Seakeeper 1 Installation Manual (90519-1) 1-202-0001 to 1-233-0630
Mechanical Installation
Mechanical Installation Introduction
The Seakeeper 1 can produce forces of up to 1,515 lbs (6.74 kN) in the vertical direction, 2,248 lbs (10.0 kN) in the longitudinal direction, and 1,697 lbs (7.55 kN) in the lateral direction at each of the four mounts. Careful consideration should be given to foundation design to ensure it is capable of safely transferring these loads into the hull. These loads represent a worst-case operating condition that includes a 6 G acceleration evaluated in each direction independently. The responsible party for designing the supporting structure (boat builder, installer, or hired sub-contractor) must accommodate the above forces plus a reasonable factor of safety. Seakeeper recommends a minimum safety factor of 2.0 (yielding in a safety margin of 1.0).
It is assumed that the installer is familiar with mounting using mechanical fasteners to marine structures and has performed structural analysis to ensure the structure to which the Seakeeper mounts can properly transfer the loads the Seakeeper exerts into the hull structure. If the installer has any doubt about the ability of the structure to transfer the loads to the hull, then the installer should contact a licensed naval architect or engineer to perform a structural analysis.
The installer should review the following list of reference drawings to ensure the mechanical installation procedure is fully understood.
Reference Documents & Drawings:
Link to Seakeeper 1 Reference Documents
- 90510 – Seakeeper 1 Hardware Scope of Supply
- 90515 – Seakeeper 1 Crate Unpacking Instructions
- 90516 – Seakeeper 1 Bolt-in Installation Details
- 90514 – Seakeeper 1 Bolt-in Clearances
- 90559 – Seakeeper 1 Generic Installation Guide
- 90517 – Seakeeper 1 Installation Fixture Kit
- 90628 – Seakeeper 1 Deck Cover Enclosure
Precautions
- The Seakeeper must only be lifted from the supplied lifting eyes (see Section: Transport and Unpacking).
- The Seakeeper flywheel is supported by precision bearings. While unpacking and lifting the Seakeeper assembly, DO NOT drop or impart mechanical shock as damage to bearings could result.
- While handling / installing the Seakeeper assembly, protect exposed hydraulic brake cylinder rods (see Figures 1) from scratches or damage as this could lead to premature seal failure and oil leaks.
- The Seakeeper must be installed in a dry location (within a leaning post or in a lazarette). Use the deck cover enclosure if installed and exposed to weather (P/N 90628).
- Exercise care to protect any exposed surfaces as damage to finish could lead to early appearance degradation of the Seakeeper.
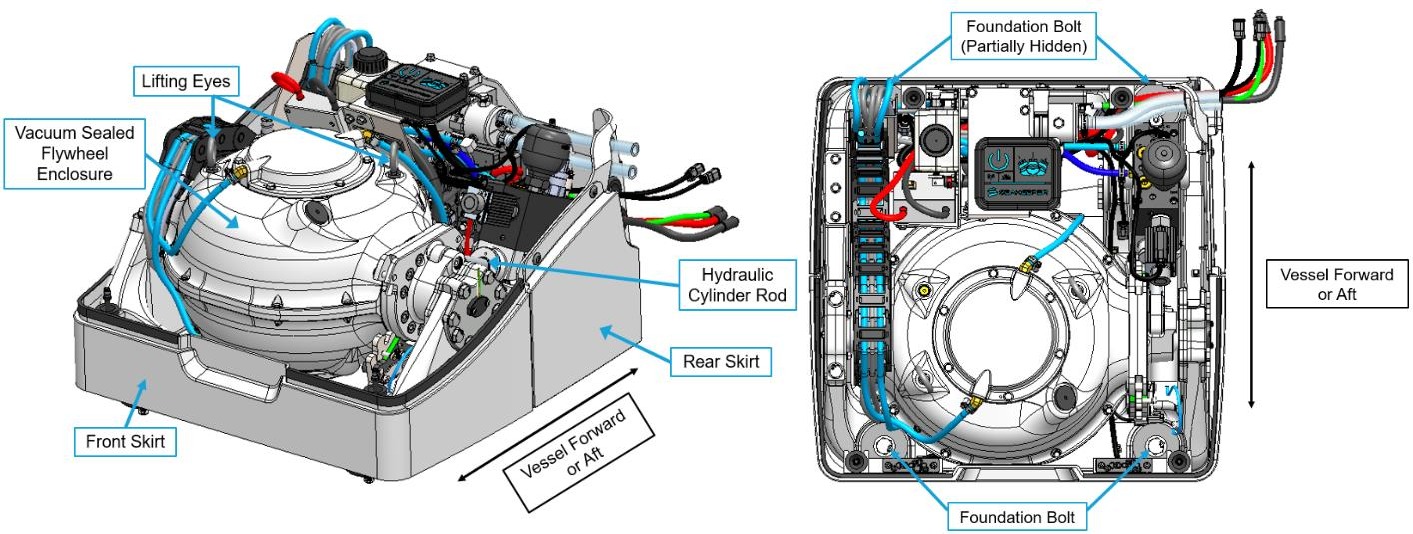
Selection of Seakeeper Installation Location
Selection of mounting location of the Seakeeper should consider the following desirable features:
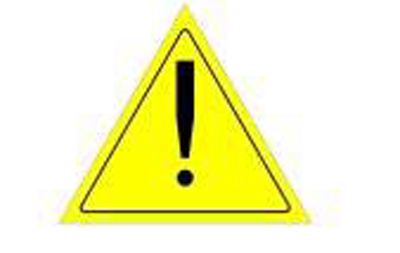
The Seakeeper should be installed aft of amidships to minimize high acceleration loadings due to hull/wave impacts during operation at high speed or in large waves. If the only possible Seakeeper location is forward of amidships, then the installer should have Seakeeper review the installation location prior to finalizing the design.
- Top-down access or sufficient clearance for access and removal of the Seakeeper 1 cover is required. See Drawing No. 90516 – Seakeeper 1 Bolt-In Installation Details and Drawing No. 90514 – Seakeeper 1 Bolt-In Clearances for reference.
- Provide adequate clearance for all recommended scheduled maintenance and any repairs that may be necessary, as shown in Figure 3 and Drawing No. 90516 – Seakeeper 1 Bolt-In Installation Details.
- Access for the removal and re-installation of the Seakeeper 1 should be considered.
- The Seakeeper should be installed in a dry space to minimize effects of corrosion. Use the deck cover enclosure if installed and exposed to weather (P/N 90628).
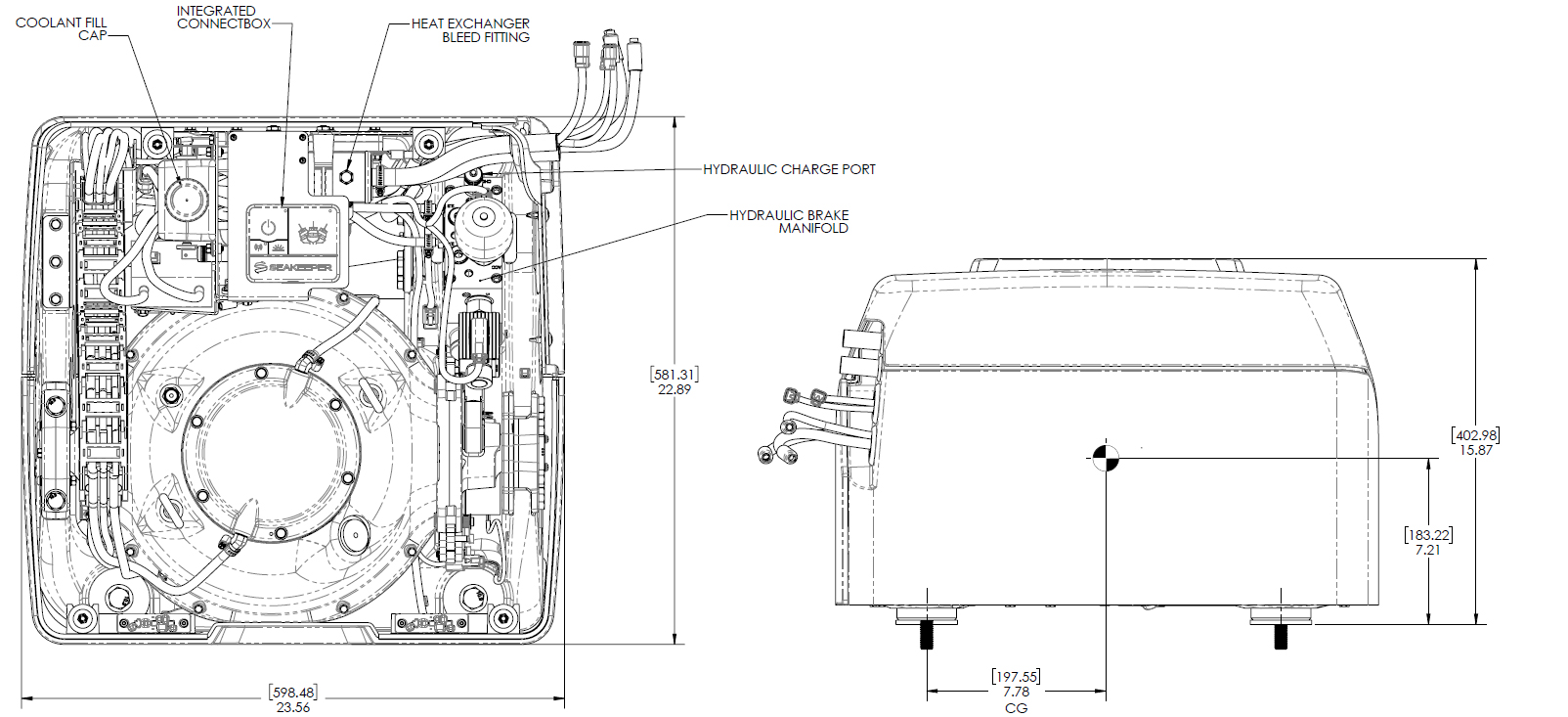
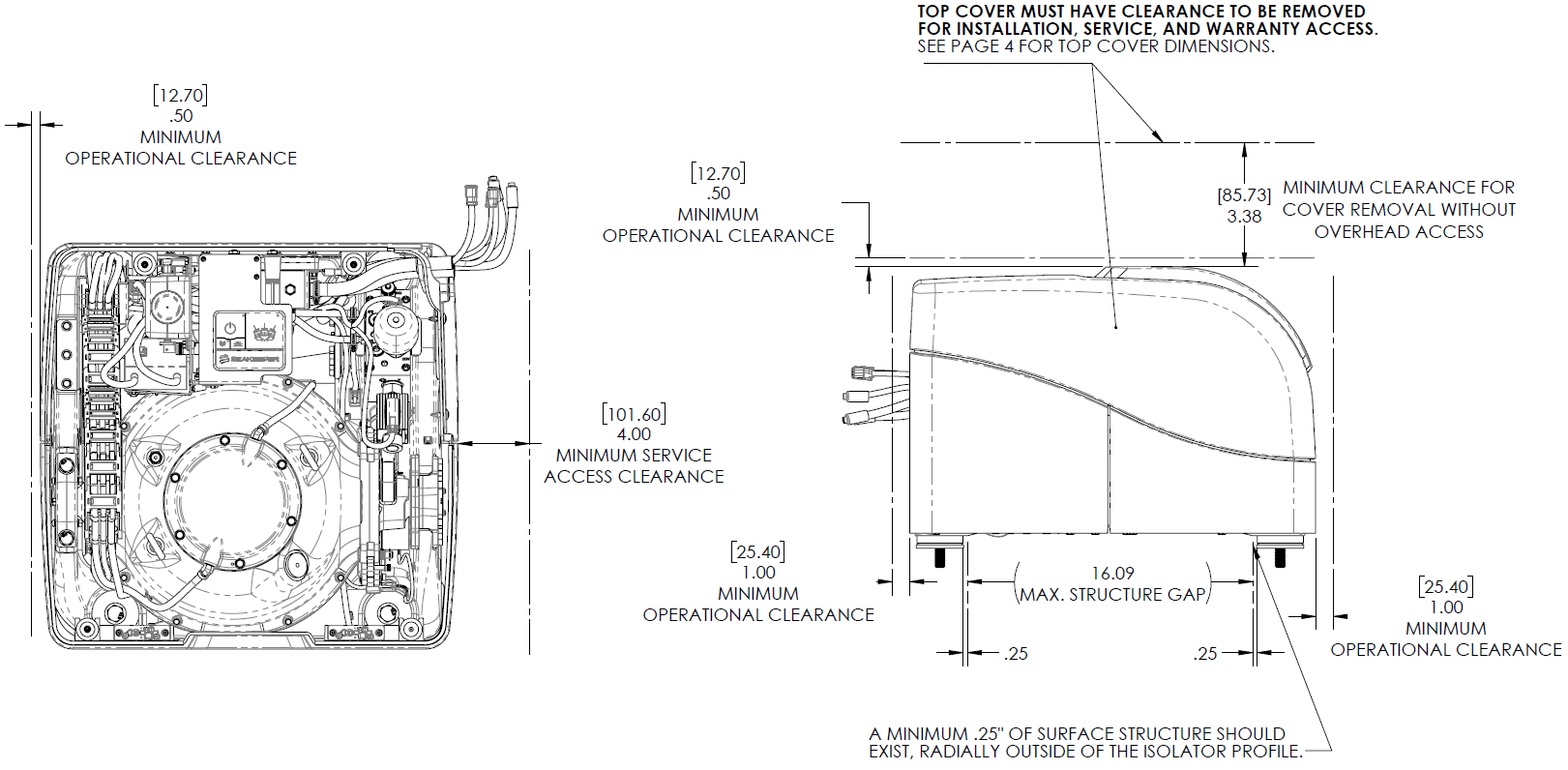
Figure 3 – Seakeeper 1 Service and Operating Clearances (Drawing No. 90516)
Note: Adequate access to remove the Seakeeper 1 cover must be incorporated into the installation design to allow for regular maintenance, service, and repair of components.
Safety
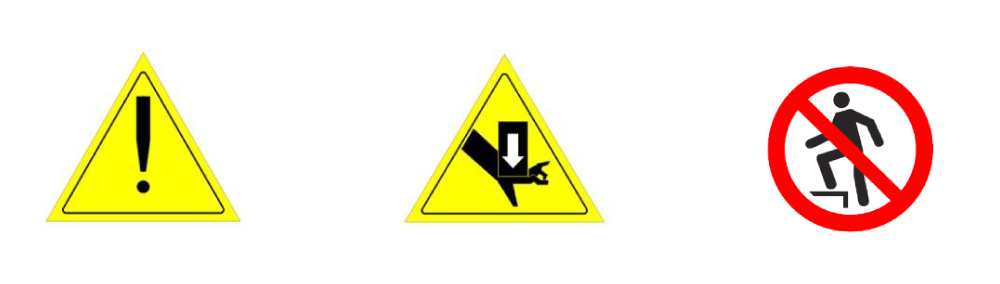
There is a large torque about the gimbal axis when the Seakeeper is precessing. The Seakeeper 1 enclosure is provided to prevent personnel or equipment from contacting the Seakeeper while it is in operation. These covers should not be stepped on or have anything placed on top. The covers should always be in place during operation. If it is ever necessary to access the Seakeeper while the flywheel is spinning, the Seakeeper must be locked at the display to stop the Seakeeper from precessing. Seakeeper regular scheduled maintenance should only be performed by authorized personnel when the Seakeeper is locked and the flywheel has stopped spinning.
Noise and Soundproofing
Seakeeper noise has been measured under steady state conditions (no wave load) in Seakeeper‘s Engineering Lab and in our Factory Demo Boat. The steady state noise at 1 meter is typically in the range of 62-64 dBC un-weighted. As the frequencies emitting the highest sound pressures are low (like other marine machinery), it is recommended that the Seakeeper be installed in an enclosed space such as a leaning post / seat, bilge, center console, or machinery space.
Transport and Unpacking
Transport
- Use a Seakeeper-provided shipping crate for transport, P/N 12098. The overall dimensions of a fully-packed Seakeeper 1 crate are 27.5 L x 27.5 W x 23.25 H in. (0.70 L x 0.70 W x 0.60 H m) with a weight of 430 lbs (195 kg), including accessories.
- Seakeeper 1 crates can be stacked up to two (2) units high. Only like units should be stacked. i.e., Seakeeper 1 on top of a Seakeeper 1
- Both air and ground transport are acceptable and available through Seakeeper.
- Seakeeper shipping crates must be transported in environmental conditions between -4°F and 140°F (-20°C and 60°C).
Unpacking Crate
Reference Drawing No. 90515 – Seakeeper 1 Crate Unpacking Instructions, for detailed unpacking instructions. Once the Seakeeper 1 crate has been unpacked, follow these instructions when lifting the unit:
- Remove and set aside cover, electrical components, cables, and misc. items.
- Attach Small Gyro Lifting Bar Kit, P/N 11766, to the two lifting eyes located on the top of the Seakeeper enclosure.
- Stay clear of the Seakeeper 1 when the unit is being lifted and use safe practices for working under a suspended load. The Seakeeper 1 weighs 365 lbs (165 kg).
- See Figure 4 for proper lifting arrangement. Additional details can be found in Drawing No. 90516 –Seakeeper 1 Bolt-In Installation Details.
- Remove lifting eyes once unit is installed. Lifting eyes must be removed prior to operation.
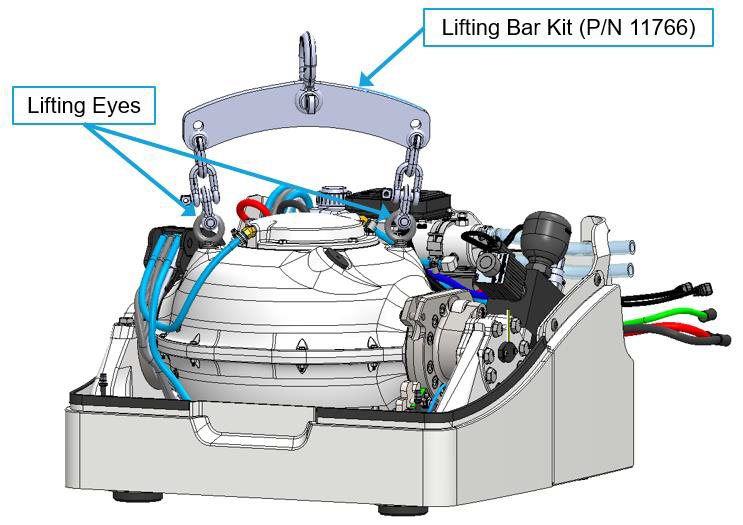
Figure 4 – Seakeeper 1 Lifting Arrangement
Mechanical Installation
Reference Documents & Drawings:
- 90559 – Seakeeper 1 Generic Installation Guide
- 90514 – Seakeeper 1 Bolt-In Clearances (Gives details of bolt stack also)
- 90516 – Seakeeper 1 Bolt-In Installation Details
- 90517 – Seakeeper 1 Installation Fixture Kit
- 90599 – Seakeeper 1 Bolt-In Kit
Preparation of Vessel Structure
Drawing No. 90559 – Seakeeper 1 Generic Installation Guide, shows various structural arrangements to support the integration of the Seakeeper 1. The Generic Installation Guide offers above and below deck installation arrangements with fiber-reinforced plastic (FRP) and aluminum structures, which should provide solutions for most vessels. Depending on the structure to which the Seakeeper is fastened, blind threaded holes or through-bolting can be utilized. The Seakeeper 1 is affixed to the hull via four bolts in the Seakeeper 1 frame. Each Seakeeper 1 foundation bolt has a vibration isolation assembly to minimize the transmission of vibrations to the hull structure.
Refer to Seakeeper Drawing No. 90516 – Seakeeper 1 Bolt-In Installation Details. This drawing contains critical design dimensions and loads that must be considered in the design of the boat’s structure that will receive the Seakeeper 1. It is assumed that a proper structural analysis has been performed for the vessel structure to which the Seakeeper will be fastened to ensure proper strength margins for the loads the Seakeeper will create during operation.
The vessel structure supporting the Seakeeper should be installed so the Seakeeper is parallel to the waterline in the transverse direction and within 2 degrees longitudinally.
In addition, the four areas on top of the structure on which the Seakeeper 1 will rest need to be co-planar within .06 in. (1.5 mm) to minimize potential distortion of Seakeeper isolation mounts when installed.
Seakeeper offers an installation fixture kit, P/N 90517. The fixture has 4 holes located at the same centers as the mounting holes on the Seakeeper 1. The fixture locates the hole patterns at the proper spacing both in the forward-aft direction and the port-starboard direction. See Figure 5 for more details regarding the Seakeeper 1 template.
Note: Do NOT use the installation fixture to establish the Seakeeper envelope dimensions or clearances. Refer to Drawing No. 90516 – Seakeeper 1 Bolt-In Installation Guide, for envelope dimensions. A 3-D model of the Seakeeper 1 is available on the Seakeeper website www.seakeeper.com to aid in designing the Seakeeper foundation and the space around the Seakeeper.
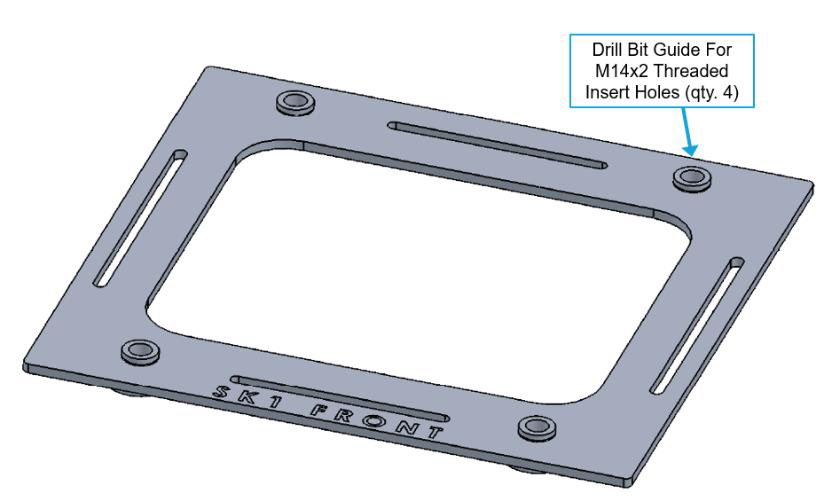
Transfer of Holes to Boat Structure
The following instructions should be used to establish the Seakeeper 1 bolt pattern on the hull structure that has been designed to accept the Seakeeper 1, based on the information provided in Drawing No. 90599 – Seakeeper 1 Bolt-In Kit and Drawing No. 90516 – Seakeeper 1 Bolt-In Installation Details.
- Lower installation fixture onto vessel structure.
- The four Isolation Mounts, where the Seakeeper 1 contacts the hull structure, must be coplanar to within 0.06 in. (1.5 mm).
- Align fixture in desired location and transfer holes from fixture plate to the vessel structure by transfer punch. Note that holes in fixture plate are ø9/16 in. (14.287 mm).
- Using the bushings in the fixture holes as a guide to stay perpendicular with the vessel structure, drill 4 X 9/16 in. diameter holes for M14 x 2.0 1.5xDIA (21 mm length minimum) threaded inserts in vessel structure at marked locations to mate with holes in the Seakeeper foundation.
- Tap threads in holes for M14 x 2.0 1.5xDIA threaded inserts.
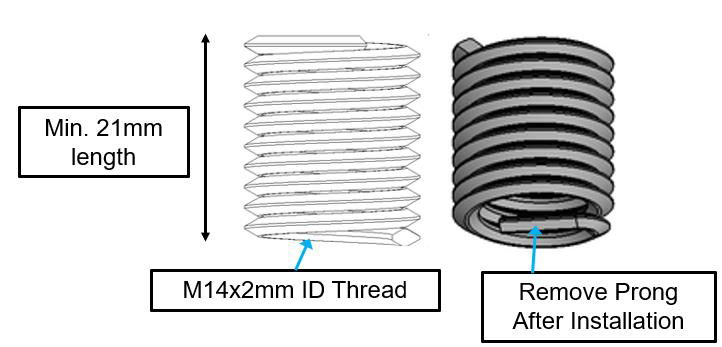
- Install threaded inserts into holes using Helicoil installation tool.
- Remove threaded insert prongs after threaded inserts are installed.
Installation of Seakeeper
- Locate and position the lower snubbing washers onto vessel foundation structure at each of the 4 hole locations.
- NOTE: Sealant or caulk is recommended to be applied around the outside edge of the lower face of each lower snubbing washer, where it contacts the vessel structure. This will maintain the position of the snubbing washer and prevent water from wicking between the parts and setting up corrosion.
- Sealant is not required between the snubbing washer faces and isolator bushings.
- Lower the Seakeeper 1 onto the lower snubbing washer on the vessel structure and align over drilled holes.
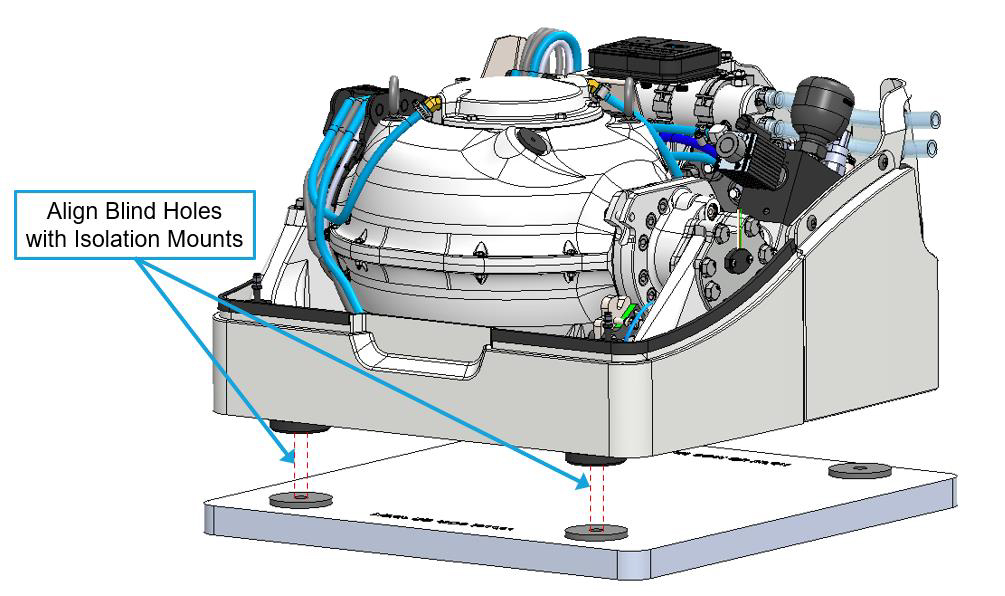
- Using a flexible extendable magnet (McMaster P/N: 3838A42 or similar), install the Seakeeper 1 Bolt-In Kit – P/N 90599: isolator mount sleeve tube, upper snubbing washer, wedge-lock washer, and bolt at each isolation mount.
- Figure 8 shows an exploded view of the Bolt-In Kit.
- Before installation, apply a moderate coat of anti-seize to the threads of each bolt.
- Insert an isolator mount sleeve tube in each of the four vibration isolator assemblies.
- The upper snubbing washer, wedge-lock washer, and M14 Bolt can be stacked as one assembly by attaching the magnet to the snubbing washer.
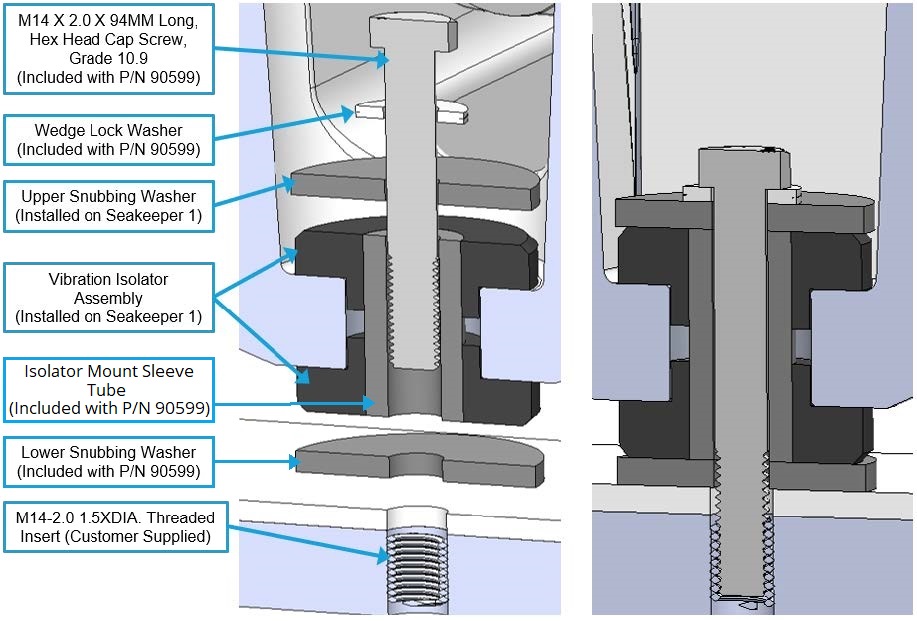
Figure 8 – Seakeeper 1 Bolt Stack Arrangement Exploded (left) / Installed (right) (P/N 90599)
- Torque all fasteners to 115 ft-lbs (156 N-m). New bolts must be used for each installation and re-installation.
- Threaded inserts can be reused if they are found to be intact and without damage.