) with a weight of 430 lbs (195 kg), including accessories.
- Seakeeper 1 crates can be stacked up to two (2) units high. Only like units should be stacked, i.e., Seakeeper 1 on top of a Seakeeper 1
- Both air and ground transport are acceptable and available through Seakeeper.
- Seakeeper shipping crates must be transported in environmental conditions between -4°F and 140°F (-20°C and 60°C).
Unpacking
Reference Drawing No. 90515 – Seakeeper 1 Crate Unpacking Instructions for detailed unpacking instructions. Once the Seakeeper 1 crate has been unpacked, follow these instructions when lifting the unit:
- Remove and set aside cover, electrical components, cables, and miscellaneous items.
- Attach the Small Gyro Lifting Bar Kit, P/N 11766, to the two lifting eyes on top of the Seakeeper enclosure.
- Stay clear of the Seakeeper 1 when it is being lifted, and follow safe practices for working under a suspended load. The Seakeeper 1 weighs 365 lbs (165 kg).
- Figure 2 shows the proper lifting arrangement. Drawing No. 90516 –Seakeeper 1 Bolt-In Installation Details provides additional details.
- Remove lifting eyes once the unit is installed. Lifting eyes must be removed prior to operation.
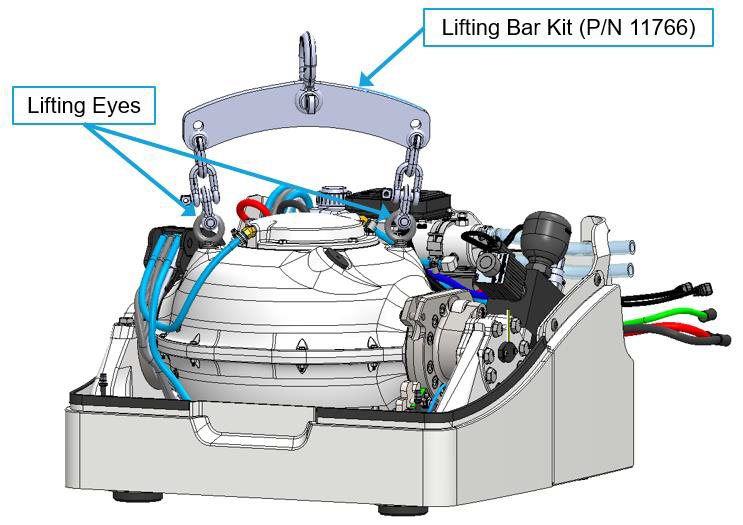
Figure 2 – Seakeeper 1 Lifting Arrangement
2.0 Mechanical Installation
2.1 Mechanical Installation Introduction
The Seakeeper 1 can produce forces of up to 1,515 lbs (6.74 kN) in the vertical direction, 2,248 lbs (10.0 kN) in the longitudinal direction, and 1,697 lbs (7.55 kN) in the lateral direction at each of the four mounts. Careful consideration should be given to foundation design to ensure it can safely transfer these loads into the hull. These loads represent a worst-case operating condition that includes a 6 G acceleration evaluated in each direction independently. The responsible party for designing the supporting structure (boat builder, installer, or hired sub-contractor) must accommodate the above forces plus a reasonable safety factor. Seakeeper recommends a minimum safety factor of 2.0 (resulting in a safety margin of 1.0).
It is assumed that the installer is familiar with mounting using mechanical fasteners to marine structures and has performed structural analysis to ensure the structure to which the Seakeeper mounts can properly transfer the loads the Seakeeper creates into the hull structure. If the installer has any doubt about the ability of the structure to transfer the loads to the hull, then a licensed naval architect or marine engineer should be contacted to do a structural analysis.
The installer should review the following list of reference drawings to ensure the mechanical installation procedure is fully understood.
Reference Documents & Drawings
2.2 Selection of Seakeeper Installation Location
2.2.1 Location Considerations
Selection of mounting location of the Seakeeper should consider the following desirable features:
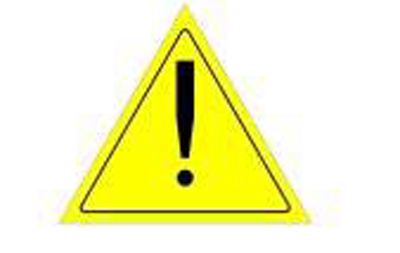
The Seakeeper should be installed aft of amidships to minimize high acceleration loadings due to hull / wave impacts during operation at high speed or in large waves. If the only possible installation location is forward of amidships, then the installer should have Seakeeper review the installation location prior to finalizing the design.
- Top-down access or sufficient clearance for access and removal of the Seakeeper 1 cover is required. For reference, see Drawing No. 90516—Seakeeper 1 Bolt-In Installation Details and Drawing No. 90514—Seakeeper 1 Bolt-In Clearances.
- Provide adequate clearance for all recommended scheduled maintenance and any necessary repairs, as shown in Figure 4 and Drawing No. 90516—Seakeeper 1 Bolt-In Installation Details.
- Access for the removal and re-installation of the Seakeeper 1 should be considered.
- The Seakeeper should be installed in a dry space to minimize the effects of corrosion. If installed and exposed to weather, use the deck cover enclosure (P/N 90628).
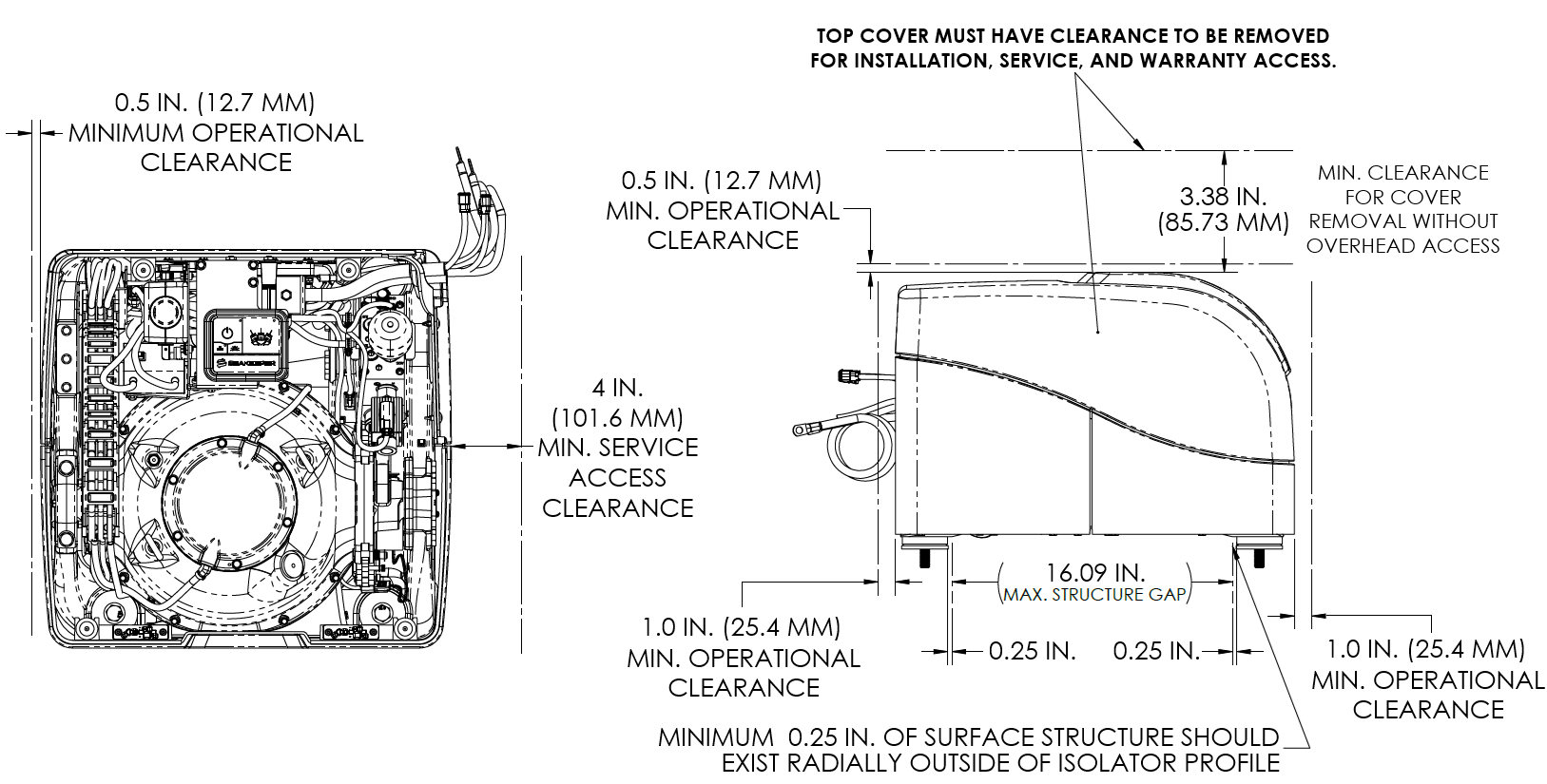
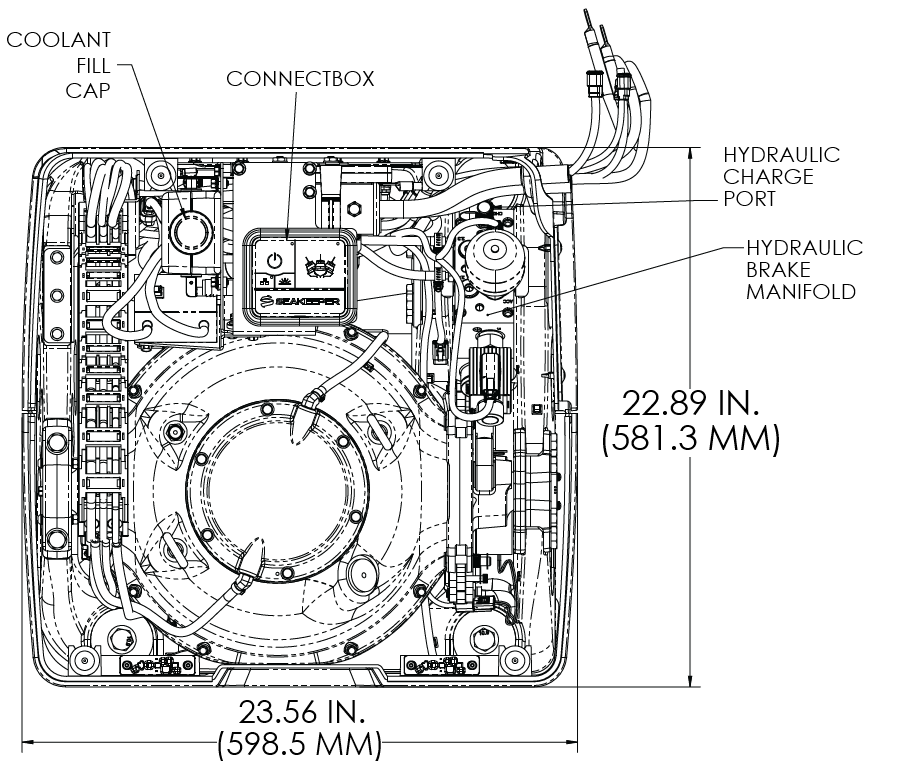

Figure 4 – Seakeeper 1 Service and Operating Clearances (Drawing No. 90516)
Note: Adequate access to remove the Seakeeper 1 cover must be incorporated into the installation design to allow for regular maintenance, service, and repair of components.
2.2.2 Noise and Soundproofing
Seakeeper noise has been measured under steady-state conditions (no wave load) in Seakeeper‘s Engineering Lab and in our Factory Demo Boat. The steady-state noise at 1 meter is typically less than 64 dBC. As the frequencies emitting the highest sound pressures are low (like other marine machinery), it is recommended that the Seakeeper be installed in an enclosed space such as a leaning post/seat, bilge, center console, or machinery space.
2.3 Mechanical Installation
Reference Documents & Drawings:
- 90514 – Seakeeper 1 Bolt-In Clearances
- 90516 – Seakeeper 1 Bolt-In Installation Details
- 90517 – Seakeeper 1 Installation Fixture Kit
- 90559 – Seakeeper 1 Generic Installation Guide
- 90599 – Seakeeper 1 Bolt-In Kit
- 90564-4 – Seakeeper 1 Installation Plate
- 90692-1 – Seakeeper 1 Deck Enclosure Installation Instructions
2.3.1 Preparation of Vessel Structure
Drawing No. 90559 – Seakeeper 1 Generic Installation Guide shows various structural arrangements to support the integration of the Seakeeper 1. The Generic Installation Guide offers above and below-deck installation arrangements with fiber-reinforced plastic (FRP) and aluminum structures, which should provide solutions for most vessels. Depending on the structure to which the Seakeeper is fastened, blind threaded holes or through-bolting can be utilized. The Seakeeper 1 is affixed to the hull via four bolts in the Seakeeper 1 frame. Each Seakeeper 1 foundation bolt has a vibration isolation assembly to minimize the transmission of vibrations to the hull structure.
Refer to Seakeeper Drawing No. 90516 – Seakeeper 1 Bolt-In Installation Details. This drawing contains critical design dimensions and loads that must be considered in the design of the boat’s structure that will receive the Seakeeper 1. It is assumed that a proper structural analysis has been performed for the vessel structure to which the Seakeeper will be fastened to ensure proper strength margins for the loads the Seakeeper will create during operation.
The vessel structure supporting the Seakeeper should be installed so the Seakeeper is parallel to the waterline in the transverse direction and within 2 degrees longitudinally.
In addition, the four areas on top of the structure on which the Seakeeper 1 will rest need to be co-planar within .06 in. (1.5 mm) to minimize potential distortion of Seakeeper isolation mounts when installed.
Seakeeper offers an installation fixture kit, P/N 90517. The fixture has four (4) holes at the same centers as the mounting holes on the Seakeeper 1. It locates the hole patterns at the proper spacing in the forward-aft direction and the port-starboard direction. See Figure 5 for more details regarding the Seakeeper 1 template.
Note: Do NOT use the installation fixture to establish the Seakeeper envelope dimensions or clearances. For envelope dimensions, refer to Drawing No. 90516—Seakeeper 1 Bolt-In Installation Guide. A 3-D model of Seakeeper 1 is available on the Seakeeper website, www.seakeeper.com, to aid in designing the Seakeeper foundation and the space around it.
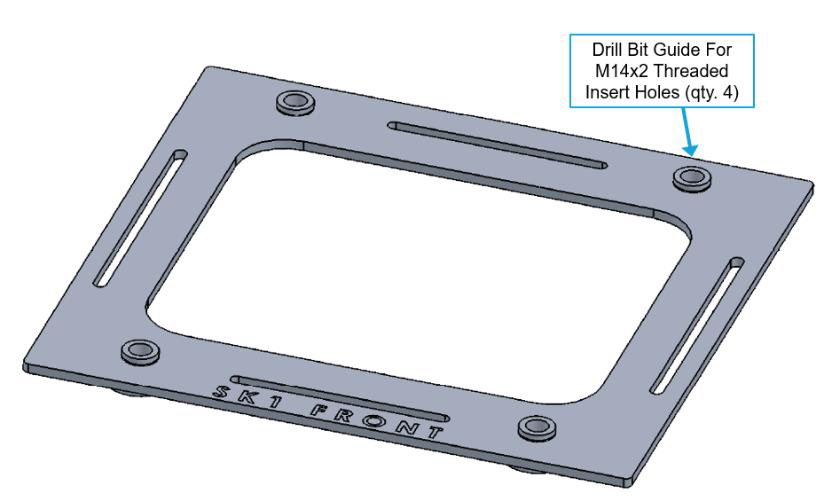
2.3.2 Transfer of Holes to Boat Structure
The following instructions should be used to establish the Seakeeper 1 bolt pattern on the hull structure designed to accept the Seakeeper 1, based on the information provided in Drawing No. 90599—Seakeeper 1 Bolt-In Kit and Drawing No. 90516—Seakeeper 1 Bolt-In Installation Details.
- Lower installation fixture onto vessel structure.
- The four Isolation Mounts, where the Seakeeper 1 contacts the hull structure, must be coplanar to within 0.06 in. (1.5 mm).
- Align fixture in desired location and transfer holes from fixture plate to the vessel structure by transfer punch. Note that holes in fixture plate are ø 9/16 in. (14.287 mm).
- Using the bushings in the fixture holes as a guide to stay perpendicular with the vessel structure, drill 4 X 9/16 in. diameter holes for M14-2.0 (21 mm length minimum) threaded inserts in vessel structure at marked locations to mate with holes in the Seakeeper foundation.
- Tap threads in holes for M14 x 2.0, 1.5 x diameter threaded inserts.
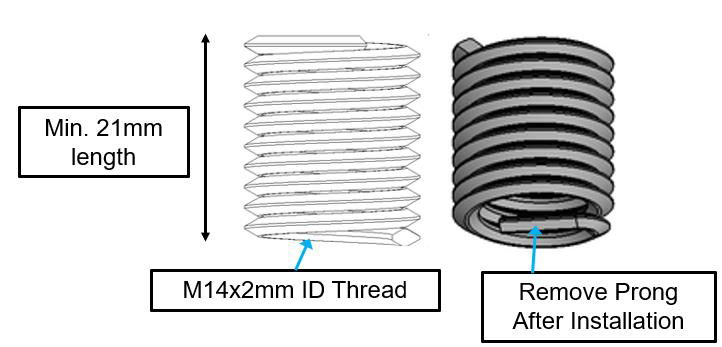
- Install threaded inserts into holes using Helicoil installation tool.
- Remove threaded insert prongs after threaded inserts are installed.
2.3.3 Installation of Seakeeper
- Locate and position the lower snubbing washers onto the vessel foundation structure at the four (4) hole locations.
- NOTE: Sealant or caulk should be applied around the outside edge of the lower face of each lower snubbing washer where it contacts the vessel structure. This will maintain the washer’s position and prevent water from wicking between the parts and causing corrosion.
- Sealant is not required between the snubbing washer faces and isolator bushings.
- Lower the Seakeeper 1 onto the lower snubbing washer on the vessel structure and align over drilled holes.
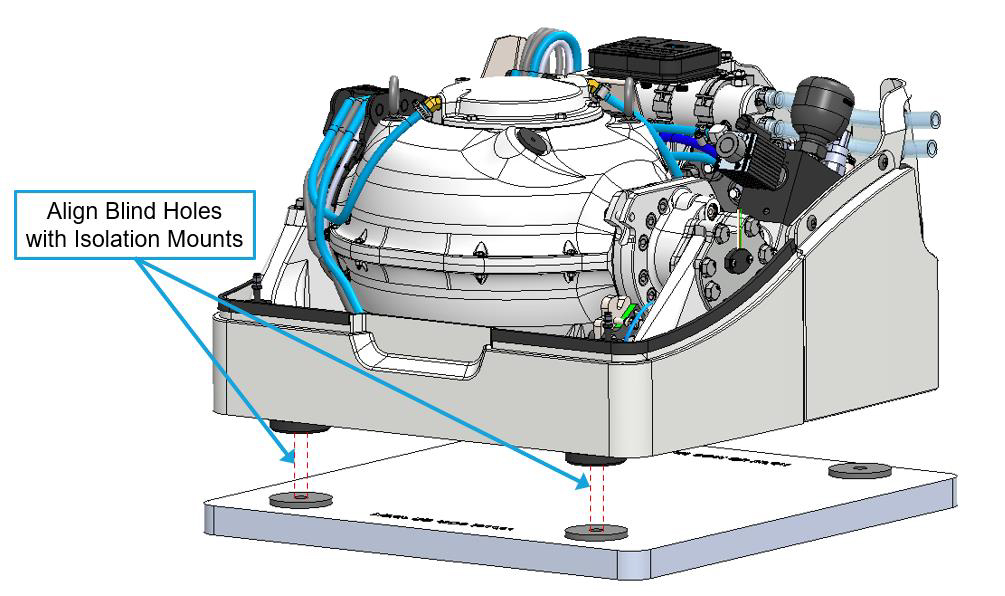
- Using a flexible extendable magnet (McMaster P/N: 3838A42 or similar), install the Seakeeper 1 Bolt-In Kit (P/N 90599): the isolation mount sleeve tube, upper snubbing washer, wedge-lock washer, and bolt at each isolation mount.
- Figure 8 shows an exploded view of the Bolt-In Kit.
- Before installation, apply a moderate coat of anti-seize to the threads of each bolt.
- By attaching the magnet to the upper snubbing washer, wedge-lock washer, and M14 Bolt, they can be stacked as one assembly.
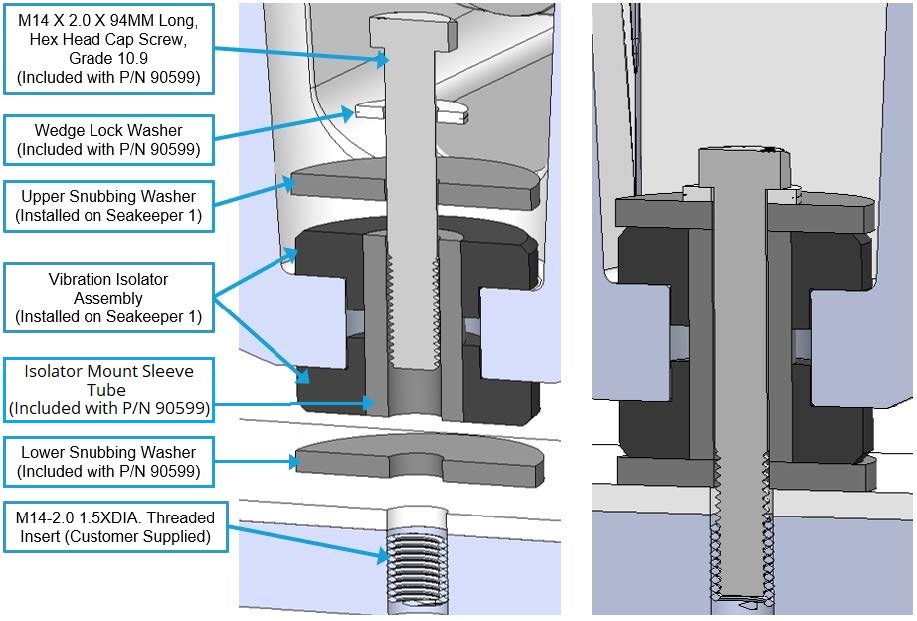
Figure 8 – Seakeeper 1 Bolt Stack Arrangement Cutaway –
Exploded (left) / Installed (right) (P/N 90599)
- Torque all fasteners to 115 ft-lbs (156 N-m). New bolts must be used for each installation and re-installation.
- Threaded inserts can be reused if they are intact and without damage.
- Proceed to the electrical and cooling portion of the installation.
3.0 Electrical Installation
3.1 Electrical Installation Introduction
This section for electrical installation explains how to mount the electrical equipment and how to connect the electrical cables.
Reference Documents & Drawings:
- 90510 – Seakeeper 1 Hardware Scope of Supply
- 90511 – Seakeeper 1 Cable Block Diagram
- 90512 – Seakeeper 1 Cooling Water Schematic
- 90558 – ConnectBox Helm Mounting Kit
- TB-90191 – Seawater Cooling Pump Recommendations
- TB-90575 – DC Installation Kits
- Seakeeper Compatibility Technical Bulletins
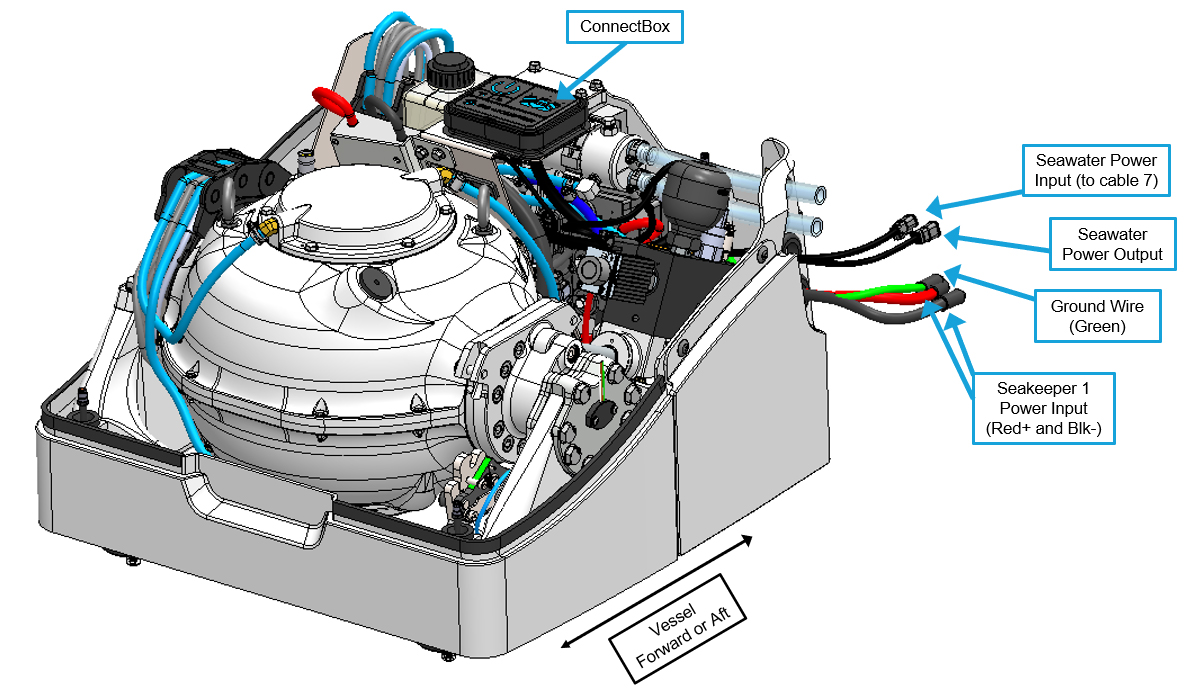
Figure 1 – Seakeeper 1 Isometric View with Electrical Connections
The following images show the electrical equipment included with the Seakeeper 1 Hardware Scope of Supply (Drawing No. 90510):
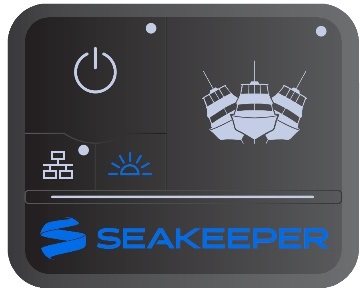
(20415)
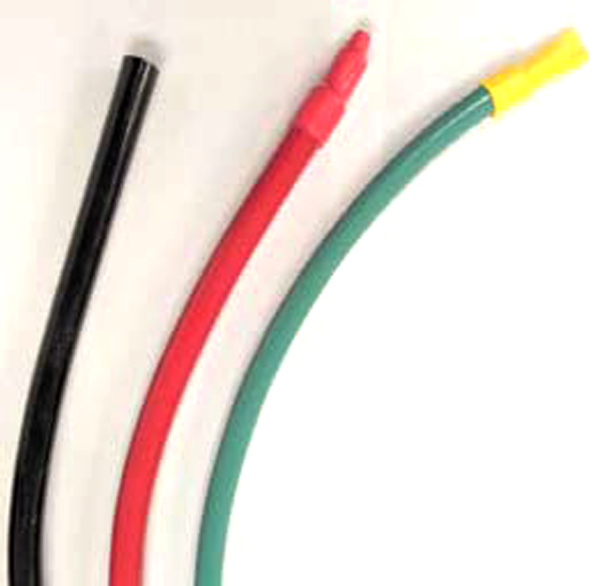
(20436, 20435, 20437)
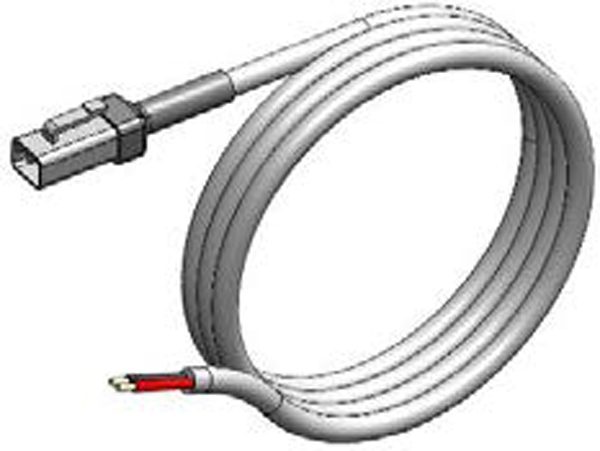
5 m. Length (30327)

5 m. Length (20334)
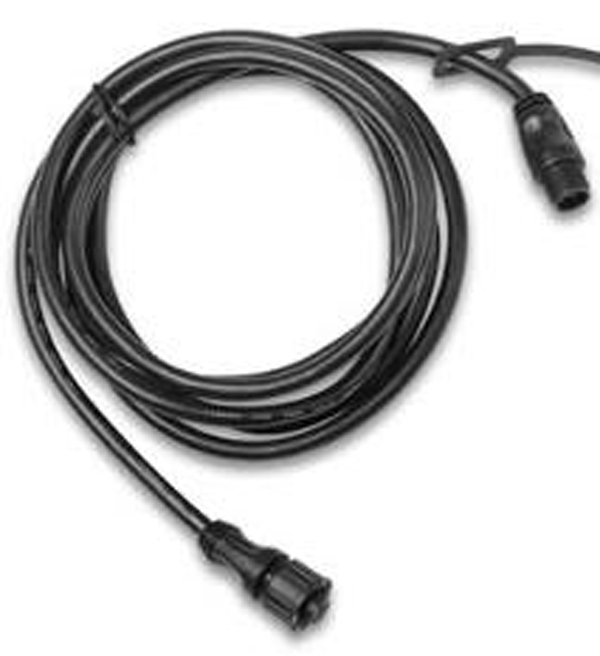
(30332)
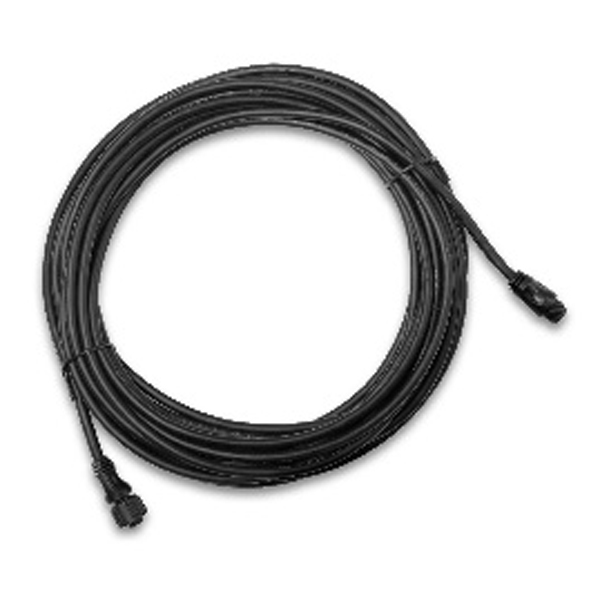
(30330)
Figure 2 – Electrical Equipment for Seakeeper 1
3.2 Electrical Equipment Connections
3.2.1 High Current 12 VDC Power
Source | Battery Bank, 12 VDC, Marine, Deep Cycle |
Voltage Range | 11.2 – 14.7 VDC |
Continuous Current | 55 A |
Overcurrent Protection | 80 A (Customer Supplied) |
High Current 12 VDC Power Connection Instructions
- Connect positive and negative High-Current 12 VDC cables, 2 AWG (33.6 mm2) conductors, to the 12 VDC power source.
- The positive and negative cables are supplied with a length of 1.8 m, and approximately 0.5 m is routed within the gyro frame (1.3 m outside frame).
- Splice customer-supplied 2 AWG conductors to the positive and negative 2 AWG cables per the Crimping Instructions of Figure 4, using Seakeeper-supplied butt connectors, to increase conductors to the desired length. The maximum cable length is 29.53 ft (9.0 m) each. See also Figure 4 below for splicing.
- Crimp the positive High-Current Cable to B+ Conductor (red). Conductor should be continuous throughout entire length; do not coil. The most direct route to the 12 VDC power source should be used.
- Repeat Step 3 for the negative High-Current Cable to B- Conductor (black).
- Install approximately 2 in. (51 mm) of double wall (adhesive lined) heat shrink tubing over entire butt connector and onto both sides of conductor insulation.
- Connect positive conductor (B+, red) through dedicated 80 A overcurrent protection device (customer-supplied) and a dedicated isolation switch (customer-supplied), then directly to battery plus terminal or bus bar.
- Connect negative conductor (B-, black) directly to battery minus terminal or DC negative bus.
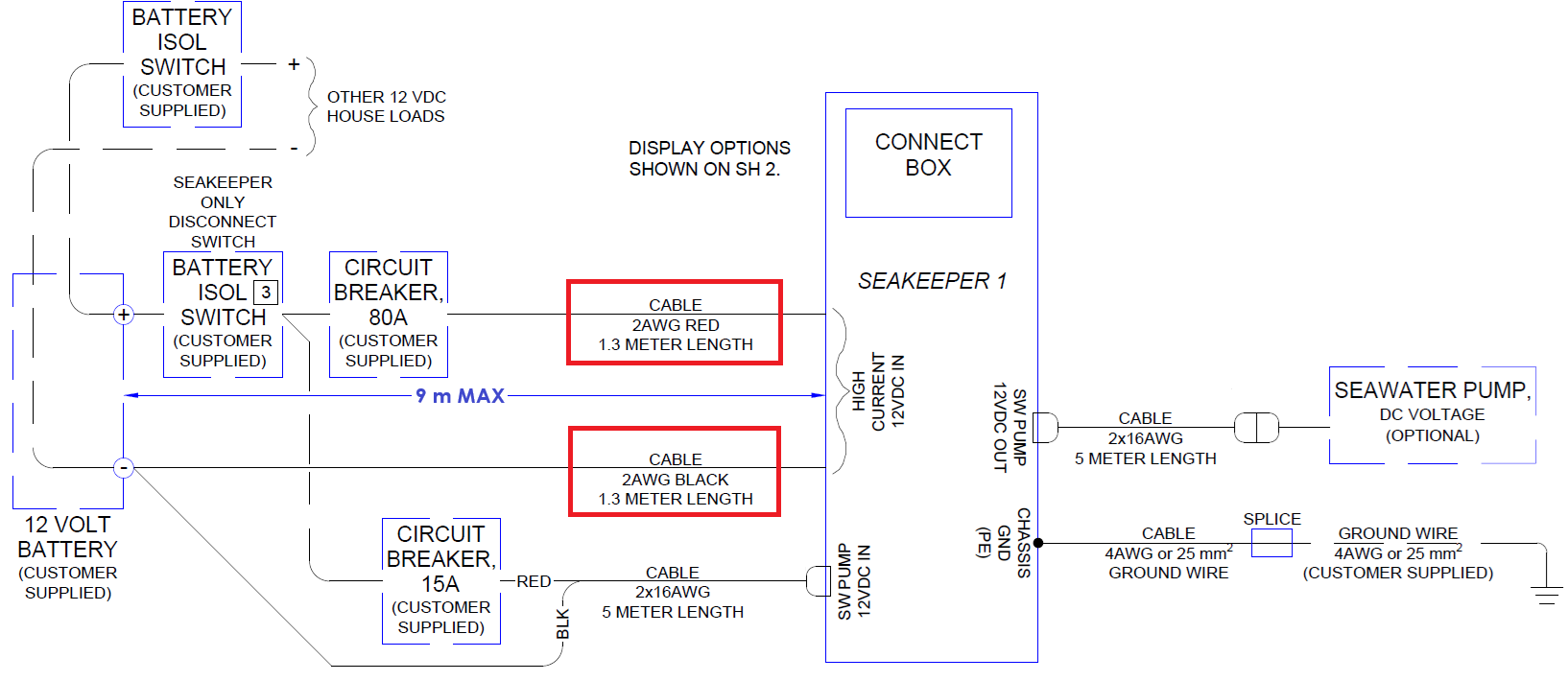
Figure 3 – Seakeeper 1 Cable Block Diagram (Drawing No. 90511) –
High Current Connection Highlighted
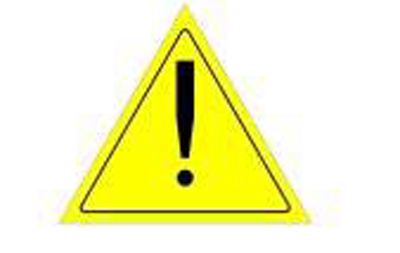
Reversing polarity on the DC power input to the Seakeeper can result in damaging the electronics in the control system.
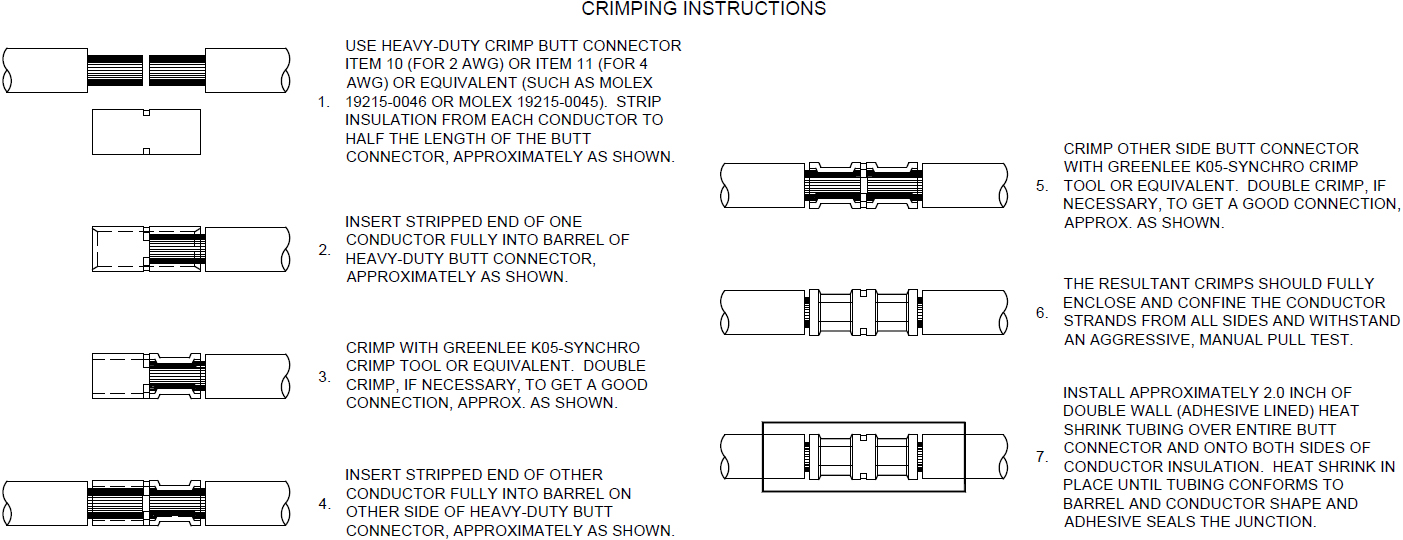
Figure 4 – High Current DC Input Crimping Instructions
3.2.2 Seawater Pump 12 VDC Power
Power Source | Battery Bank, 12 VDC, Marine, Deep Cycle |
Voltage Range | 11.2 – 14.7 VDC |
Current Rating | Max 15 A rating |
Overcurrent Protection | Per pump specification, max 15 A |
Seawater Pump 12 VDC Power Input Connection Instructions
- Connect Seawater Pump Input Cable (P/N: 30327) to Seakeeper 1 “SW Pump DC In” as shown in Drawing No. 90511 – Seakeeper 1 Cable Block Diagram, with overcurrent protection corresponding to seawater pump selected.
- Connect the 16 AWG (1.5 mm2) plus conductor (red) through dedicated overcurrent protection device (customer-supplied), maximum of 15 A, to dedicated battery isolation switch.
- The positive High-Current 12 VDC cable, 2 AWG B+ conductor (red), is capable of carrying the current for both the High Current and Seawater Pump from the 12 VDC power supply to the battery isolation switch.
- Connect the 16 AWG (1.5 mm2) minus conductor (black) directly to battery minus terminal or DC main negative bus.
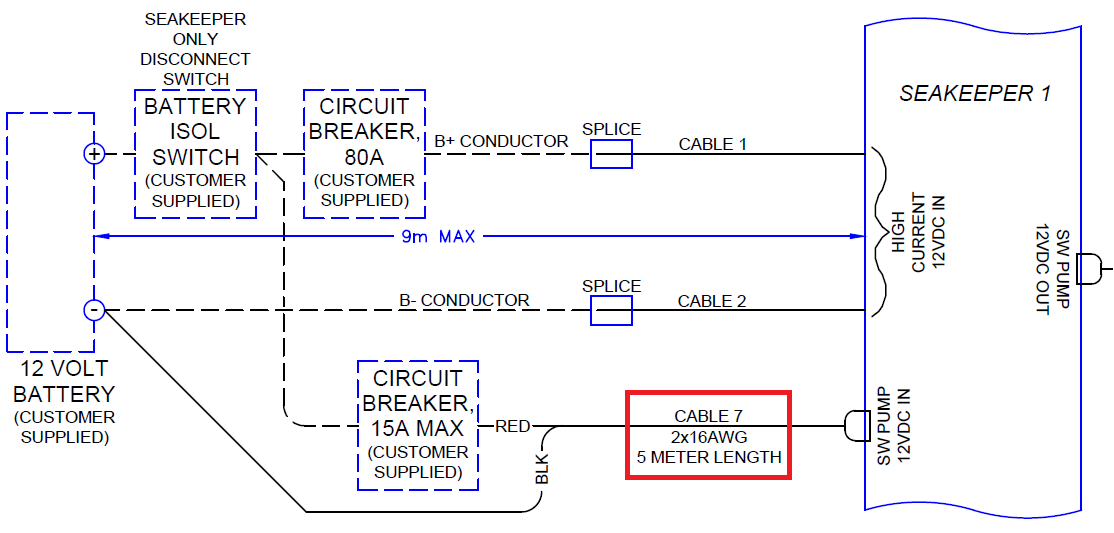
Seawater Pump 12 VDC Power Output Connection Instructions
- Connect Seawater Pump Output Cable to the Seakeeper 1 “SW Pump 12 VDC Out” for DC power output to the seawater pump. The cable is a 2 x 16 AWG cable (1.5 mm2), 16 ft (5 m) length, with a size 16 female Deutsch plug.
- Pumps rated at 12 VDC, 15 A maximum, customer-supplied, must be configured with a Deutsch DT series, 2-pin receptacle to mate with the connector shown in figure 6.
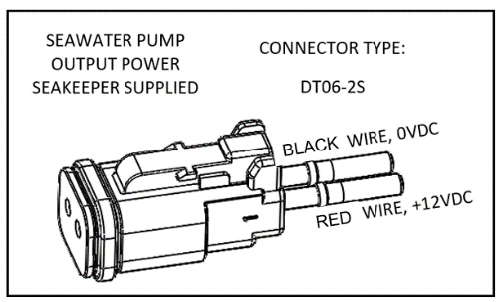
- The Seawater Pump Output Cable must be routed and installed in the vessel from the Seakeeper 1 “SW Pump 12 VDC Out” Deutsch connector (pins end) to the DC seawater pump cable Deutsch connector (socket end).
- Connect Seawater Pump Output Cable plug end (female end) to the customer-supplied receptacle end (male end). The recommended wiring is shown in the following figure.
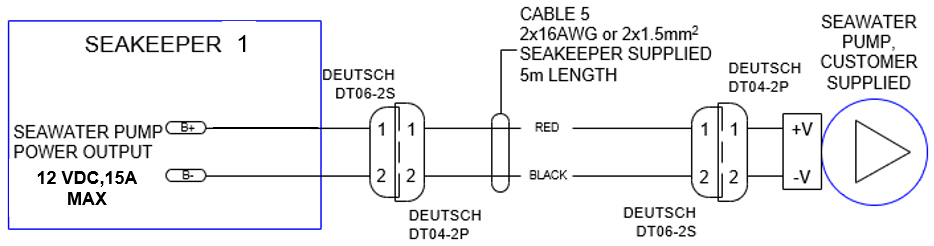
Figure 7 – Seawater Pump Power Output Cable
- Seakeeper DC Seawater Pump Assembly (P/N 30331), which is prewired for DC Seawater Output Cable, is available as an option with the Seakeeper 1.
3.3 Electrical Equipment Ground Connections
Seakeeper 1 to Vessel Ground Connection Instructions
- Connect ground cable, 4 AWG (25 mm2), polyethylene (PE) cable to vessel grounding bus to comply with:
- EN/IEC 60204-1 Clauses 6.3.3 and 8.2.3.
- ABYC E-11 July 2021 Clauses 11.15.2 and 11.17.
- Butt splice green ground cable, 4 AWG (green) to a 4 AWG ground wire (customer-supplied) suitable in length for the specific installation, as shown in the following figure.
- Note: GROUND CABLE (GREEN) SHOULD ONLY BE USED FOR GROUNDING THE SEAKEEPER TO THE VESSEL GROUND.
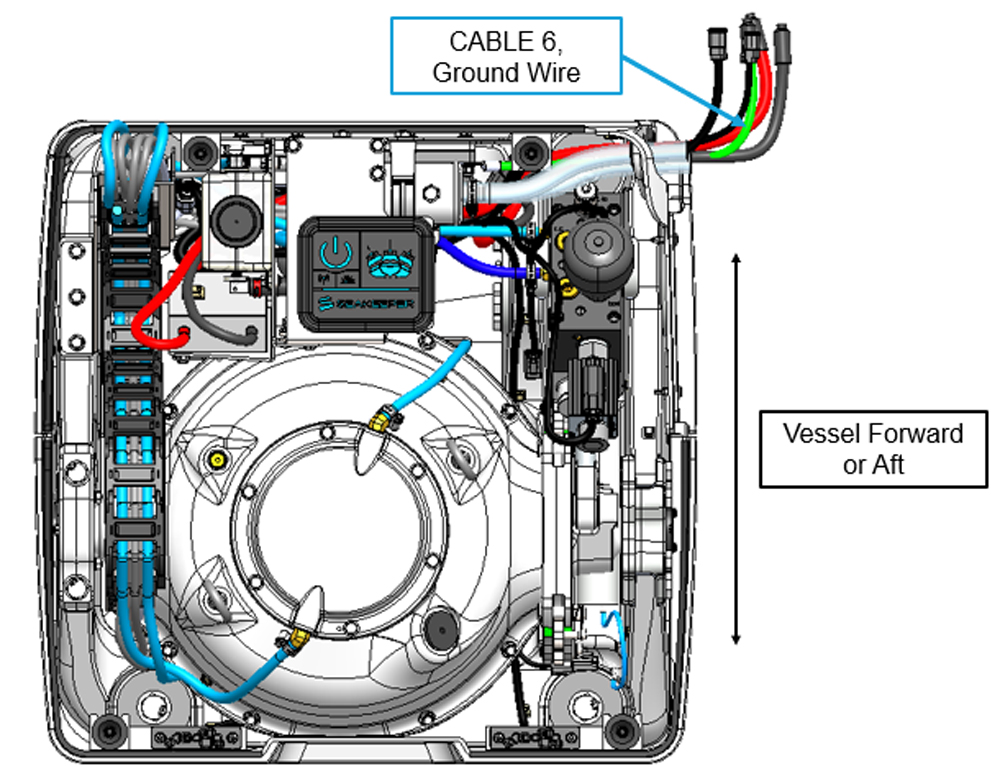

3.4 Seakeeper 1 Display Connection
Seakeeper 1 Display Options
The Seakeeper 1 requires a compatible Multifunction Display (MFD).
A display is required with the installation of a Seakeeper 1 to support the full functionality of the unit through the Seakeeper App in addition to the ConnectBox. The Seakeeper App provides an interface for controlling the Seakeeper 1 or viewing the Settings, Service, Info, and Alarm pages. The Seakeeper ConnectBox can be helm-mounted to provide an additional interface for controlling the Seakeeper 1 but does not replace the need for a Seakeeper-compatible display.
Figure 10 provides a schematic of the display installation:
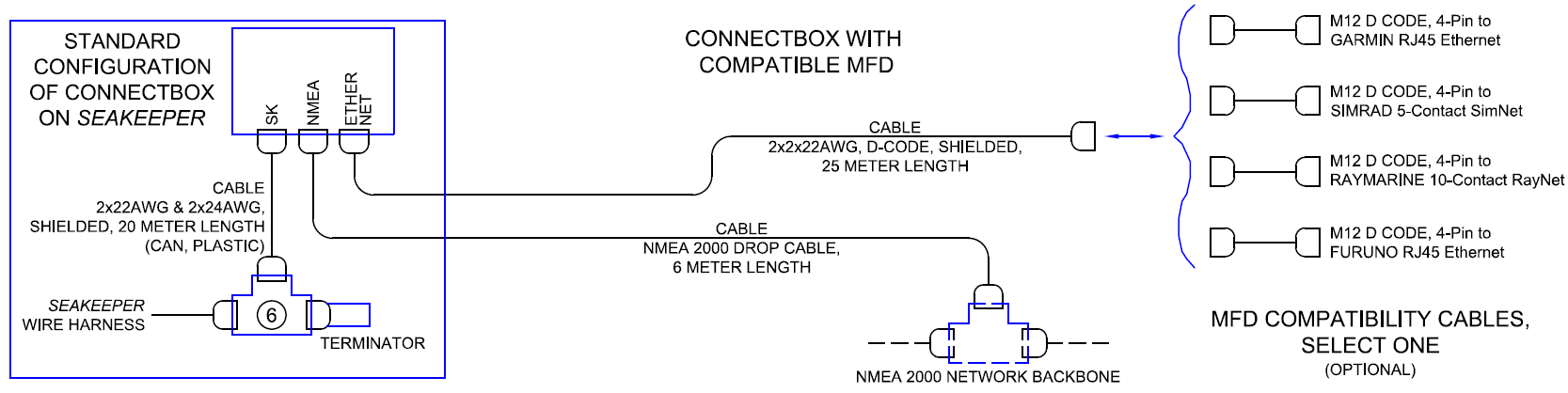
Connecting to a Compatible MFD
- The Seakeeper 1 can be connected to a variety of available MFD systems. Refer to the Technical Bulletins Section of the Seakeeper Technical Library for manufacturer specific MFD compatibility technical bulletins.
- MFD specific Technical Bulletins will be updated regularly as new MFD systems become compatible. Currently Garmin, Raymarine, NAVICO, and Furuno offer compatible MFD models.
- Once a compatible MFD has been selected, refer to the appropriate manufacturer specific Technical Bulletin for integration instructions.
- Connect Seakeeper-supplied Ethernet Adapter Cable, D-Code 10 m cable to MFD manufacturer-specific Ethernet adapter cable. Custom Ethernet cables for specific MFD manufacturers are available through Seakeeper and must be purchased with the Seakeeper 1 if connecting to an MFD.
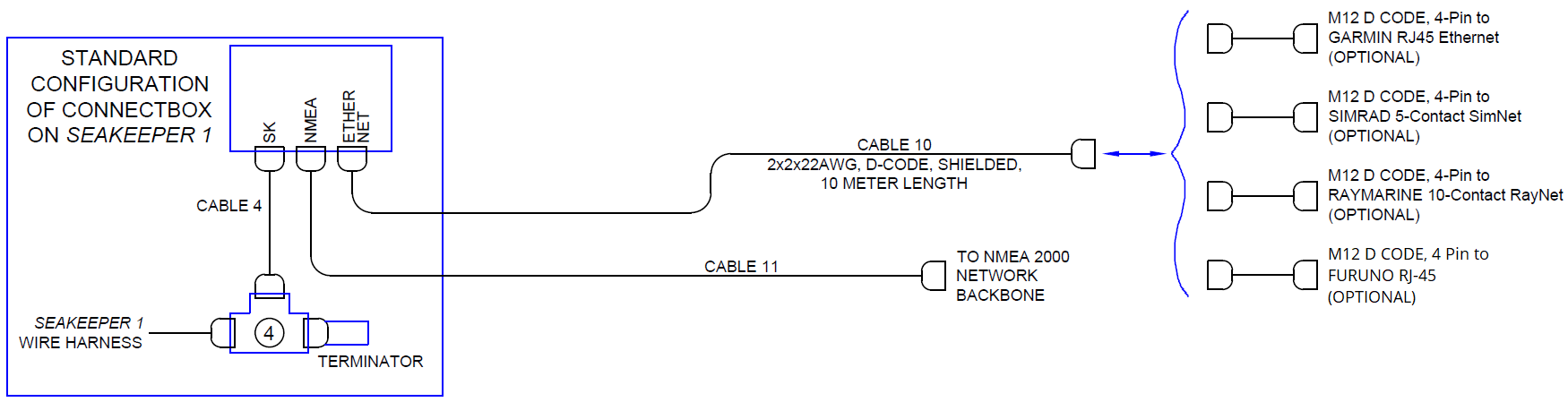
NMEA 2000 Network Connection
The Seakeeper 1 requires a connection to the vessel’s NMEA 2000 network backbone. The Seakeeper 1 will monitor information on the NMEA network to support and optimize the performance of the Seakeeper 1.
- Connect Seakeeper-supplied NMEA Drop Cable to the customer-supplied NMEA 2000 Tee Adapter on vessel’s NMEA 2000 backbone.
- An active NMEA 2000 compatible GPS signal is required on the vessel’s NMEA 2000 backbone to operate the Seakeeper 1.
- If no GPS signal is detected, a warning will be present on the Seakeeper App.
- An active NMEA 2000 compatible GPS signal is required on the vessel’s NMEA 2000 backbone to operate the Seakeeper 1.
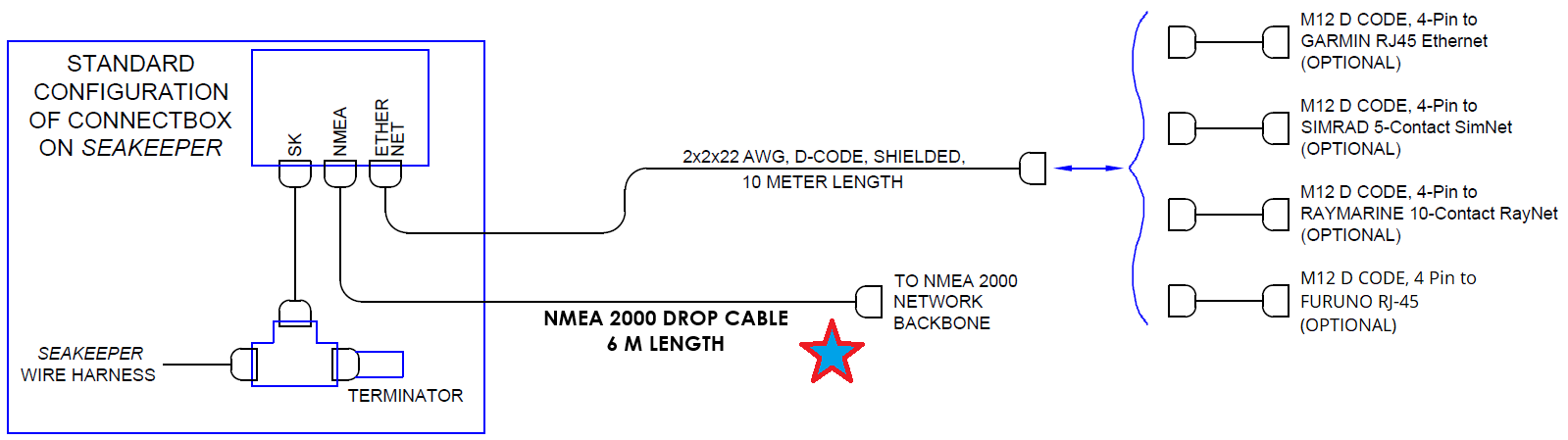
ConnectBox Helm Mounting – Optional
- Remote ConnectBox mounting requires Seakeeper part number 90558, ConnectBox Remote Mount Kit.
- Console space required: Approx. 3.41 L x 4.15 W in. (87 x 106 mm).
- Mounting Instructions, Surface Mount: See Drawing No. 90558 – Seakeeper 1 ConnectBox Helm Mounting Kit, for details. Seakeeper ConnectBox 3D Model available upon request.
- Mount ConnectBox Replacement Blank Insert (P/N 12206) into Seakeeper 1 enclosure at the original location of the ConnectBox.
4.0 Cooling Installation
4.1 Cooling Installation Introduction
Reference Drawings and Documents:
- 90511 – Seakeeper 1 Cable Block Diagram
- 90512 – Seakeeper 1 Cooling Water Schematic
- TB 90947 – Seawater Plumbing Best Practices
- 30331 – Seakeeper DC Seawater Pump Assembly
The Seakeeper 1 is shipped with the cooling circuit filled and ready for use. The Seakeeper 1 requires connection to a raw water pump, referred to as the seawater pump, to cool the closed loop cooling circuit on the unit. The required seawater flow through the Seakeeper 1 heat exchanger is between 2 and 4 GPM (7.6 and 15.2 LPM). Prior to operation, confirmation of the glycol level is recommended.
Seakeeper offers a compatible self-priming DC Seawater Pump (P/N 30331) prewired for the Seakeeper 1 Installation and covered under the standard Seakeeper warranty. For details, see Drawing No. 30331—Seakeeper DC Seawater Pump Assembly and the Seakeeper Options and Accessories Price List.
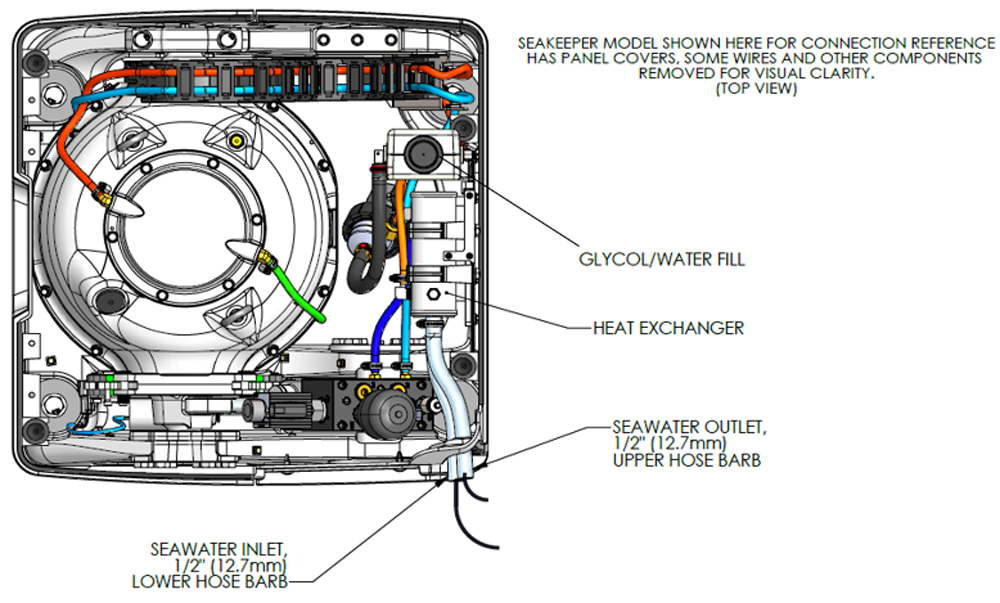
4.2 Installation Considerations
- The installer is responsible for supplying a dedicated seawater pump and associated plumbing. An optional seawater pump can be purchased through Seakeeper, P/N 30331.
- Unintended seawater flow from the seawater pick-up during the vessel’s underway operation is unacceptable and may cause stress to internal components. Unintended flow should be mitigated through pump selection, using a diaphragm-style pump or an inlet control valve. Continuous cooling flow from shared through-hull plumbing, a centralized chiller, or a cooling system is unacceptable for on-demand Seakeeper models.
- Seawater connections on the Seakeeper heat exchanger mate with ½ in. (13 mm) hose.
- As outlined in the Electrical Installation section, the seawater pump is powered by a cable (P/N 20334) via “SW Pump 12 VDC Out” on the Seakeeper 1.
- The seawater pump operates on 12 VDC with a max overcurrent protection rating of 15 A.
- To ensure sufficient seawater flow to each Seakeeper unit onboard the vessel, a dedicated through-hull fitting should be installed.
- It is recommended that the seawater pump is located below the waterline, as close to the vessel’s baseline as practically possible, to maintain positive inlet pressure on the pump in all operating conditions.
- A self-priming seawater pump may be required to maintain water flow in all underway conditions. Cavitation can occur at the seawater inlet and potentially cause an air-lock condition restricting seawater flow to the heat exchanger.
- Maximum allowable seawater pressure in heat exchanger is 20 psi (1.4 bar).
- The seawater flow requirement through the Seakeeper heat exchanger is 2 GPM (7.6 LPM) minimum and 4 GPM (15.1 LPM) maximum under all operating conditions.
- When sizing the seawater pump, installers should consider losses for raw water plumbing.
- A forward-facing scoop / highspeed seawater inlet should be installed to ensure sufficient seawater flow during underway operation.
4.3 Connecting Seawater to Heat Exchanger
Refer to Figure 2 for typical seawater plumbing arrangement.
- Connect seawater pump to Seakeeper dedicated through-hull fitting. A strainer and seacock valve should generally be installed between the seawater inlet and the pump.
- Connect seawater from the installer-supplied seawater pump to the lower ½ in. (13 mm) hose barb on the heat exchanger.
- Use the same practices as other below waterline seawater plumbing.
- Connect the seawater discharge (upper hose barb) to the overboard drain. Use the same practices as for other below-waterline seawater plumbing.
- During commissioning, seawater flow should be checked to be within the flow requirements while the vessel is at rest, at speed, and when backing down.
- If no other method of confirming flow is available, the discharge line may be temporarily diverted to a bucket. The flow rate is calculated based on the time required to fill a known volume in GPM or LPM.
- Flowrates over 4 GPM (15.2 LPM) could affect heat exchanger life.
- After sea trial / commissioning, inspect all raw water plumbing for any signs of leakage.
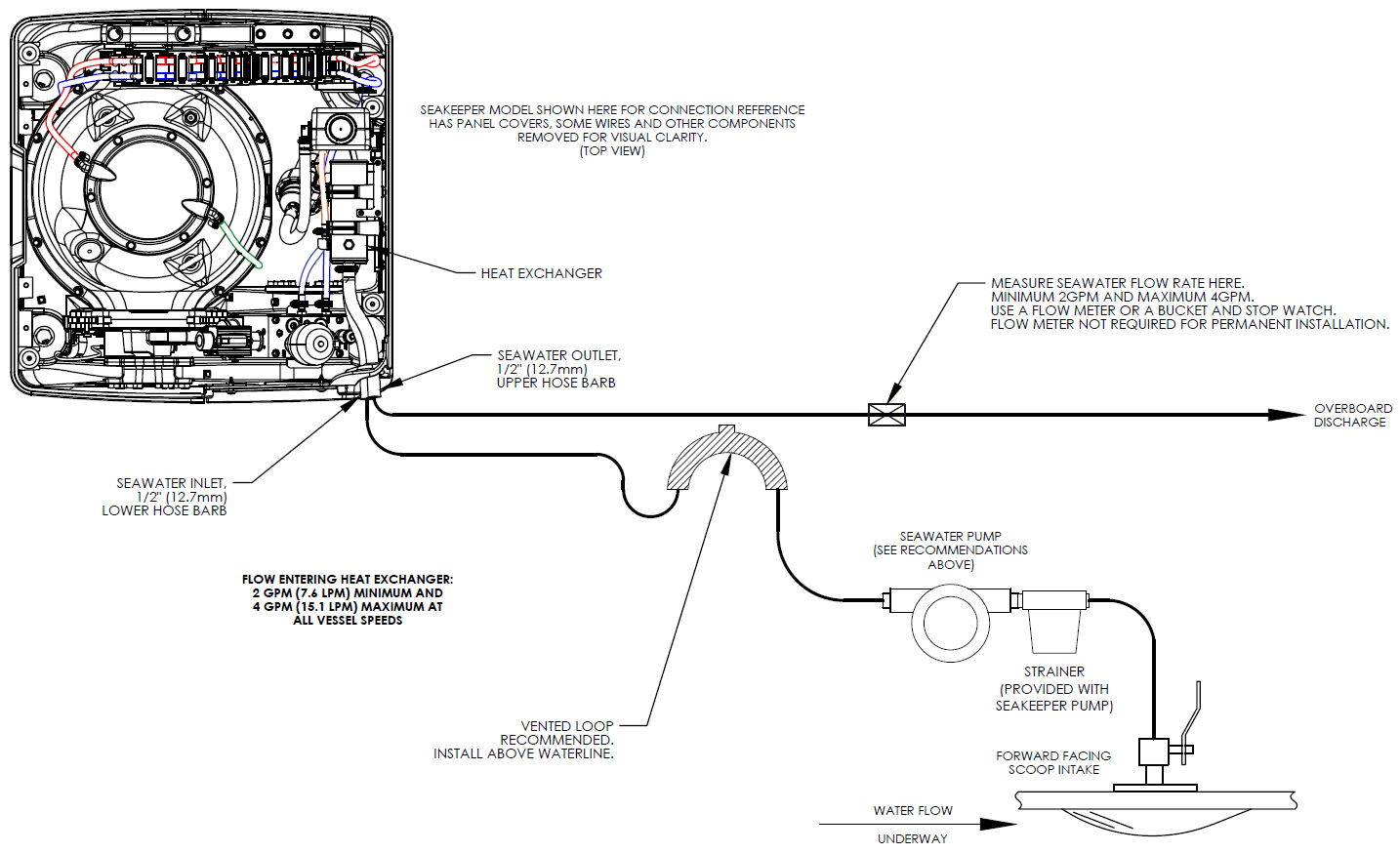
Seakeeper Optional DC Seawater Pump (P/N 30331)
Voltage: | 24 VDC (Operate at 12 V for Seakeeper 1) |
Rated Flow: | 2.5 GPM (9.5 LPM), at 12 VDC |
Overcurrent Protection: | 15 A |
Ignition Protection: | ISO 8846 or equivalent |
- Seakeeper offers a self-priming DC Seawater pump as an optional addition, P/N 30331– DC Seawater Pump Assembly, shown in figure below.
- The Seakeeper Seawater Pump is a 24 VDC pump operated at 12 VDC for the Seakeeper 1 and maintains a seawater flow of approx. 2.5 GPM (9.5 LPM) at 12V DC.
- The pump assembly is pre-wired for connection to Seakeeper 1 Seawater Pump Output Cable and includes a seawater strainer and various fittings. The pump specifications are as follows:
NOTE: Use only SeaFlo®-provided threaded fittings for DC Seawater Pump 30331.
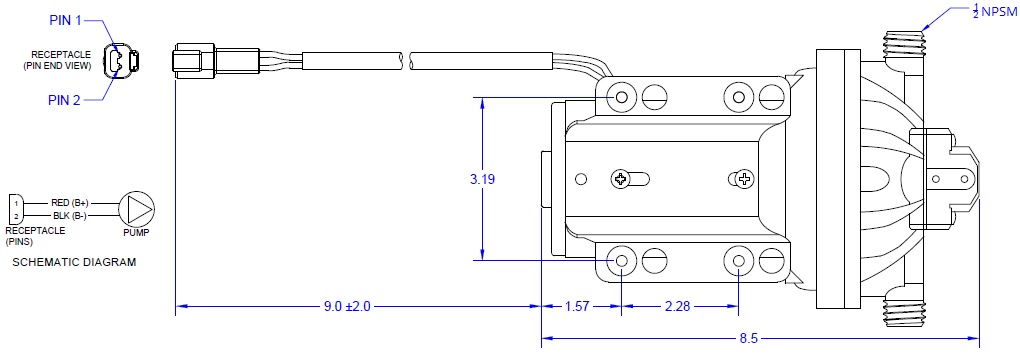
4.4 Adding Coolant
- The Seakeeper 1 cooling system is filled to proper level when shipped, with a mixture of 50% ethylene glycol and 50% distilled water.
- The coolant reservoir should be filled with colored coolant mixture, as shown in the following figure. If level has dropped, check for evidence of leaks at all connections before adding fluid as described below.
- If coolant is at the correct level, (see Figure 2) skip to the Connecting Seawater to Heat Exchanger section.
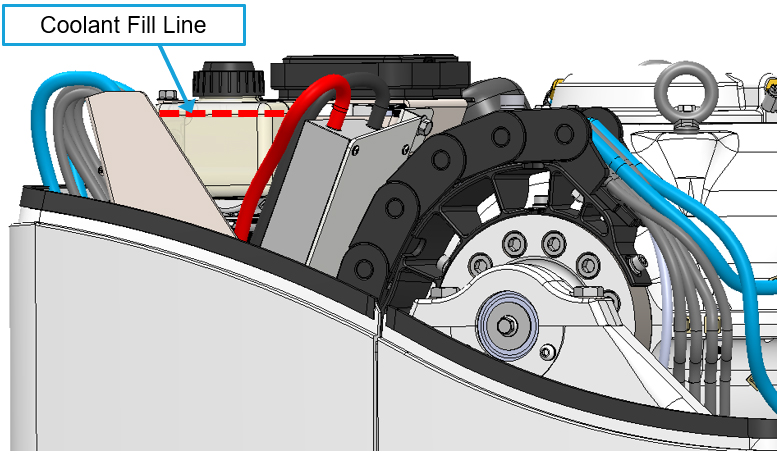
- Mix 50% ethylene glycol with 50% distilled water in a clean container. Refer to glycol manufacturer’s literature for freezing points.
- Ethylene glycol with corrosion inhibitors is required. Most commercially available glycol has these additives standard.
- Remove reservoir cap and pour mixture in until level reaches top face of the reservoir enclosure, as shown in Figure 4.
- Filling reservoir above this level will not cause any damage but coolant may be expelled from the vented cap due to normal thermal expansion of coolant.
- Once the Seakeeper 1 and DC Seawater pump are connected to 12 VDC power:
- Check the Seakeeper Display interface for any ALARMS.
- Cycle the Seakeeper 1, press the POWER ON button.
- The flywheel will start to spin and the glycol pump will start.
- Recheck glycol level with fluid circulating in coolant circuit to ensure the correct fill level is maintained.
- After several minutes of running, press POWER OFF button.
- The cooling system is self-purging. If small amounts of air are in the system, they should be dislodged during the first sea trial. Recheck level after sea trial and add fluid if required.
NOTE: It is not uncommon to see some air in the coolant system.
It is normal and will not affect operation.
5.0 Installation Requirements
5.1 Installation Requirements Introduction
The Installation Requirements section outlines the components and tools needed for the Seakeeper 1 installation that are not included within the scope of supply.
5.2 Required Supplies for Seakeeper Installation
Table 1 outlines the customer-supplied components required for the Seakeeper 1 installation:
Table 1: Components and Supplies Required for Seakeeper 1 Installation
Item | Description | Qty | Installation Manual Reference | Other Reference | System |
---|---|---|---|---|---|
1 | Spreader bar for lifting the Seakeeper 1 | 1 | Transport and Unpacking | P/N 11766 | Mechanical |
2 | Seakeeper 1 Foundation | 1 | Mechanical Installation | Dwg 90559 | Mechanical |
3 | Seakeeper 1 Fixture Kit | 1 | Mechanical Installation | P/N 90517 | Mechanical |
4 | Threaded insert: M14-2 x 1.5DIA (21 mm) | 4 | Mechanical Installation | Dwg 90516 | Mechanical |
5 | Seakeeper 1 Bolt-In Kit | 1 | Mechanical Installation | P/N 90599 | Mechanical |
6 | Marine Sealant | AR | Mechanical Installation | Dwg 90516 | Mechanical |
7 | Anti-Seize | AR | Mechanical Installation | Dwg 90516 | Mechanical |
8 | Conductor, Marine, 2 AWG, red (B+ Positive) | AR | High Current 12 VDC Connection | Dwg 90511 | Electrical |
9 | Conductor, Marine, 2 AWG, black (B- Negative) | AR | High Current 12 VDC Connection | Dwg 90511 | Electrical |
10 | Circuit Breaker, 80 A | 1 | High Current 12 VDC Connection | Dwg 90511 | Electrical |
11 | Battery Isolator Switch | 1 | High Current 12 VDC Connection | Dwg 90511 | Electrical |
12 | Seawater Pump, 12 VDC, 15 A max Optional: DC Seawater Pump Assembly (prewired) | 1 | Seawater Pump Connection Instructions | Dwg 90512, P/N 30331 | Electrical / Cooling |
13 | Circuit Breaker corresponding to pump rating | 1 | Seawater Pump Connection Instructions | Dwg 90511 | Electrical |
14 | Deutsch DT Series 2-pin Receptacle – Female *Not required with Seakeeper Seawater Pump (30331) | 1 | Seawater Pump Connection Instructions | Dwg 90511 | Electrical |
15 | Conductor, Marine, 4 AWG, green (Ground) | AR | Electrical Equipment Ground Connections | Dwg 90470 | Electrical |
16 | Compatible MFD Display | 1 | Seakeeper 1 Display Connection | Dwg 90511, TB 90573, P/N 90600 | Electrical |
17 | MFD Connection Cable, M12 D Code, 4-Pin | 1 | Seakeeper 1 Display Connection | P/N 20373, 20380, 20346 | Electrical |
18 | NMEA 2000 Backbone with compatible GPS Signal | 1 | Seakeeper 1 NMEA 2000 Network Connection | Dwg 90511 | Electrical |
19 | Through-hull fittings (1 high-speed pick-up / 1 overboard discharge) | 2 | Installation Considerations | Dwg 90512 | Cooling |
20 | Seawater Strainer *Included with Seakeeper Seawater Pump (30331) | 1 | Connecting Seawater to Heat Exchanger | Dwg 90512 | Cooling |
21 | Seacock Valve | 1 | Connecting Seawater to Heat Exchanger | Dwg 90512 | Cooling |
22 | ½ in. ID Seawater Hose | AR | Connecting Seawater to Heat Exchanger | Dwg 90512 | Cooling |
23 | Hose Clamps ½ in. (13 mm) fittings (2 per connection) | 8 | Connecting Seawater to Heat Exchanger | Dwg 90512 | Cooling |
AR = As Required
Dwg = Drawing
P/N = Seakeeper Part Number
5.3 Tools Required for Installation
Table 2 outlines the tools and equipment required for the Seakeeper 1 installation:
Table 2: Tools and Equipment Required for Seakeeper 1 Installation
Item | Description | Use |
---|---|---|
1 | Hoist, Forklift, or Crane | Unpacking and lifting Seakeeper 1 into position |
2 | Transfer Punch Kit | Locate foundation hole penetrations |
3 | Drill / Drill Press | Bolt hole penetrations |
4 | Threaded Insert Installation Kit | Tap and install threaded inserts (M14x2 1.5xDIA) |
5 | Marine Sealant | Lower snubbing washer installation |
6 | Flexible Extendable Magnet, McMaster P/N: 3838A42 or similar | Lowering foundation bolts into place |
7 | ½ in. Drive Torque Wrench | Foundation Bolts (115 ft/lbs [15 N-m]) |
8 | 12-18 in. Extension, ½ in. Drive | Foundation Bolts |
9 | 22 mm Socket | Foundation Bolts |
10 | Utility knife | Scoring cable jackets |
11 | Wire cutter | DC Power Cables |
12 | Wire stripper | DC Power Cables |
13 | Greenlee K05-Synchro Crimp Tool or Equivalent | 12 VDC High Current Input Cables, 2 AWG Ground Cable, 4 AWG |
14 | Heat gun | For conductor 1, 2, 6 heat shrink |
15 | Fish tape | Cable pulls |
16 | Hole saw | Thru-hull fittings |
17 | ¼ in. (7 mm) Nut Driver / Flat Head Screwdriver | Hose clamps |
Note: Additional tools could be required for the installation of customer-supplied components.
6.0 Installation and Start Up Checklist
6.1 Installation and Start Up Checklist Introduction
Reference Documents & Drawings:
- 90516 – Seakeeper 1 Bolt-In Installation Details
- 90511 – Seakeeper 1 Cable Block Diagram
- 90512 – Seakeeper 1 Cooling Water Schematic
- 90437 – Seakeeper Commissioning Form
- SWI-105 Commissioning Checklist
- 90520 – Seakeeper 1 Operation Manual
- 90569 – Seakeeper ConnectBox and Application Quick Start Guide
The Installation and Start-Up Checklists in this section provide an overview of the primary steps covered in the installation manual and should be referenced throughout the installation process. Upon completing the Seakeeper 1 installation, the installer should commission each Seakeeper unit with the Seakeeper Commissioning Form (90437). The Commissioning Checklist Work Instruction (SWI-105) provides a checklist of items to inspect and verify during the commissioning process and supplements the Seakeeper Commissioning Form (90437).
All Seakeeper stabilizers should be commissioned to verify that installation specifications and requirements have been implemented properly. The commissioning process should include completing the Seakeeper Commissioning Form (90437), all the items in the Installation Checklist, and verifying that Seakeeper 1 operates without alarms or abnormal behavior.
6.2 Installation Checklist
6.2.1 Mechanical Checklist
- Seakeeper foundation installed per requirements of Drawing No. 90516 – Seakeeper 1 Bolt-In Installation Details.
- Structure designed to accommodate Seakeeper 1 forces, as defined in Drawing No. 90516 – Seakeeper 1 Bolt-In Installation Details, with a minimum safety factor of 2.0.
- Foundation is co-planar within 0.06 in. (1.5 mm).
- Clearances around Seakeeper meet service and operating specifications and no obstructions are within the Seakeeper envelope.
- Seakeeper 1 Bolt-In Kit is installed (P/N 90599), includes: M14-2 x 94 mm Hex Head Bolt, M14 wedgelock washer, upper snubbing washer, isolation mount tube sleeve, and lower snubbing washer at each corner.
- Foundation bolts torqued to specification: 115 ft-lbs (156 N-m).
- Seakeeper 1 cover can be removed to access and service the unit.
6.2.2 Electrical Checklist
6.2.2.1 High Current 12 VDC Power Source: Cable 1 & 2
- Butt splice Cable 1 and Cable 2 to customer-supplied 2 AWG B+ and B- conductors to allow for routing to 12 VDC power source.
- Butt splice instructions can be found in Drawing No. 90511 – Seakeeper 1 Cable Block Diagram.
- Heat shrink
- Connect spliced Cable 1, B+ conductor (red), through 80 A circuit breaker (customer-supplied) and a dedicated battery isolation switch (customer-supplied), directly to the battery plus terminal or bus bar.
- Connect spliced Cable 2, B- conductor (black), to battery minus terminal or DC main negative bus bar.
6.2.2.2 Seawater Pump Connection: Cable 5 & 7
- Connect Cable 7 positive (red) directly to a customer-supplied circuit breaker corresponding to the seawater pump current overprotection rating (max 15 A), then to the dedicated battery isolation switch.
- Connect Cable 7 negative (black) to the DC main negative bus bar or battery minus terminal.
- Connect Cable 5 receptacle end (pins) to Seakeeper 1 SW Pump 12 VDC Out and the plug end (sockets) to customer-supplied 12 VDC seawater pump cable Deutsch connector termination.
6.2.2.3 Ground Connection: Cable 6
- Butt splice Cable 6 to customer-supplied ground wire, 4 AWG, with sufficient length to reach the vessel ground.
- Vessel grounding bus to comply with:
- EM/IEC 60204-1 Clauses 6.3.3 and 8.2.3.
- ABYC E-11 July 2018 Clauses 11.5.2 and 11.16.1.
6.2.2.4 Seakeeper Display Connection
- Ensure a compatible Multifunction Display (MFD) is available. Refer to Seakeeper MFD Compatibility Technical Bulletins.
- Connect Seakeeper Compatible MFD
- Purchase custom Seakeeper MFD integration cable based on the compatible MFD onboard.
- Connect Cable 10 to ethernet connection of Seakeeper ConnectBox.
- Connect 4 pin end of MFD integration cable to male end of Cable 10 and Ethernet M12 end of MFD network port or vessel network hub.
6.2.2.5 NMEA 2000 Network Connection
- NMEA 2000 Compatible GPS signal required for installation of Seakeeper 1.
- Connect Cable 11 to ConnectBox NMEA port.
- Route Cable 11 to vessel NMEA backbone and connect.
6.2.3 Cooling Checklist
- Purchase seawater pump for Seakeeper 1 to provide 2 – 4 GPM (7.6 – 15.1 LPM) with a max overcurrent protection rating of 15 A.
- Optional seawater pump can be purchased through Seakeeper, P/N 30331.
- Connect and route seawater inlet hoses from seacock valve to the seawater strainer, seawater pump, then Seakeeper 1 heat exchanger.
- Connect and route seawater outlet hoses from Seakeeper 1 heat exchanger to the seawater overboard.
- Test seawater pump.
- Verify 2 GPM (7.6 LPM) minimum and 4 GPM (15.1 LPM) maximum seawater flow through heat exchanger under all operating conditions of the vessel.
- Verify coolant level in heat exchanger coolant reservoir, fill if needed.
6.3 Start Up Checklist
Refer to Seakeeper 1 Operation Manual, Section 2 for detailed start up instructions.
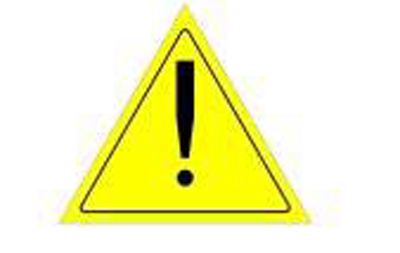
Prior to beginning the start up sequence all previous Sections of the Installation Manual for Mechanical, Electrical, and Cooling installation must be complete. Before continuing, the Seakeeper 1 cover must be installed and the operating clearances must be clear of personnel and equipment.
- Remove lifting bolts and install sealing bolts and washers into lifting eye holes and install cover.
- Energize battery isolation switch, high current 80 A breaker, and seawater pump breaker.
- Verify display is active and no alarms are present.
- If the Seakeeper 1 display does not activate, turn off both circuit breakers immediately and check all wiring connections.
- Override seawater pump “on” (at 0 RPM hold down SERVICE Button, wrench icon, for 5 seconds) and verify flow at seawater outlet.
- Press Seakeeper ON/OFF Button and follow instructions in Seakeeper 1 Operation Manual, Section 2 for complete start up instructions.
- Verify that no ALARMS are present.
- Power Seakeeper 1 down. The Seakeeper 1 flywheel will take 2+ hours to coast down to 0 RPM.
7.0 Revision History
REVISION | DESCRIPTION | DATE |
1 | Initial release | 22MAY2020 |
2 | Mk1 ConnectBox release, Additional installation details added. Removed 5-inch display references. | 11APR2025 |